10/28/2009
The Challenge
A paint and coatings plant that produces both cationic paste with pigments and cationic binders without pigments for truck shipment to automotive OEMs was experiencing difficulties when transferring the compounds from mobile tanks to trucks.
In particular, its pumps were incapable of totally draining the pipes, hoses and mobile tanks used in the process, leading to wasted time and materials, as well as an increase in the probability of leakage occurring. Because the trucks are loaded with cationic binder from mobile tanks, meaning frequent human involvement, the plant operators were looking to upgrade to a pump that would make the overall operation cleaner and more efficient.
Because of the unique types of binders that are handled, as well as the operators' requirements for clean, time-sensitive performance, a versatile pump needed to be incorporated-one that was sealless and provided low shear, clean-in-place capabilities and high volumetric efficiencies.
The Solution
The new pump selected for this type of application featured eccentric disc technology. The eccentric disc pump installed at the plant was sealless. Four years after installation, the pump is still working perfectly. At the end of the loading process, the pump totally drains the inlet hose, mobile tank and outlet pipe, and since the pump does not have a mechanical seal, there is no risk of product leakage.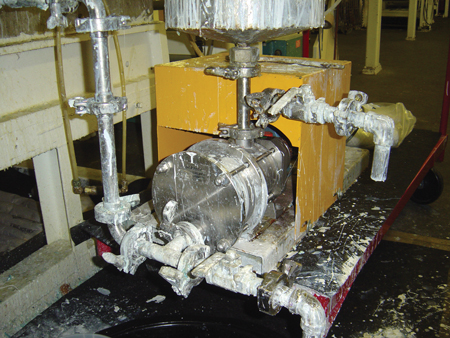
- Sealless design without mechanical seals, magnets, rubber or PTFE diaphragms
- Low shear handling of products with low slip, lower internal velocities and ultra-low agitation
- Clean-in-place capability that allows the pump to be completely drained, flushed and cleaned without disassembly
- High volumetric efficiency capable of maintaining a constant flow rate at a given viscosity throughout its pressure range
- Good compression performance and the ability to run dry (up to 10 seconds) enable self-priming capabilities and complete line stripping of suction and discharge lines
- Self-adjusting operation that maintains delivery/pressure performance over time through the use of a self-adjusting disc/cylinder
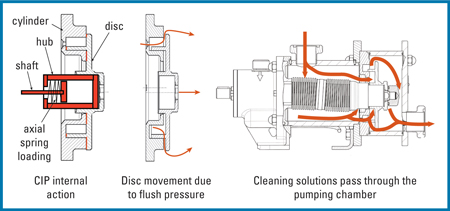
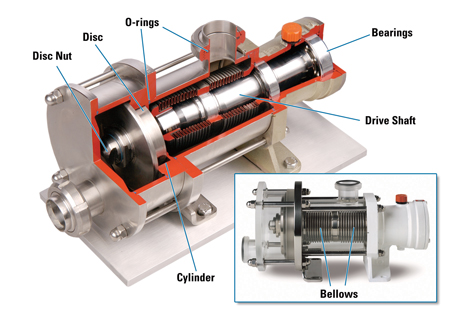
Eccentric Disc Technology versus Others
Because of all of these characteristics, eccentric disc pumps can supply benefits that some pumps traditionally used in the paint and coatings market sector cannot:-
Air-Operated Diaphragm (AOD) Pumps-AODs have traditionally been the pump of choice in the P&C market because of their low initial purchase cost. However, they can be inefficient and require high maintenance, increasing their total cost of ownership.
- Gear Pumps-The second most popular pump choice behind AODs due to their capability of handling higher viscosity ranges. Gear pumps can have excessive seal leakage; inability to self prime; a flow rate that is jeopardized when wear begins; high internal velocities that affect fluid dynamics, resulting in shear; and clearances that result in slip as pressures increase and viscosities decrease.
- Centrifugal Pumps-Centrifugal pumps can have a high rate of slippage. Some centrifugal pumps have lower efficiencies than eccentric disc pumps.
- Lobe Pumps-Lobe-type pumps perform like gear pumps, meaning they can have many of the same drawbacks that gear pumps have. The need to seal two shafts doubles the expense of seals and the potential for leakage.