This equipment exploits the elasticity of synthetic rubber and ensures stable bearing behavior.
08/17/2015
After 30 years of research, an engineering team in Japan has developed a hybrid-type submersible bearing that prevents burnouts during vertical pump dry-starts, exploits the elasticity of the synthetic rubber to level the pressure during typical operation, and ensures stable bearing behavior by conferring vibration control while supporting the rotating shafts. Using polytetrafluoroethylene (PTFE) strips as slide members and synthetic soft rubber for cushioning between the slide elements and metal shell (or the base plates), the hybrid bearing can be used for dry-start operation of vertical pumps without applying lubricating water from the outside prior to pump operation.
Advantages of Adopting a Dry-Start Bearing
A wet-start vertical pump system requires that water be injected from outside the pump into shaft protection tubes at the top of the column pipes before operation. In most cases, the water is pumped up automatically after a fixed time to avoid wasting the feed water pump power or the water from the tap, which is usually called self-feed water. A dry-start pump does not require lubrication and is less prone to environmental damage from crevice corrosion in joint parts where seawater remains. Because the stainless steel shafts are exposed directly to the pump main flow, pitting corrosion—prone to occur in low-flow-velocity or stagnant regions—is reduced.Structure of Hybrid Bearings
Three molds have been developed to produce three types of bearings, each suitable for a different range and scale of application. These include full-molded, segmental and barrel type bearings. Bearings are basically composed of four layers: PTFE strips as slide elements, synthetic rubber for cushioning, base plates as the backing-plates and a metal shell that serves as the holder. The full-molded bearing is used almost exclusively for vertical pumps, making a simple, three-layered structure as shown in Figure 1.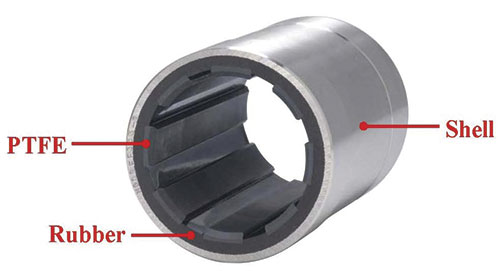
Friction Coefficients
Creating submersible bearings with materials that have low friction coefficients has been a top priority for submersible bearing manufacturers. Figure 2 shows friction coefficients in tap water of different bearing materials (PTFE, polyether ether ketone [PEEK] and polyurethane in hybrid structure with rubber) used in dry-start vertical pumps and rubber bearings used in wet-start pumps. Friction coefficients were obtained using identically structured bearings to match test conditions.
Effects of Synthetic Rubber
Friction coefficients obtained using the two test bearings during wear resistance testing indicate that the test bearing with the persistently soft rubber layer (72 Shore A hardness) has a lower friction coefficient than the bearing with the rubber layer turned into ebonite (80 Shore D hardness). This suggests that the rubber layer may prevent sharp rises in the local pressure on the bearing conferred by the shaft deflection. The rubber seems to keep pressure low overall and limit the solid contact friction areas. The free surfaces of the rubber made by or among the PTFE strips may improve the elastic effect compared with the bearings without free surfaces facing the shaft, as with a the bearing with a monolithic ring-like structure of metal and resin.1 The balance between the number of grooves and the size of the area in which the water film formed to lower the friction coefficients is important. If the number of grooves is increased to enhance the elasticity of the rubber, the size of the water film area will decrease and invite the larger friction coefficients and vice versa. Because the pump shafts of the vertical pumps are suspended on the center of the column pipes, the bearing load by the shaft weight is comparatively small, which is typical with vertical pumps. This reduces the importance of self-alignment, but another problem may emerge.Adhesive & Abrasive Wear Resistance
Wear resistance related to adhesive wear and the abrasive wear of the slide members is an important factor for submerged bearings from the viewpoint of tribology. Figure 3 shows the results of an adhesive wear test on two pieces of same-sized bearings. One was the PTFE and rubber hybrid bearing, while the other contained abundant sulfur and was vulcanized to harden the rubber into ebonite with the hardness of 80 Shore D.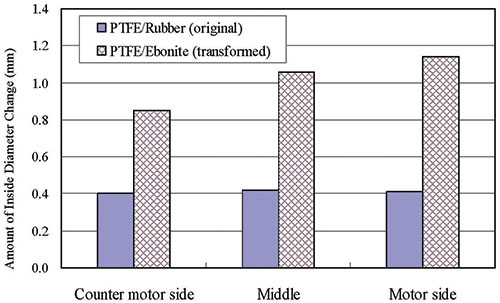
Absorptivity of Shaft Vibration
In addition to the effect on friction coefficients, the rubber layer also affects shaft vibration control. A viscoelastic material like rubber suppresses the self-excited or sub-synchronous vibration that is caused by the strong nonlinearity of the bearing characteristics and tends to appear when loads are small, as in the case of the shafts of vertical pumps. Figure 4 shows the peak-to-peak amplitude measured on a bearing spider fixed on the middle part between the column pipes of the test pump in operation. The inside radiating spokes holding the bearing in the shaft center were replaced with rods extruded from the load cells to measure the bearing load. This pump was 6 meters long under the floor. A 200-millimeter bored vertical pseudo-pump with three bearings (upper, middle and lower) was fixed in the bearing spiders. The impeller of this pseudo-pump was replaced by a rotating disk with the same rotating inertia to cease its pumping action.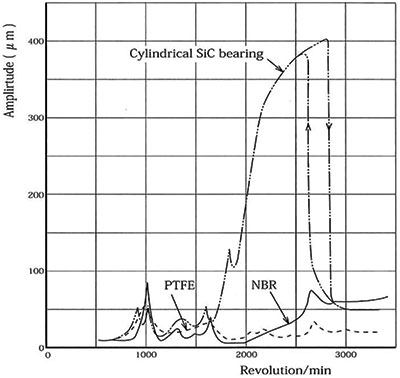
Acceptability of Dry Runs
Figure 5 shows the threshold of the possible dry-start continuing time relative to the bearing pressure in an experimental run at a progressively higher shaft speed. The plot shows a nearly inverse relationship between the dry-run continuing time and bearing pressure. As expected, the bearing pressure remains low on the vertical pumps as long as their assemblies and alignments stay normal. The dry run can presumably be extended to a few minutes.
Acceptability of a Lack of Lubrication Water
A lack of lubrication water arises when some force or phenomenon intercepts the flow of replacement water to or from the bearing surroundings. Assuming a cutoff of the passage of lubricating water to and from the bearing, the test bearing was sealed in an experiment using the oil seals at both ends after immersion in water. The bearing temperature was measured in the vicinity of the bearing surface.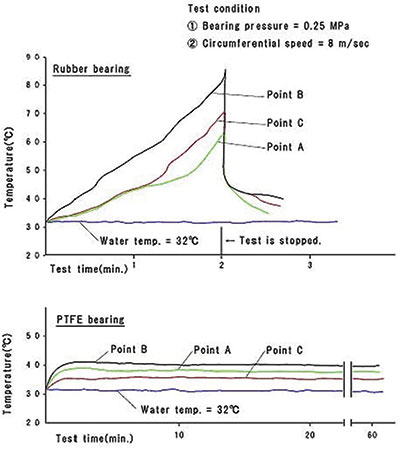
- Satoh H., Okada K., Furukawa S., 1994a, 'Influence of Grooves of Compound-Structured Submerged Bearings for Vertical Pumps,' Transactions of the Japan Society of Mechanical Engineers, Vol.60, No.571, pp.1033-1038.
- Satoh H., Takeda H., 1989, 'Dry-Start Bearings for Vertical Pumps,' Proceedings of 6th International Pump Users Symposium, pp. 75-82.
- Kikkawa F., Ogawa R., Satoh H., 2010b, 'PTFE submersible dry-start bearings,' World Pumps, No.531, pp.31-34.
- Kikkawa F., Ogawa R., Satoh H., 2010a, 'PTFE submersible dry-start bearings,' World Pumps, No.530, pp. 30-33. Satoh H., Takeda H., Kikkawa F., 1988, 'Dry-Start Bearings for Vertical Pumps,' Journal of Turbomachinery Society of Japan, Vol.16, No.7, pp. 382-390. Satoh H., Sugiya T., Okada K., Yamada S. 1994b, 'Influence of Submerged Bearings for Vertical Pumps on Vibration Characteristics,' Transactions of the Japan Society of Mechanical Engineers, Vol.60, No.578, pp.3233-3237.