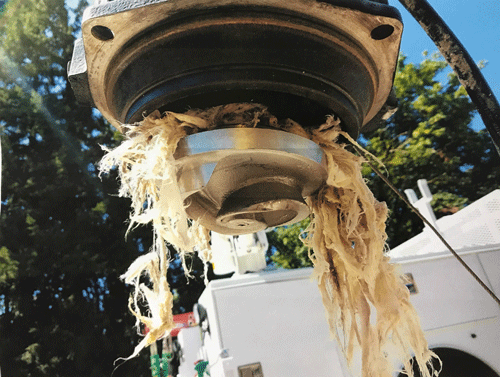
Nothing acts in isolation. Technology connects the entire world, so it is no coincidence that this year’s WEFTEC theme is “Create Connections. Transform Tomorrow.” The pump industry will benefit from more connected real-time control and risk mitigation, especially in wastewater processing and treatment applications. Here, pump system operators’ constant concerns are ragging, pump equipment failure and storm event spillage.
Isaac Newton’s Third Law states that every action has an equal and opposite reaction. Similarly, for every action in the wastewater industry, there is a multitude of connected reactions. Therefore, the aggregate result can provide positive or negative outcomes depending on how each action and reaction affect one another.
This connected world aims to use these interconnected actions to drive positive results and avoid negative consequences.
The Perils of Ragging
Take an everyday example to look at some interconnected actions needed to drive positive solutions in the wastewater industry. Too often, nonflushable items make it down the drains of toilets, including some varieties of flushable wipes and feminine hygiene products. Unfortunately, both products accumulate in sewers with other problematic substances like fat, oil and grease (FOG), which act as knitting agents with these other items that do not deteriorate quickly enough in the sewer system. As a result, everything forms together and creates rag balls that clog pipelines and block pumps.
Rag balls are concerning when processing wastewater, as they cause excess wear in pump equipment and lead to significant system failures. Unfortunately, operators may not realize when rag balls have formed and, by the time they realize there is a problem, the rag balls are already causing severe blockages. Even worse, storm events create a perfect combination of high flows that prevent materials within the system from passing through quickly enough. When wells experience this catastrophic clogging, hazardous materials may expel into the surrounding environment.
It is a connected series of events that causes a problem like this. The good news is that technology allows users to intelligently connect related actions to predict, prevent and eradicate issues such as ragging.
Complete System Optimization
To optimize a pump system, users should understand how wastewater networks function holistically. It is not just one or two problem lift stations working in isolation; instead, it is a complex network that must work in harmony.
Today’s deragging technology allows users to determine—in real-time—if anything is interfering with or affecting the efficiency of a pump. For example, a network of lift stations will only have so much capacity to accept a limited amount of inflow at any given time. Connected technology allows the pump to self-regulate so that it can alleviate or remove this problem. Whether the pump equipment is aging, wearing out or suffering from a specific mechanical failure, the connected technology can predict potential issues and warn of catastrophic failure.
Predictive Monitoring & Automation
This technology goes even further than just monitoring individual assets within lift stations. For example, connective control devices and advanced monitoring systems allow wastewater systems to adjust in real-time to environmental changes. The corresponding data enables the system’s assets to prepare the collection network in anticipation of increased flows.
Such interconnected “asset thinking” potentially allows a network to manage much larger volumes without expanding storage capacity, which can prove cost-effective. Asset optimization is also benefitting from connectivity. For example, even if a pump is not in danger of catastrophic failure, its efficiency naturally declines over time. Real-time monitoring data allows operators to identify the proper moment for equipment maintenance or replacement, determining precisely when the improvement in operating efficiency will offset the cost of replacing the asset. Instead of a “run to fail” approach, intelligent technology can provide a far more optimized method for preventative maintenance and asset repair or replacement.
Preventing Problems Before They Occur
Going back to the ragging example, connected deragging technology allows for real-time monitoring of torque, power and a whole host of pump operating variables. Intelligent technology can instantly recognize the problem when rag balls form and start to hinder pump performance in wastewater systems.
In addition, it provides automated deragging by reversing the flow and agitating any rags, which clears any potential blockages while breaking down the rag ball into more manageable pieces that can safely travel through the pump
and be collected by screens at the treatment facility.
Deragging technology provides predictive and preventative capabilities. This technology is the perfect example of the modern need for more interconnected technology in the water treatment and wastewater management industries. When paired with a direct in-line pump system, real-time pump monitoring is a solution.
Pump design and control system technology continues to evolve with each passing year. Everything in our lives has become more connected, and these advancements change how pump operators run their systems.
Connectivity allows for enhanced equipment monitoring, flow rates, pressures, temperatures and other essential performance indicators. In addition, it can predict when pump components like bearings, seals and valves are experiencing too much wear and need to be replaced. Connected technology can provide predictive results to catch potential problems before they happen while automating specific catastrophe-avoidance processes.
Users can avoid clogs, leaks, floods and spillage while enjoying optimized cost-efficiency and dialed-in performance. Most importantly, monitoring technology continues to adapt and grow with the challenges facing pump system operators, showing that the future of wastewater system health is bright.