Manufacturers of process pumps have, over many decades, concentrated on improving hydraulic performance thanks to expressed interest in efficiency gains from end users. The power end with its bearing housing and oil application strategies may, therefore, need attention.
A major Middle Eastern oil refinery was among those that saw merit in upgrading bearing housings and lubricant application methods. In early 2005, this refinery reported precise tracking for 1,400 process pumps lubricated by pure oil mist. In the previous year, there were no reported bearing failures in these 1,400 pumps.
Their experience corroborated what had been verified and published for the previous three decades: Oil mist is a safe, environmentally friendly and technically sound lubrication method. It is reliable, and users of an estimated 160,000 pumps in the United States and elsewhere have reduced maintenance costs and downtime.1
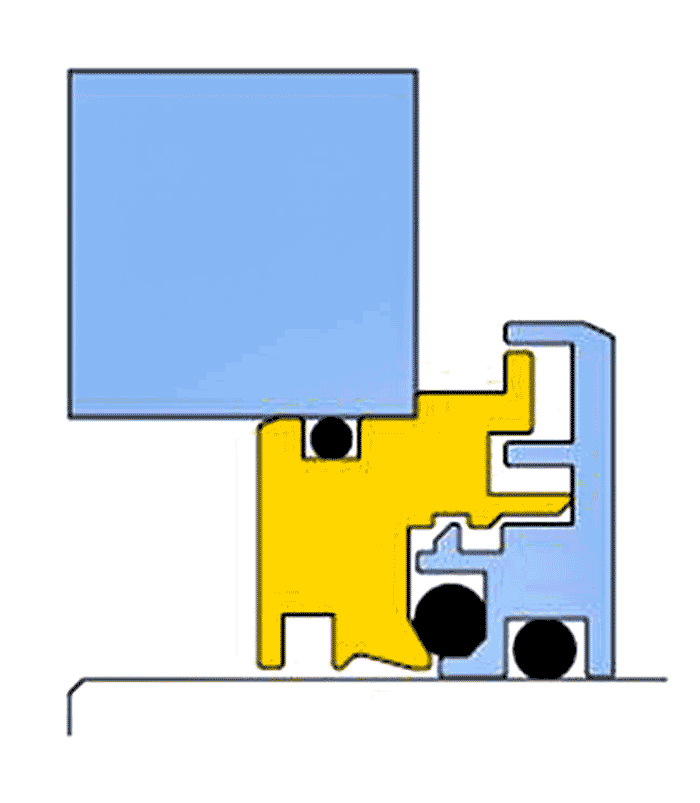
Overcoming Lubrication Deficiencies
Simple life extension measures such as installation of bearing housing protector seals (Image 1) combined with the removal of breather vents and thereafter plugging the housing’s vent port make sense. Also, while the reliability performance of oil mist may be under-reported, experience shows that oil mist and other upgrade options exist and are worth pursuing.2
As early as six or seven decades ago, a group of reliability engineers focused on lubrication technology and studied the merits of synthetic lubricants. Without these synthesized hydrocarbons, aerospace endeavors would have moved at a snail’s pace. About 50 years ago, reliability professionals began familiarizing themselves with different lubricant application methods found in process pumps. These professionals learned that all manufacturers of rolling element bearings give ranking numbers to different lubricant applications.
In 1980 and today, in 2019, many bearing manufacturers agree that a jet of oil sprayed into bearings is one of the most effective ways of lubricating rolling element bearings. Oil mist is usually highly ranked as well.
Pressured lubricant (“oil jet” or “oil spray”) provides some of the best possible lubrication of process pumps. The use of separately powered external oil pumps to pressurize and then spray lube oil into bearings may not be economical. Developing and then positioning a small oil pump inside a process pump’s bearing housing is feasible and should provide rapid payback. Located inside or mounted directly on the bearing housing, it could be driven from the main pump shaft. The small positive displacement spur gear pump (Image 2) or a functionally similar motor vehicle crankcase oil pump would take its flooded suction from the oil in the sump and would force the oil from the small pump’s discharge through spray nozzles into the bearings.3
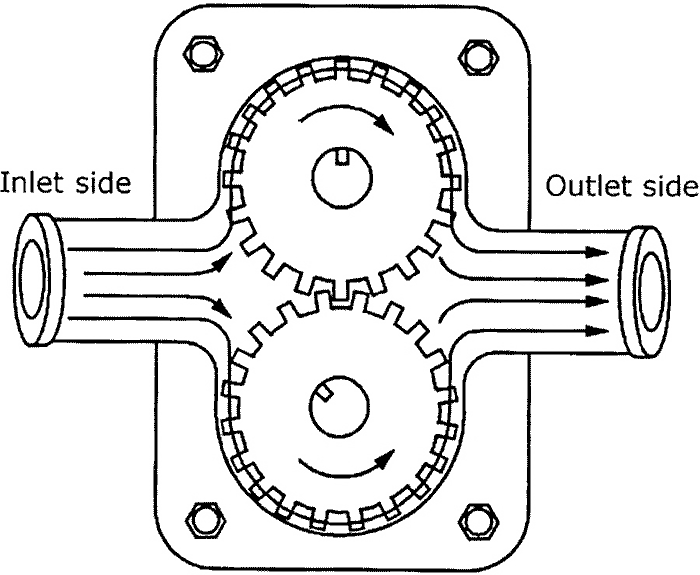
Oil Mist Technology Updates
Both oil jet and oil mist lubrication allow systems to dispense with what can be less reliable technology. Shafts no longer require absolute horizontality, and maintenance manpower shrinks.3
Two updates on oil mist technology were received between November 2018 and March 2019. The first came from an experienced reliability engineer who was surprised when a new project did not include oil mist lubrication for a process unit that was expected to be highly reliable and designed to minimize maintenance. The senior professional at the project-receiving plant wrote:
“The issue of optimized lubrication comes up whenever our world-scale oil refinery engages in plans for expanding throughput in process units or becomes the licensee/recipient of new process technologies with restrictions on budgets. Left to make our own decisions, the choice of properly designed and installed oil mist would not be an issue here. The latest unit commissioned at our refinery, circa 2001, has had all its pumps running on oil mist for 14 years and has not had a pump out for bearing maintenance. This is, so far, an infinite MTBR (mean time between repairs). The process is relatively clean gasoline products and our pumps were properly sized for the various services. Sister units using oil mist have had a similarly long MTBR. Operations teams and reliability groups believe in the results achieved with oil mist along with proper sizing and proper installation of process pumps. The statistical evidence is very supportive of the choices made since the early 1970s when oil mist was first tried in this facility.
… Our refinery does not need to be convinced of the value of oil mist since, at present, our pump MTBR is somewhere between 114 and 120 months, depending on how we calculate. But our numbers are close enough and quite compelling. Also, we have not had a lubrication-related bearing failure since 1999 that’s worth talking about. Note that this refinery has ACHE (air-cooled heat exchanger) fan bearings that have not been touched since the fans were installed in 2004. Finally, the same impeccable results were obtained with the pillow block bearings on the FD (forced draft) and ID (induced draft) fans at our refinery which, as you know, is the largest on this continent.”
The majority of reliability professionals remain determined to make a case for proven technology to project leaders and managers. They will be helped by this article and will find hundreds of pages of corroborating details in perhaps 100 articles, conference proceedings and books.
The issue of diverging views was also alluded to by a second reliability engineer. He had a question about the myth of a limiting product temperature when applying pure oil mist to rolling element bearings. What he had read differed from what experts had told him. He stated:
“Our specification allows installing pure mist in pumps with product temperatures ranging from 120 C to 250 C, as long as a fan is installed on the pump shaft. Above 250 C the specification disallows pure mist and, instead, requires purge mist (wet sump). ... At present, I am attempting to maximize the use of pure oil mist (“dry sump”) in the plant instead of the purge oil mist (wet sump) that had been widely used at our facility in the past.”
Today, some of the world’s most profitable oil refineries use pure oil mist on thousands of rolling element bearings. Pure mist is often considered the “gold standard” and has been in successful use at refineries owned by ExxonMobil, Chevron, Shell and others for more than 40 years. Forty years of experience in solid, safe, reliable hot service with temperatures as high as 400 C validate their value.
In the years when only mineral oil was used for process pump lubrication, forced air cooling was of some benefit. Since then, however, synthetic lubricants have become widely available and lube replacement intervals have been extended up to four-fold. In closed oil mist systems, the coalesced oil is collected after it has passed through the bearings; the coalesced oil flows toward a drain port near the low point of the bearing housing. Many refineries have, for decades, applied pure oil mist in conjunction with advanced-style bearing housing protector seals. With appropriately formulated synthetic lubricants, cooling is usually not required and cooling fans are typically not used.
Duplicating the approach taken in high-performance automobile engines where oil sumps have been enlarged, process pumps today are incorporating larger oil sumps than years ago. Also, water cooling is usually unnecessary on process pumps with rolling element bearings and fluid temperatures up to 400 C.
Dealing with Hot Bearings
If hot bearing housings (those exceeding 190 F/88 C) are encountered with oil mist, this is a sign of overloaded bearings, incorrectly installed bearings, incorrect bearing fits, incorrect lubricant viscosity and so on. When bearings exceed 190 F, it will be helpful to recall that without exception, all failures of rolling element bearings in process pumps are attributable to one of only four contributors, “FRETT.” The acronym FRETT stands for:
- force
- reactive environment
- time
- temperature.1
There are many pumps in service with pumping temperatures of 740 F (~400 C). They are lubricated with pure oil mist and some of these pumps have been in highly successful service for well over 40 years. Many of these are typically in operation for six or seven years before being dismantled for precautionary inspections.2
An API pump with rolling element bearings and a pumping temperature of 400 C on pure oil mist will operate with greater probability of long bearing life than the same pump (i.e., an API pump with rolling element bearings and a pumping temperature of 400 C) being operated with other alternatives. One match for oil mist would be an auxiliary pump-around unit or oil jet discussed earlier in conjunction with Figure 2.
Conclusion
End users’ choices should not contradict science and should harmonize with common sense. Start by understanding that pure oil mist works on hundreds of hot service pumps. Therefore, if it does not work at “Refinery X,” the root cause should be determined.
If oil mist works well on hundreds of seemingly identical pumps elsewhere, could it be that the real problem remains hidden?
References
1. Bloch, Heinz P.; “Pump Wisdom: Problem Solving for Operators and Specialists,” (2011) John Wiley &Sons, Hoboken, NJ, (ISBN 978-1-118-04123-9)
2. Bloch, Heinz P.; “Petrochemical Machinery Insights,” (2017) Elsevier Publishing Company, Oxford, UK and Cambridge, MA, (ISBN 978-0-12-809272-9)
3. Bloch/Geitner/Ehlert: “Optimized Equipment Lubrication, Oil Mist Technology and Storage Preservation,” Reliabilityweb, Ft. Myers, Florida; scheduled for release in fall 2019