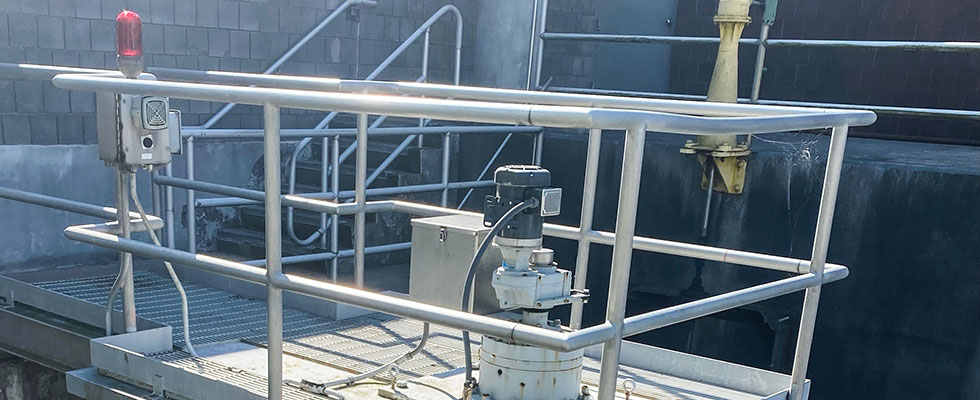
Implementing an automation strategy that integrates sensors throughout the water utility with intelligent software that delivers an integrated operational view makes sense. The ability to know the state of an organization’s most important assets, including pumps, blowers, mixers and sludge collectors, is vital to the safe, efficient running of the utility.
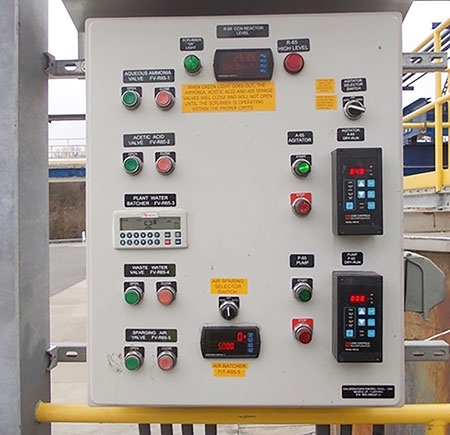
Motor, Pump & Mixer Blade Protection
Because motor power sensors and controls can determine small changes in motor workload, they are most frequently used to protect motors and their associated equipment, such as pumps and mixer blades. The motor power data that reflects when a pump is clogged, jammed, loses its prime or suffers impeller damage, allows the motor to be shut off before expensive pump damage can occur.
Similarly, a long mixer arm, attached to a motor through a highly geared linkage will indicate when the arm has encountered an unexpected workload, perhaps a greater viscosity or an obstruction. This changed motor load can be acted upon by the motor power control, signaling a potential concern or acting as an electronic shear pin, shutting the process down before bent blades and damaged linkages can put the equipment offline for lengthy repairs.
Monitoring Operations
When used in concert with an existing supervisory control and data acquisition (SCADA) system, motor power sensors can offer important insights that validate the efficient running of the utility, as well as enable a higher throughput configuration. By comparing motor power data, which closely tracks pump and mixer work completed, flow data and other operational throughput metrics can be checked for accuracy and consistency.
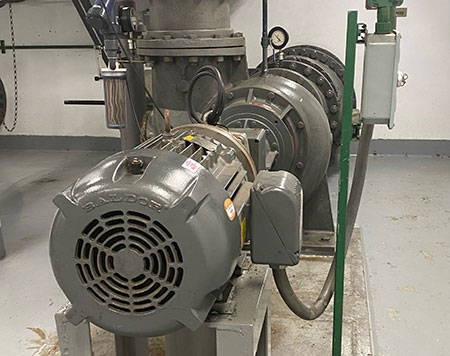
Because motor power is an accurate measure of flow and work, it is useful in tracking output metrics in ways that vibration, level and pressure may not. An additional benefit to operations is the ability to run the entire facility with confidence that motors and downstream pumps and mixers are protected. It is not uncommon for water and waste utilities to hold back a percentage of standby mixing and pumping capacity to ensure there are capabilities in the event of a failure. By monitoring motor power, all production capacity can be put into service, and exceptions highlighted by increases or decreases in power can be dealt with sooner, avoiding downtime.
Energy Efficiency
Many water and waste utilities spend between 65% and 80% of their total energy bill to power their pumps. Motor power can provide important insights into how to lower this energy bill. By monitoring power trends of individual motors over time, water utilities can understand which assets are the largest contributors to expense. Some options to address the cost of energy include:
comparing pump, mixer and blower motor power sensor readings to nameplate power ratings of the motors, enabling correct sizing of motors over time
using motor power as an additional data point (along with pressure and flow) to ensure how close to best efficiency point (BEP) pumps are operating
comparing pumps with similar configuration, sizing and workload to pinpoint pumps that are not as efficient as their peers, potentially highlighting maintenance needs
understanding the individual motor contribution to peak workloads throughout the day, providing the roadmap for staggering schedules or workloads to reduce peak energy surcharges
Short-Term vs. Long-Term Installation
Motor power sensors are available as portable devices that can be useful in an energy audit. When used as part of a regular motor energy assessment program, the ability to get power data across the enterprise’s pumps, mixers and blowers can unlock many of the energy efficiency insights listed. Leveraging permanently attached motor power sensors can offer the equipment protection benefits and offer longer-term data benefits.
The option to review motor power changes over time gives the context of improvements or degradation to motor and pump health and efficiency. The ability to integrate power data with supervisory control and data acquisition (SCADA) information also enables a link to be drawn between energy usage and water pumped or waste treated.
Getting Started, Getting It Funded
A pilot project that connects to several pumps and mixers will typically yield a great deal of insight into the potential savings of a broader deployment. Comparing pump power data with flow information will show overall efficiency and potential opportunities for improvements. This data can form the basis of a proposal to move the project beyond a pilot phase.
The same cost savings insights may also be used to align the larger project with energy equipment rebates from your local electrical utility. Many energy providers offer formal programs for funding this type of investment if it can be directed toward energy saving results. The power sensors that offer so many operational benefits may actually be subsidized or free.
Installing motor power sensors and controls is an important step to protecting motors, pumps and mixers. Many additional operational benefits come with this investment: the ability to validate workload and healthy operations, the data necessary to ensure operational efficiency and the potential to map the energy use of the entire water utility with the insights for lowering overall energy expense. Pilot projects for motor power sensors and controls can highlight the potential savings and the opportunity for energy utility cost sharing programs.