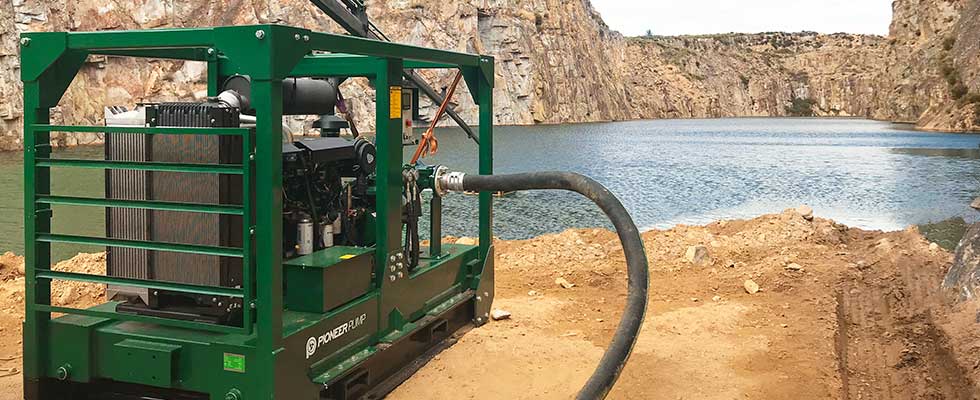
If a mine uses pumping equipment, chances are reliability and efficiency are equally important to overall productivity. From dewatering to slurry and tailing pumping to processing produced water, the pump packages a mine operates help to get the job done, and there is no room for downtime or expensive overhead. So, how do mine owners and operators make sure the pump packages they choose are helping to get the job done efficiently? This is where total cost of ownership (TCO) comes into play. TCO goes beyond the initial purchase price of a piece of equipment and looks at the total lifetime cost of owning, maintaining and operating it. While more industries are moving to electric power, when it comes to making the shift in mining applications, TCO plays a major role in making the best choice for the application needs.
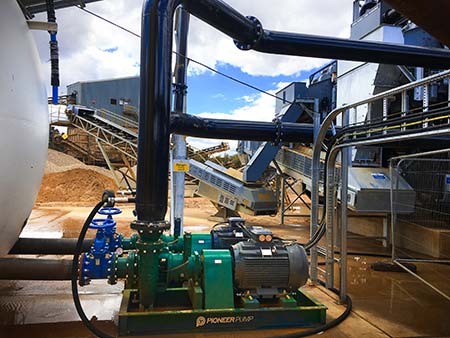
Fixed Costs in the TCO Equation
In addition to the initial acquisition cost to purchase and transport the pump package, the TCO calculations for electric- and diesel-driven pump packages in mining applications will likely include a few fixed costs, such as:
Service costs per year
Service costs per hour times service hours per year.
Energy costs per year
For electric-driven pump packages, take the local cost per kilowatt-hour times hours of operation per day times the number of days the pump operates per year times the kW absorbed at duty point by the pump.
For diesel-driven pump packages, calculate the cost per gallon of diesel fuel times the number of gallons burned per day times the number of days the pump operates per year.
Downtime costs per year
Cost per downtime hour times downtime hours per year. Multiply each of the annual costs above by pump life span and add in the initial acquisition cost to calculate the TCO of a pump package.
It is important to consider, however, that not all costs might be equally weighted depending on the application requirements and other factors. Maintenance and repair can account for additional revenue loss and be a bigger factor for certain operations. What kind of cost ripple effect does downtime mean to a site? It is important to consider some of the benefits an electric-driven pump package may bring to a mining site and how these might factor
into TCO.
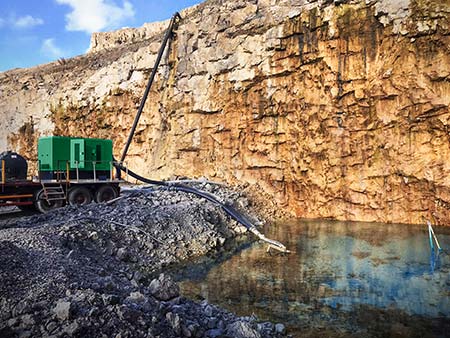
Evaluating the Benefits of Electric-Driven Packages in Terms of TCO
First consider where the pump package will be installed and how it will be used. The most common mining applications include:
- dewatering
- process water
- tailings
- slurries
- wastewater and reuse
- quarrying wash plants
- backup fire protection
Then consider why an electric-driven package makes sense in each application. Questions to consider include:
How important is versatility?
Electric pump packages come in a variety of sizes and configurations—and that versatility can be critical for the ever-changing needs of mining sites. For example, portable electric-driven pump packages are typically paired with variable frequency drives (VFDs) so that users can address multiple applications with one pump by simply adjusting the speed. For mining applications with varying duty points, electric-driven packages can meet the specific efficiency and performance requirements of each application or be used for multiple applications, as long as electric power is available. The pump can run one day to dewater a small pit and then be moved to a larger one the next day without compromising the long-term performance of the motor.
An electric-powered pump also delivers end-to-end performance. Electric-driven pump packages can cover multiple duty points. In an electric-driven package, when the VFD connects to a power source, it converts the input frequency to the desired output frequency, changing the rotational speed of the motor. This allows the pump to reach the entire pump end’s performance curve range.
Versatility can also factor into TCO. Consider the changing landscape of a mine over the years—it can get larger or deeper and require increased dewatering needs. One versatile pump package can be used across a site over the years or be expanded as needed. This saves on ownership costs as well as operating costs.
Is a clean running engine critical to a site’s needs now or in the future?
Mine sites are often tight quarters with limited real estate for large pumps and limited space to exhaust fumes. Add in that the world is changing in terms of environmental regulations, and pump operators need more options to run cleanly and efficiently. This is where electric-driven pump packages become more practical and responsible for the long-term. With regulations becoming more
stringent, electric-driven packages can be an environmentally friendly option for mining applications.
Spontaneous combustion from nonexhaust emissions and fuel spillages in diesel engines can be a safety and environmental concern in mine sites. Electric motors eliminate emissions and mitigate hazardous waste cleanup from leaks and other Environmental Protection Agency (EPA) regulations. These environmental benefits also lead to financial ones, since cleaner running equipment minimizes the cost of dealing with emission issues.
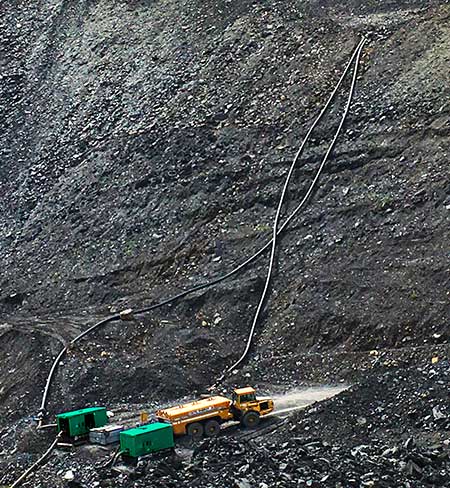
How important is operational simplicity?
Electric-driven pump packages are designed for more “hands-off” operation, delivering reduced costs when it comes to overall day-to-day wear and tear and less chance for human error. There are no oil or fuel levels to check and no filters or oil to change. No fuel also means no fuel trucks on-site that could potentially cause damage to the landscape.
Electric motors feature fewer moving parts, so there is less overall maintenance. Electric motors can offer remote control capability for complete hands-off operation. These remote operating features can also help protect a pumping system without constant in-person monitoring. Float switches can be set to automatically turn the pump on and off depending on the water level, ensuring coverage when it is needed and preventing the pump from running dry.
Using TCO to Evaluate & Select the Right Packages for Mining Applications
Once fixed costs and operating variables are determined, TCO can be accurately calculated. Here are two hypothetical examples of pump package applications that might exist in a mining operation:
- a temporary pumping system for dewatering mine pits
- a fixed pumping system at a mine’s processing plant
Temporary dewatering of mine pits
In this application case, a pump is used on a short-term basis at different locations across a mine site that does not have access to electrical power. For example, the pump is used to dewater a mine pit for four weeks, then moved to a different pit the next month and so on for a year or more at a time. Because this use case involves many short-term applications, powering a high-head pump with either an electric motor or a diesel engine yields total energy costs that are only within a few thousand dollars of each other.
However, in this example, the diesel set excels because of the lack of electrical availability at the site. The investment required to install electrical power would simply not be worth the effort; it would require site surveying, added time and additional crews. Plus, the new electrical would likely result in high voltage cables running across the site adding to safety issues. Bottom line: Diesel offers the better TCO for this type of installation.
Fixed processing plant installation
This application looks at TCO for a pumping system at a mine site’s processing plant. Typically, the processing plant is already electric-driven, which means power is likely available for the pump package. The duty point for these types of applications is typically fixed; it is usually doing a set job and will not be relocated throughout its usage life, which can cover years of use. Selecting the same pump end to meet the application demands but powering it with an electric motor versus a diesel engine yields total energy costs that are different from each other—more than double the amount of total energy costs.
When an electric pump is being used in a fixed application, the initial investment cost is lower than a diesel pump package if a VFD is not needed. In this case, upfront capital investment in an electric package will save on operational expenses over the life of ownership.