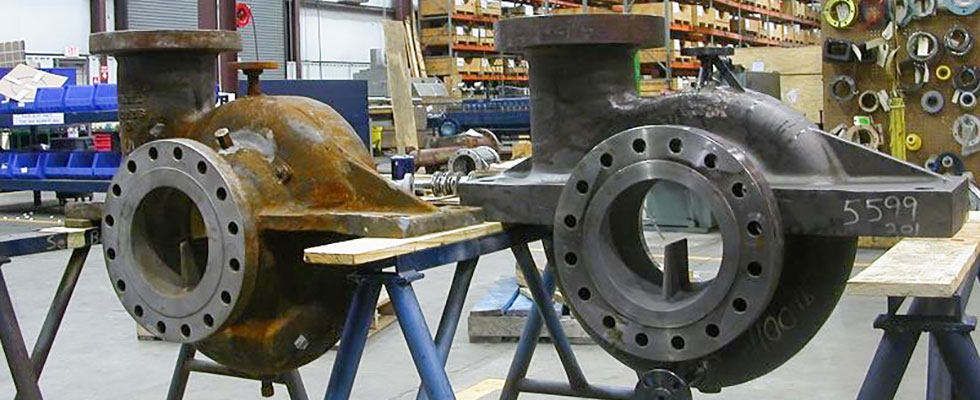
Single-stage overhung pumps are an important global resource for the transfer of fluids from one location to another. This specific style of pump is the most populous of all pump types as they provide a relatively large selection of flow and pressure range offerings and are generally simple to maintain (Image 1).
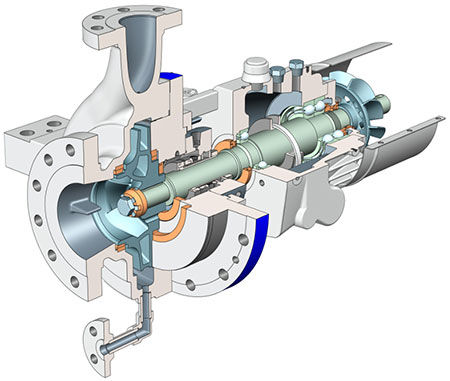
The processes served can range from heavy to light specific gravity liquids and cryogenic to temperatures over 800 F (427 C), in some cases. This versatility can put these pumps in the maintenance spotlight for increasing reliability and runtime to keep production units up and running.
Technology and experience have resulted in advancements in manufacturing, materials and design, improving the overall reliability of single-stage overhung (OH) pumps. The basic design criteria for horizontal OH-style pumps have remained relatively constant, consisting of a bearing housing with a radial and thrust bearing, and the impeller overhung on a shaft outside of the bearing housing. Industry standards, such as American Petroleum Institute (API) 610, purchasing recommendations and design considerations have been steadily revised to aid in increasing the overall reliability of these pumps.
The API 610 current bearing housing retrofit provides several upgrades to legacy-style pumps that may be subject to short meantime between repair (MTBR) schedules or fugitive emission reduction requirements. These retrofits will, in most cases, provide a single row, deep groove, radial bearing and paired back-to-back angular contact thrust bearings. Lubrication is improved with oil slinger rings and lubrication channels.
Larger oil sumps, fans and cast fins have been added to reduce or remove the need for external cooling water requirements. Finally, the seal chamber and shaft are designed to meet current API 610 deflection limits and Table 7 dimensions. This allows the use of an API 682 seal for upgraded seal technology, improved life and sealing performance.
Upgrades to the existing liquid end components of the pump are not often considered. Some legacy pumps were designed prior to many industry standards and do not contain several features that ease maintenance and reliability of the pressure boundary. The following upgrade opportunities are suggested for end users.
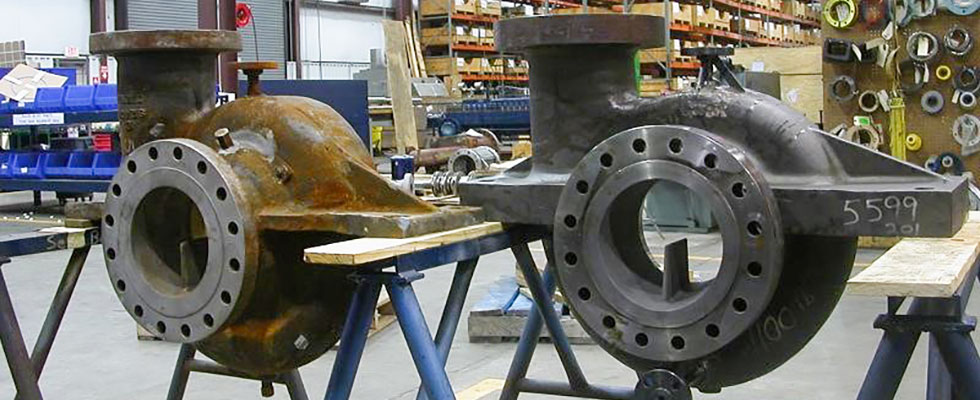
Improvements in Nozzle Loading
Equipment that was purchased and installed prior to the implementation of modern industry specifications may lack the ability to handle external nozzle forces and moments imposed by the connected piping. These forces, when applied in excess, can cause the pump case and/or base to deform, attributing to misalignment, excessive vibration and potentially wear part contact.
Often, these pumps were designed with thin mounting feet, minimal webbing bracing, and flanges that were flat faced and rated for 150 or 300 pounds per square inch (psi) (10 or 20 bar). These configurations can be upgraded with proper modifications to the existing patterns while maintaining the ability to fit in the existing piping and baseplate installations.
Legacy mounting feet and webbing may be 1 inch thick or even less, depending on the original design. Newer API 610 compliant pumps are supplied with much thicker feet and webbing to support API 610 nozzle loading requirements. Image 2 shows pattern alterations that have been made to a legacy design to improve the overall stiffness of the pump. The mounting foot thickness has more than doubled, providing extra strength to the casting.
The web bracing from the foot to the volute outside walls has also increased in thickness. In addition to these changes, the flanges for this case were changed from the original American National Standards Institute (ANSI) 300 raised face design to an ANSI 600 thickness with the same drilling and machining dimensions of the original 300 flanges.
All of these modifications have helped to improve the overall resistance of the case to deflect in the presence of pipe strain or increase the overall allowance of pipe strain as it relates to the pump alignment.
The final upgrade implemented for this case to improve overall stiffness of the pump and case connections was the installation of gusseting on the vent and drain flanges. Adding the gussets reduces the chance of small-bore pipe weld failures due to vibration fatigue.
Case Sealing Arrangement
ANSI/American Society of Mechanical Engineers (ASME) B73.1 pumps, and pre-API-style pumps up through API 610 4th Edition, did not require the use of a confined, controlled compression, spiral wound gasket between the case and case cover. In many cases, the gasket used was a nonmetallic sheet that would be sandwiched between the cover flange and case.
These gaskets could be somewhat unreliable as the compression across the sealing surface could vary depending on the torque applied to the casing bolting. Additionally, the materials could have limits for the temperature and chemical composition of the pumped fluid.
API 610 5th Edition introduced the requirement for a confined, controlled compression, spiral wound gasket to improve the sealing capabilities of the pump and expand the operational limits for temperature and product.
Many manufacturers of bearing housing retrofits incorporate the use of a spiral wound gasket in the design of a new case cover. However, the case usually must be prepared for this conversion.
Many legacy pumps may have a recess for a nonmetallic-style gasket, but that machine dimension was rarely a precisely controlled depth. Other styles may not have a gasket recess.
The opportunity to improve the overall sealing design can be incorporated when applying modifications to existing case patterns, as described in the previous section. If the existing casing dimensions at the casing cover interface will not allow for the incorporation of a spiral wound gasket groove, additional lagging can be applied to the outer diameter.
The casing closure bolt circle is then increased to create the room necessary for the incorporation of a modern API 610 Table 7 seal chamber.
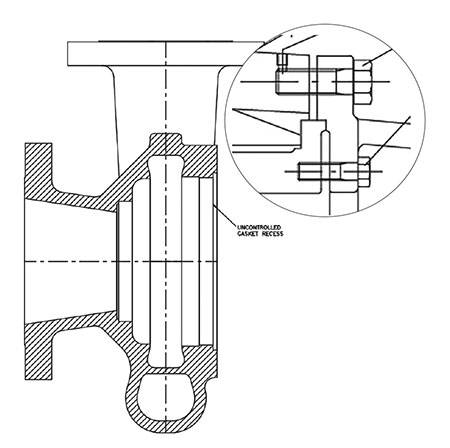
Hydraulic Rerates & Metallurgy Upgrades
In modern refining applications, it is highly likely that the original pump design duty point would change over the course of the expected pump life, due to alternative production demands.
A hydraulic rerate could be applied during the redesign phase of the newly supplied case to optimize the performance of the pump to meet current operational demands. Volute lip extensions or cutbacks from the original design may suffice.
If needed, an alternate volute core box could be created to provide more closely matched hydraulic profiles. A revised high- or low-capacity impeller may be installed to further optimize the best efficiency point (BEP) to the desired operating flow rate and differential pressure.
Consider an instance of a rerate performed on an overhung pump. The original duty point requested for this pump had been reduced and a new batch process required even further reduction of the
flow rate.
A combination of the volute modifications and an impeller replacement resulted in a satisfactory operational curve meeting the customer’s requirements.
Corrosion/Erosion Upgrades
To help combat the effects of corrosion or erosion in pump cases, it may be prudent to upgrade the case metallurgy to better suit the process fluid. These changes may include upgrades from carbon steel to a martensitic, austenitic or duplex stainless steel. Alternatively, many of these legacy pumps may be cast iron.
Replacing cast iron with carbon steel, or other weldable alloy, may add decades to equipment life span. For highly erosive conditions, additional steps involving the application of coatings in the flow passageways may also be considered. These may include technologies such as high-velocity oxygen fuel (HVOF) sprays, weld overlays and diffusion coatings.
Overhung bearing housing retrofits have long been a proven upgrade to aid in extending the MTBR of API- and pre-API-style pumps. However, it is important to realize that further gains can be made with the proper application of new pump technology to legacy equipment without the need for additional field modification of the existing installation. These modifications, while they may seem to have a long lead time and can be costly upfront, are likely to be dwarfed by the cost of field modifications to base plates and piping installations.
In addition to those expenditures, efficiency improvements can often be incorporated to further extend the life of the unit and reduce operating costs while meeting revised production demands of the facility.