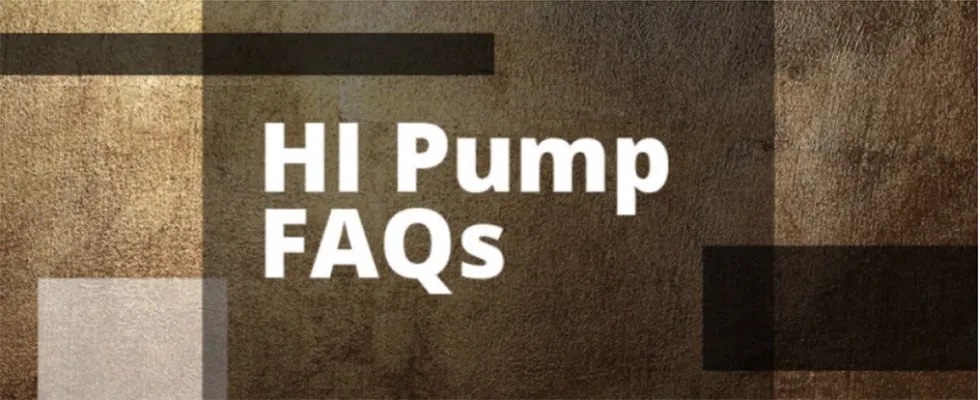
In the context of pumps, bearings carry the loads associated with pumping, and lubrication is the process through which bearings minimize friction and energy loss. Without proper lubrication, heat due to friction will result in premature wear or failure.
The most important qualities of a lubricant are its heat resistance and viscosity, which determine the applications for which it is most ideal and the methods in which it is applied. To properly lubricate bearings, a protective film must be maintained at all times during operation.
Focusing on horizontal pumps with rolling element bearings, lubrication is typically grease or oil. For grease lubrication, the grease is packed in the bearings and may require periodic regreasing (Image 1). Oil lubrication is applied with multiple methods, but similarly to grease, it will need to be maintained to ensure lubricating properties are maintained.
Grease lubrication is typically used in lower horsepower applications. Grease lubrication resists moisture ingress, is less sensitive to level pump installation, has a simpler maintenance process and may be preferable for stop-start applications.
Oil bath lubrication (Image 2) can be applied by maintaining the oil level just above the outer race of the bearing, or oil splash lubrication can be applied by an oil ring or rings that rotate on the shaft and splash oil from the oil reservoir onto the bearing. In these types of lubrication, it is vital to maintain an optimal level of lubricant in the bearing housing. Too much oil will result in a reduction of the outer bearing race’s or oil ring’s ability to distribute oil to the bearings, frothing of the oil and excessive friction. Too little oil will result in the bearings not receiving enough lubricant and could potentially lead to rapid failure.
Oil lubrication can also be done with an atomized mist that is forced into the bearing housing. Oil mist lubrication can be classified as pure and purge oil mist lubrication (Image 3). Both involve the same core process, wherein a constant mist of oil is applied directly onto the bearings as they operate. Purge oil misting, however, includes a reservoir of oil within the housing, creating a wet sump. Pure oil misting is advantageous because it can be used at a lower operating temperature and consumes less oil than oil bath or splash lubrication while also inducing fewer wear particles into the bearings. Purge oil misting can also be used at lower operating temperatures than oil bath/splash lubrication and carries an advantage over pure oil misting in that the oil level is clearly visible and easily maintained.
The best lubrication for an application is a balance of equipment design, application requirement, maintenance preferences and cost, which requires careful consideration of all factors involved. The topic of bearing lubrication is explored more in depth in the “Proper Lubrication Methods for Bearings” white paper published by the Hydraulic Institute.