A great innovation in compression packing was the development of a new material class by Ritchie Snyder of W.L. Gore & Associates in 1981. He envisioned a single material that would allow for broad standardization across a wide range of applications. It would deliver the chemical compatibility of polytetrafluoroethylene (PTFE) and graphite, with the mechanical strength of the then newly expanded PTFE material (ePTFE). Over the next 35 years, many pulp and paper, chemical, mining and power companies have standardized their plants with this new material class of ePTFE/graphite packing fiber. Prior to this breakthrough, end users working in chemical applications had one option for standardization: a natural mineral fiber known as asbestos, which was effective because of its chemical inertness and high temperature rating. By the late 1970s and early 1980s, however, it was actively being eliminated from the market because of health concerns. As an alternative, pure PTFE was substituted, but it was a poor replacement because of its inherent creep, mechanical weakness and high coefficient of thermal expansion. It was also a heat insulator with a low thermal conductivity of only 0.25 watts per meter per degree Kelvin (W/m K) and shaft speed and temperature limits of 2,000 feet per minute (ft/min) and 260 C (500 F), respectively. This material required strict adherence to the installation procedure and operator knowledge. Any overtightening could lead to a negative feedback loop of increased heat, leading to more expansion, friction and heat. These effects would damage the shaft or sleeve as a result of crystallization of the PTFE, leading to premature failure. Graphite was a great material for conducting heat. While dimensionally stable and capable of operating at higher temperatures, graphite lacks mechanical strength and makes maintaining a lower leakage rate difficult. Because of inherent limitations, other material class options fell short of meeting the need for a general-service packing for standardization, including:
- Natural fibers: The chief advantage of flax, ramie, jute and cotton is low price, but performance is negatively impacted by limitations, including poor chemical resistance (5-9 pH), low heat resistance (98 C/208 F) and speed (1,000 ft/min).
- Aramid fibers: They are divided into two categories: para-aramid and meta-aramid. They are differentiated by the type of monomer that determines molecular structure of the polymer chain. Para-aramids are bright yellow, while meta-aramids are white. Para-aramids have high tensile strength and cut resistance, and can be up to five times the strength of steel wire of the same weight. However, chemical resistance is limited to a 4-11 pH range, temperatures up to 120 C (248 F) and speeds up to 1,500 ft/min. Meta-aramids are chemically resistant with a 1-13 pH range and temperature resistance up to 270 C (518 F), above which glass transition limits its use.
- PTFE: Although PTFE is a chemically inert material with a 0-14 pH capability, very low friction and self-lubricating properties, it is limited by mechanical strength, coefficient of thermal expansion and creep. It is good for shaft speeds up to 2,000 ft/min and a maximum temperature of 260 C (500 F).
- ePTFE: This material has the same chemical and thermal expansion properties as PTFE but with higher mechanical strength and lower creep. It can operate at shaft speeds up to 3,600 ft/min. In some cases, the material can exceed the max temperature of PTFE by up to 20 percent.
- Carbon/graphite: This material has a range of properties depending on the graphite/carbon makeup and the mixture selected. The most common offerings can handle shaft speeds up to 4,000 ft/min and temperatures up to 260 C (500 F) in centrifugal pumps. They can also come in higher-purity forms, operating in valves up to 675 C (1,247 F).
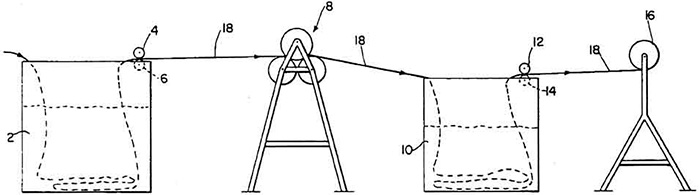
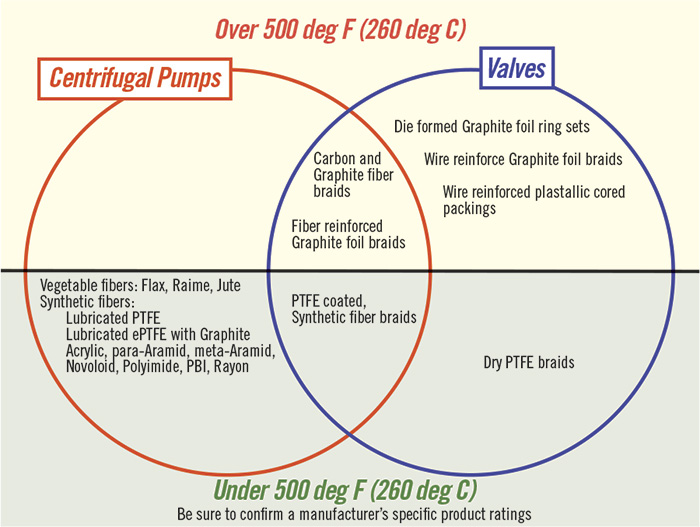