How to seal rotating shafts for low temperature to cryogenic fluids.
FSA Member, John Crane
06/28/2018
Pumping fluids at extreme temperatures presents many challenges to the shaft sealing system. It must ensure the pumped fluid is safely contained while providing long-term reliability. Many pump operators are familiar with hot pumping services, but cold services offer some unique challenges to achieving reliable shaft sealing solutions.
Pumping Equipment for Low Temperature Hydrocarbons
The pumps used to pump these cold fluids are often specialized designs. Low temperature hydrocarbons are commonly pumped with American Petroleum Institute (API) 610 (VS6) vertical multi-stage double casing pumps that feature a warming chamber, known as a cofferdam, that thermally isolates the shaft seal from the cold pumped fluid. This enables a greater range of shaft sealing solutions that can be used on these pumps using traditional sealing technology. A cofferdam is a chamber between the pump discharge and the mechanical seal that is connected to the pump suction or the vessel the pump is drawing suction from. Ambient heat surrounding the pump together with energy from the shaft and bearings causes the liquid in this chamber to vaporize into a gas, which forms an insulating barrier between the seal and process fluid. Cofferdams can only be incorporated into vertical pump designs. However, although vertical arrangements are common, various horizontal pumps can also be employed. In these types of pumps, the shaft seal is in direct contact with the cold pumped fluid, thus selection of the seal materials for low temperature operation becomes more critical.Seal Selection for Low Temperature Hydrocarbons
Due to the volatility and flammability of low temperature hydrocarbons, dual mechanical seals are used almost exclusively.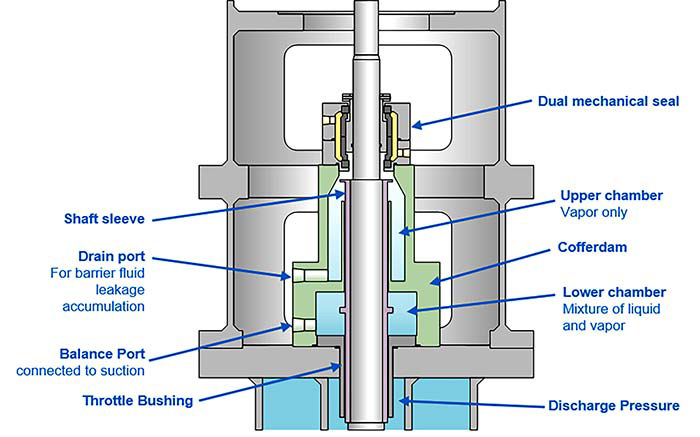

Material Considerations for Low Temperature Hydrocarbons
Low temperatures have significant implications to the choice of materials used in the seal construction. This is especially true for elastomers. Elastomers have a variety of minimum temperature limits, but none can survive dynamic operation at true cryogenic temperatures. Engineered polymer seals are an option at temperatures below the limits of elastomers. Many of these designs will not function with pressure reversals applied to the sealing ring that may be required in the mechanical seal design when support system failures occur. Elastomers can survive at significantly lower temperatures below their operational limits when the seals are not in operation (i.e. static), but they must be warmed up prior to operation. Commissioning of shaft seals containing elastomers must be completed carefully to ensure that the equipment is at the correct temperatures before startup. Blowdown, the rapid depressurization of a vessel/pipeline, is one situation that can create excessively low temperatures for the mechanical seal’s elastomers. Thermal expansion (or in the case of cold services, contraction) is also a consideration. The cavities that elastomers or engineered polymer seals are installed in will change with decreasing temperatures as will the dimensions of sealing elements installed in these cavities. Additionally, clearances between dissimilar materials, such as bushings, need reviewing. Mechanical seal manufacturers take these factors into consideration during the design of the mechanical seal. Another effect of cold temperatures is that metals become increasingly brittle as the temperature is reduced. As a general rule of thumb, martensitic and ferritic stainless steels should be avoided in favor of austenitic stainless steels.Pumping Equipment for Liquefied Atmospheric Gases
Similar to pumping equipment for low temperature hydrocarbons, a mixture of vertical multistage and horizontal single stage pumps are used. These machines generally do not follow API pump design standards. However, since the temperatures are much colder than those at which hydrocarbons are pumped, cofferdams are not employed on these machines. A mixture of vertical and horizontal pumps are commonly employed at air liquefaction plants, but mobile trailer-truck unloading pumps are almost exclusively overhung single stage pumps, either with direct drive or speed increasing gearboxes.Seal Selection for Liquefied Atmospheric Gases
Unlike hydrocarbons, emissions to atmosphere of atmospheric gases pose relatively minor hazards, thus shaft seal reliability takes precedence when selecting a shaft sealing system. There are two commonly employed shaft sealing technologies used in these pumps:- Single Mechanical Seals Single mechanical seals are the most common solution to pumps used in air liquefaction plant and mobile transportation unloading pumps. The major difference between the two is that the mobile unloading pumps tend to be smaller and often use noncartridge seals. Cartridge seals are commonly found in larger machinery at an air liquefaction plant. These seals fall into two subcategories: contacting wet seals and vaporizing liquid gas seals. Single mechanical seals use a metal bellows to provide elastomer-free axial flexibility. Seal face materials typically include filled TFE running against a tungsten carbide or hard-coated stainless-steel mating ring. Similar to contacting wet seals, vaporizing liquid gas seals feature seal face topography that allows the controlled vaporization of the pumped atmospheric gas to produce a highly reliable seal that exhibits controlled low-level leakage rates.
- Segmented Bushings This sealing configuration is most often found in vertical multistage pumps at air liquefaction plants. The design provides a controlled leakage by breaking down the sealed pressure over a series of tightly controlled bushing clearances. Leakage rates are higher than that of mechanical seals, however, these leakage rates are often considered acceptable in this industry.