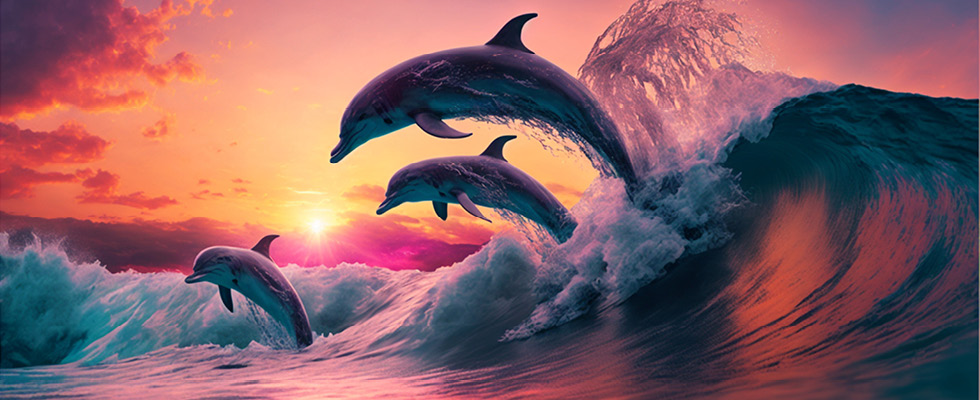
In the tales of the mid-18th century, sailors spun a captivating narrative about dolphins—the mariners’ supposed best friends. Stories echoed of men falling overboard and being saved by dolphins who guided them toward the shore. Dolphins became revered as benevolent protectors of the sea, always looking out for their human companions. Little did these sailors know that centuries later their tales would serve as an allegory for the perils of selective data analysis, echoing through discussions about the quality of scientific data.
In the realm of scientific inquiry, the story of benevolent dolphins illuminates the danger of cherry-picking data clusters, such as only considering cases of people who survived falling overboard. Imagine a scenario where a dolphin inadvertently pushed someone out to sea—a tale lost to the depths, its data excluded. Such selective analysis can lead to misguided conclusions, much like assuming dolphins are protectors when they may actually harbor a disdain for humans. This tendency to focus solely on positive data while excluding the negative is pervasive in various aspects of our lives. This is sometimes referred to as the survivorship bias.
This phenomenon of benevolent dolphins can also be observed in the field of flange sealing maintenance practices, where results are often based on only half the data. In our data-driven world, it is crucial to scrutinize maintenance training, ensuring it is grounded in facts rather than fallacies. Many plants lack specific training on effective bolting practices, an oversight that could significantly enhance overall plant performance and safety by minimizing leaks.
To navigate these waters successfully, it is essential to review a plant’s training program meticulously, ensuring it considers a comprehensive dataset when evaluating effectiveness. Treating training as a continuous improvement process is the key to staying afloat in the ever-evolving sea of industry standards.
Embarking on the journey to enhance a flange sealing training program requires navigating through good sources of technical information. The Fluid Sealing Association (FSA) is an international trade association founded in 1933. Its member companies are deeply involved in the production and marketing of fluid sealing devices, primarily targeted to the industrial market, making them a trusted technical resource for the industry (the knowledgebase site can be found at fsaknowledgebase.org).
Consider this case in which a hundred gasket failures were meticulously reviewed. A root cause analysis revealed that 68% of these failures were due to under-compression of the gasket, while 15% occurred because the wrong product was used in the wrong application. With these facts, it becomes evident that including bolt tightening skills in maintenance training is imperative. Yet, in the field, bolt loading training often does not receive the attention it deserves.
Take, for example, the absence of a standard anti-seize used uniformly by all employees and contractors. This oversight leads to inconsistent torque calculations, as many journeymen at a plant resort to outdated “torque tables” without adjusting for the coefficient of friction (K Factor) of the anti-seize used. This can result in inaccurate gasket loading and lead to gasket failure. This seemingly simple assumption that all anti-seizes and thread lubricants are the same underscores the critical importance of comprehensive training programs.
Another critical aspect is assessing the condition of bolting in a bolted connection. The absence of under-compression often stems from poor load transmission, emphasizing the pivotal role of bolt condition. Understanding torque is not tension is essential. Far too often, these terms are used interchangeably, but they have distinct meanings. Torque represents the force applied to the bolt, ideally resulting in a specific amount of stretch (tension) on the bolt. This relationship involves various factors, including bolt condition, coefficient of friction and torque wrench accuracy.
A real-life incident serves as a stark reminder of the consequences of using incorrect materials. In 2018, on Thanksgiving weekend, an ethylene oxide (EO) plant in Delaware accidentally released EO into the air. The Delaware Memorial Bridge had to be closed for five hours due to the potentially hazardous nature of EO. While no injuries were reported, the inconvenience caused to thousands highlighted the severity of the situation. Investigations determined a failed flange gasket, made of a material unsuitable for the operation, was the cause. This incident underscores how critical gasket selections are in hazardous service.
The Gasket Handbook, a 138-page document available for download from the FSA webpage, offers comprehensive technical information on gaskets in bolted flange connections. It serves as a valuable resource for plant engineers, maintenance operators and purchasing personnel, guiding them on specifying gaskets, troubleshooting leaks and understanding the functional distinctions between various gasket types.
Lifelong learning and training are indispensable for maintenance workers, engineers and planners. Ensuring training incorporates the latest methods and techniques not only reduces the risk of accidents, but also contributes to the longevity of plant operations. So, let’s navigate the seas of maintenance wisdom with the diligence of sailors, avoiding the pitfalls of cherry-picked data and embracing the full spectrum of knowledge for a safer and more efficient future.
We invite your suggestions for article topics as well as questions on sealing issues so we can better respond to the needs of the industry. Please direct your suggestions and questions to sealingsensequestions@fluidsealing.com.