A Southwest mining company, as part of its expansion plans, invited bids for a complete tailings reclaim water system. The proposal called for multiple system features, including pumps, motors, valves, piping, floating pump barges and skid-mounted booster stations. The conceptual design included two parallel pumping systems, each with primary barge-mounted pumps and two booster stations. Each parallel system was intended to be independent of the other, allowing relocation while others remained in service. The level was expected to increase rapidly in the initial phase and gradually over time as the pond became larger. The systems were designed to pump reclaim process water from the tailings dam to a holding pond at the mill concentrator. Mill operators would reuse the water as needed. Each parallel system, or train, would pump 10,500 gallons per minute. All three pumps would work in parallel against a total dynamic head (TDH) of 750 feet. The TDH would decrease over time as the pond level rose.
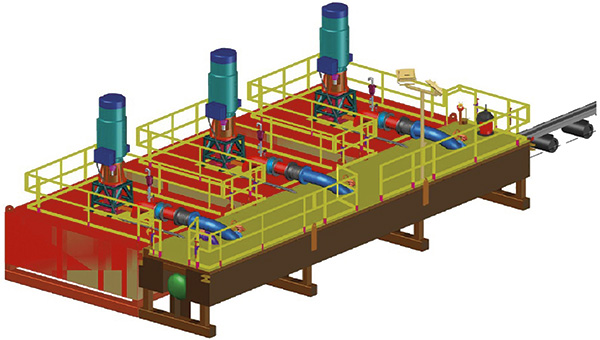
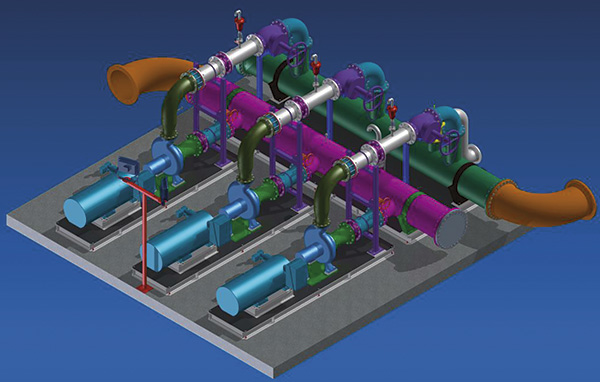
- Six cantilever pumps with 350-horsepower (HP) motors
- Twelve end-suction pumps with 300-HP motors
- Six steel hull pump barges
- Two steel hull header barges
- All piping, valves, instruments, fabrication, engineering, pre-assembly and testing
- A 175-HP tri-hull pontoon boat with a 2-ton service crane
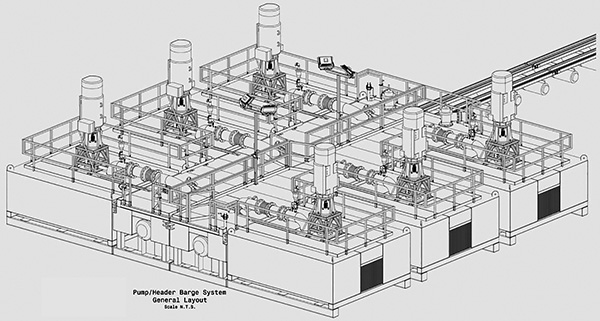