Lawmakers in Washington are talking about it. Operations teams are thinking about it, and CFOs are losing sleep because of it. A plant’s energy costs are on multiple stakeholders’ minds.
Plant managers especially want to increase uptime and throughput without sacrificing goals for reduced production costs. These two competing issues can be dealt with simultaneously, but not through piecemeal efforts. A systems approach to pump system efficiency is required to accomplish both.
Imagine if all the specialized production equipment in a plant was stripped away. A labyrinth of pumps, pipes, tanks and valves would be left—key components of subsystems that are critical to a successful operation. These subsystems represent a significant portion of a plant’s current operating costs and, directly or indirectly, have a serious impact on plant performance.
Right now, approximately 40 percent of manufacturing revenues at facilities are devoted to the maintenance of pumps and valves. The good news is that up to 60 percent of scheduled maintenance checks on valves and motor systems in these systems could be avoided.1
The key to solving many facilities’ most pressing issues is a systems approach to efficiency—not just focusing on the primary systems but also the subsystems.
Finding Optimization Opportunities
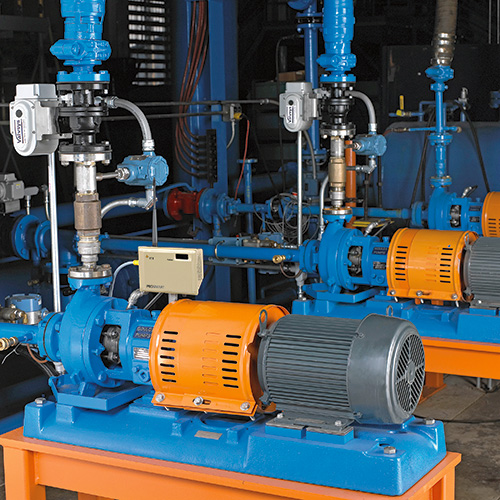
The standard in plant systems management tends to be more about “fire fighting,” but engineers need to take a more systematic approach to improving long-term performance. This does not mean ignoring pressing issues. It means finding the right solutions from a technology perspective, rather than deploying the fastest and easiest fixes. It also means tracking the sources of chronic issues, so they can be treated with permanent solutions. Instead of treating symptoms, operators must attempt to cure the disease in the systems.
In pump systems, disease runs rampant. Pumps are often oversized and inefficient. The average pump efficiency is less than 40 percent. More than 10 percent of pumps are running at 10 percent efficiency or less, according to a recent study by the Finnish Tech Research Center. Centrifugal pumps represent the single greatest opportunity for electrical energy savings compared to other processes and equipment.
The biggest process disease that plagues plants today is not necessarily intuitive. It is often hiding in plain sight. Oversized pumps that result in excessive throttling are the most common culprits, with seal failure as the number one maintenance cost item. Pumps with relatively high levels of excess energy carry higher electrical costs, but increasing the pump size is considered a way to play it safe. It is exactly the opposite. The excess energy is blowing the pumps apart. Oversized pumps are less reliable and more costly.
When thinking about the amount of excess head generated by oversized pumps, the excess is often considered as reserve pressure that is available, if needed, to do useful work. Many end users think that this is why adjustable control valves are used, but valves kept in restrictive positions wear out faster. They also wear out pumps faster. Valves that are frequently less than 40 percent open can force pumps to operate against massive resistance, exposing the pumps to inordinate bearing damage, seal wear and leakage. Under these conditions, pump shafts often crack or break.
Optimizing Pump Performance
A systems approach to efficiency includes more than just understanding energy loss in throttled pumps and the increased costs associated with resulting breakdowns. Additional technologies are available that help subsystems work in better unison, which should also be considered.
In addition to pump and valve breakdowns, oversized pumps and throttling can result in degraded process control. Sub-optimal process control increases variability, and as a result, control loops are often switched into manual mode to stabilize the process. This common fix results in additional costs that are the direct result of compounding system inefficiency.
In many cases, a better solution may be installing variable frequency drives (VFDs) to adjust speed rather than control valve position.
A recent study by the U.S. Department of Energy suggests that motor systems equipped with VFDs account for only 4 percent of motor energy usage, marking a significant opportunity for efficiency improvement. VFDs are widely applicable and can be applied to 18 to 25 percent of total energy used for retrofits or up to 60 percent for new or refurbished plants.
In antiquated systems, manual throttling is the only way to adjust the flow in pump systems. Today, VFDs integrate pumps into process control systems. They make archaic, mechanically controlled pump systems high-tech, often including embedded firmware programs with pump protection technology. By incorporating VFDs into the continuous loop in lieu of a control valve, low static head pump systems can consistently operate near peak efficiency. Adopting a systems approach means building systems that have components that work in sync with one another.
Case Study: A Bleach Plant
Regular pump breakdowns and undue wear resulting from throttling can cost companies millions each year. In one case study dating back to 2001, a paper mill bleach plant suffered from major problems and financial losses as the result of an oversized pump before a plant performance team stepped in to help.
The bleach plant was facing downtime issues that could not be ignored. Internally, an energy team determined that nearly two-thirds of the facility’s valves were less than 50 percent open, and many were less than 30 percent open. One key pump system had a capacity of 6,500 gallons per minute (gpm), but the average load was only 2,750 gpm. The peak flow demand was only 5,200 gpm. The pump was heavily throttled, which resulted in chronic stress on pump components and valves, pipe cracks, gasket leaks and frequent downtime. It experienced failures while running and during startup and shutdowns, which occurred more than 10 times per year.
More damage occurs at startup and shutdown than at any other time, primarily because of the large pressure changes and water hammer across the pump system components. However, the initial shock to the system upon startup involved more than pressure. Thermal shock from 220-degree fluid entering the pipes on startup also occurred.
The mill’s reliability engineers had conducted a thorough examination of the system, determining that the installation of automated gate valves and new operating procedures—to open slowly as pipes warmed to avoid thermal shock and cracking—would provide incremental improvements with a reduction in breakdowns. However, the complete elimination of failures was only accomplished when the plant performance services consultant recommended a low-voltage motor and VFD, operated in pressure control mode, for the three vessels that the pump was feeding. The result was markedly increased efficiency plus a pump system modification that paid for itself quickly.
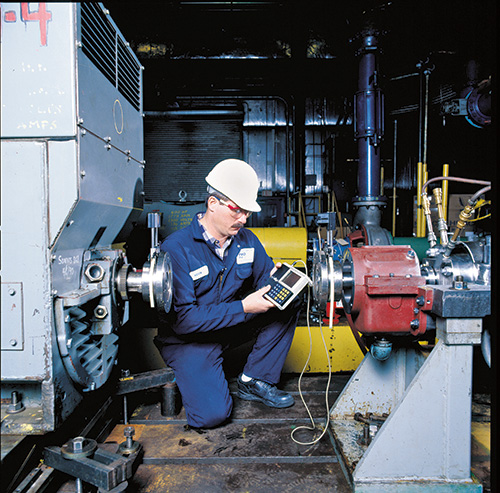
Stabilizing the control loops and reducing pressure inside the system took a pump that failed frequently and turned it into a properly functioning component of the system. The bleach plant witnessed $18,000 USD in energy savings in 2002. Energy savings in the same process had climbed to $32,000 per year in 2010 as energy costs increased. Beyond the efficiency improvement, plant representatives reported that the systems-based solution saved them more than $1 million annually in downtime and repair costs.
Adopting a Systems Approach
Plants are not investing in efficiency quickly enough for several reasons. One is simply a lack of experience with the methods and techniques used to raise efficiency. When components break, operators often buy what they know works to replace them.
Plant operations are risk adverse, and modifying a system to improve efficiency often represents an element of risk. Not making the changes also carries a risk that is usually much greater. When in the process of deciding to modify systems to improve efficiency, it may feel like Catch-22. Nobody wants to interrupt day-to-day operations of the plant to overhaul functioning equipment or systems—especially if they are not necessarily part of the specialized production equipment that is paramount to a plant’s business success and a product’s differentiation in the market.
However, critical subsystem issues in many plants have been ignored for too long. Engineers and suppliers oversize pumps frequently and for many reasons. Sometimes, they prepare for increased demand, imagining future capacity increases that never come. Sometimes, pipe friction losses are overestimated, leaving no doubt that enough head is available when needed. The approach is common but not ordinary.
The main reason for lower than expected investment in high-return energy efficiency projects is a lack of funds set aside specifically for energy efficiency studies and projects. The need to earmark funds in the capital budget must be addressed, because plants will face the imperative to make energy investments in the future. Sustainability is an essential strategy for industrial plant survival.
Though it is often appealing in the short-term to fight fires, this approach can overlook potential design and operating cost-savings that far exceed the implementation cost. A dedicated systems approach to optimizing efficiency can save the industry billions and save plants millions in energy and maintenance costs—while improving process control and plant sustainability—throughout the manufacturing landscape. It is something everyone should be thinking more about—from the plant floor to Washington.
References
1. ARC Advisory Group, “Strategies to Drive Manufacturing Efficiency on the Production Floor.”