01/29/2013
First of Two Parts
Branch-line pumping applications abound throughout the pumping industry. These systems consist of a pump (or pumps) discharging into a single line that feeds a network of individual piping segments. Branch-line systems can be closed-loop or open-ended.
Closed-Loop & Open-Ended Systems
Figure 1 illustrates these two configurations. Closed-loop systems are often seen in heat exchange applications in commercial and industrial processes. The most common example of an open-ended system is the water piping in a typical home. The hot and cold water pipes branch out to the kitchen, laundry room and bathrooms. Many high-rise buildings use booster pumps that feed a vertical riser with open branches to each floor. Industrial applications use open-ended systems to distribute fluids to various locations within a plant.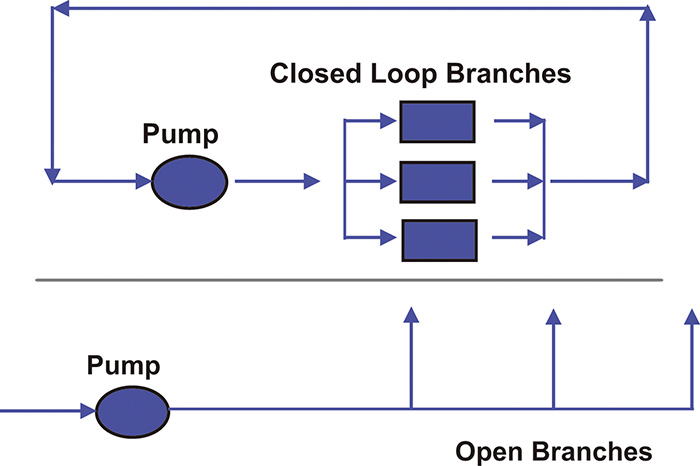
Example
Figure 2 is an example from my “Branch Line Pumping Alternatives” spreadsheet. It allows a user or designer to compare a standard branch-line pumping system with several alternative designs and calculate the potential cost savings of those alternative designs. It is an evaluation tool—not a design tool.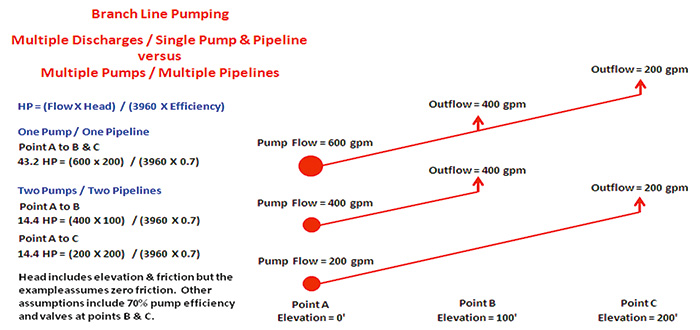
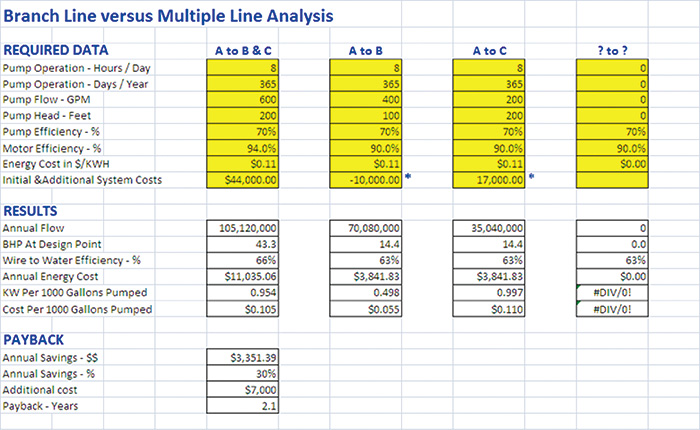