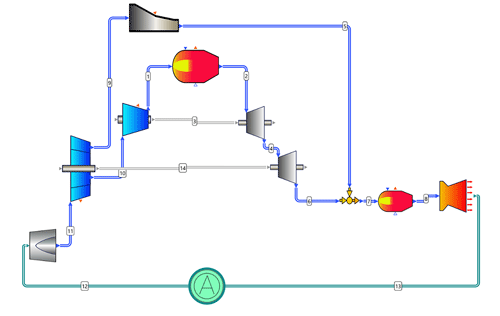
The word “sensor” in a pumping application can mean many different things: an oxygen sensor in a wastewater treatment plant, a pressure sensor in condensate system piping, a toxic gas sensor at the discharge of a scrubber, a fuel level sensor in a backup generator, etc.
Fluid conditions to be monitored are spread all over a pumping system. Sensors are tasked with checking these key parameters, from the core of the system to the fringes. Most of these sensors are set to monitor system outputs—pressure, flow, oxygen content, dissolved solids, toxic gases, etc. These are all important parameters, but most fundamental among all the sensors in the system are the ones that monitor the pumps and fans themselves. For example, are they running, and are they likely to keep running?
Why is pump or fan run status and health the most important system information to monitor? It seems simple, but it is worth reflecting on for a moment. What happens in a system when the pump or the fan does not run? In a cooling system, a fan failure can cause the associated compressor to overheat and fail, shutting down the system completely.
How about a water/wastewater application? In a wastewater system, a pump failure can result in an untreated sewage discharge, endangering people and creating a cascade of secondary public safety impacts. How about potable water? In a potable water system, a failed pump means the water flows no more.
Now consider pump and fan monitoring. What sensors can be used to accomplish this? Users can set up monitoring conditions in the pipe or duct. Pressure, flow and temperature sensors can be placed in piping to evaluate the status of a pump and can tell the user if the pump is operating or not. If the pump or the fan shuts down, these sensors will detect the reduction in pressure or flow or the change in fluid temperature. Additionally, when the relevant setpoint in the control system is reached, the pump shutdown will be signaled. This works, but is it the only way? Further, is it the best way?
There is another way, and that way is to move upstream in the system. Upstream, in this case, does not mean moving to the suction side of the pump to monitor conditions—what this means is a move to monitor the electrical power feeding that motor. Think about talking upstream but in the electrical sense. The sensor type to use here is a current sensor, typically an alternating current (AC) sensor. These sensors are placed in the electrical feed to the motor and can be set to trip at an overcurrent (for something like a jammed impeller) or undercurrent (loss of suction) condition.
A change in current will send an output signal, notifying the control system of an unwanted event. This type of sensor is designed with fixed or adjustable trip points and can be ideal for providing information on AC electrified equipment in pump and fan applications.
There are several reasons why these sensors are used:
- They are simple to install and use since some require no external source of power at all and can be simply clamped around the power feed cable to the pump without disconnecting that cable.
- They are relatively inexpensive since they do not need the environmental protections required for sensors that mount into or within the fluid side of the system.
- They are a leading indicator signaling the change in the pump parameters long before a change in the fluid environment.
- They are smart—with versions that can learn the characteristics of a user’s system and look for changes outside the norm.
Beyond system performance monitoring and motor protection, what else can these sensors do in a pump or fan application that other sensors might struggle to do? Because they are in the electrical feed to the motor, they can also monitor power consumption. This can be important since pumps can consume up to 25% of the energy in applications like water and wastewater.
Versions of these current sensors can pass analog current signals to the control system with the signal level proportional to the current flow to the motor. With simple signaling and display devices, these sensors can help operators adjust and balance loads to utility pricing structures, thereby reducing cost of power. Long-term monitoring of this data can also signal slowly developing problems with pumps and fans, to allow for needed service or maintenance in a planned evolution long before a motor failure takes a system down.
There are many ways to sense parameters in a fluid system. Keeping it simple, with current monitoring for
pump and fan parameters, can often be the easiest, most cost-efficient and effective way.