Pumping Prescriptions
Pumping Machinery LLC
05/24/2017
Last of Four Parts
Editor’s Note: Barry T. Brown of Spurlock Station, Unit 2, East Kentucky Power Cooperative contributed to this column.
In the first three articles of my recent series “Case Study: Troubleshooting Seal Problems in Cooling Water Pumps,” published in Pumps & Systems (December 2016, January and February 2017), we discussed the background of the seals’ reliability issue and the application of a monitoring troubleshooting system (PREMS-2A) used to track the issue to a root cause. Many readers offered suggestions, some of which were presented in the March 2017 Pumping Prescriptions column. This final installment of the series will present the ultimate pinpointing of the root cause and solutions for the problem.
Having ruled out operational issues, the focus of our work steadily narrowed toward the design and installation itself. As was noted by Lawrence Leising in our March 2017 article, there is a key difference between the seal chamber environment within the horizontally mounted versus vertically mounted pumps.
While a more typical horizontal configuration of the single stage double suction split casing pumps may not be as susceptible to a dry running seal faces environment, a vertical orientation of such pumps can become a big issue for the seals in this regard. A detailed evaluation by the seal manufacturer of these repeatedly failing seals further confirmed the conclusions reached by the authors: the lack of vent ports was the main problem.
The major issue was air entrapment at the top of the seal chamber with no air vent connection provided. This was apparent from the condition of the seal faces.
Both primary (rotary) seal faces exhibit significant phonographic finish with chipping at the edges. This type of damage is typically indicative of lack of lubrication (dry running).
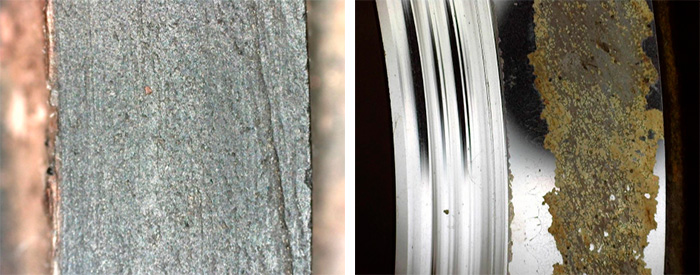
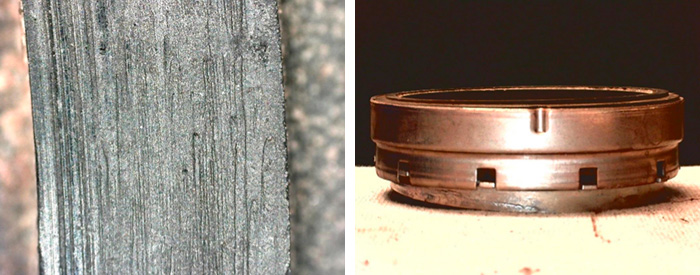
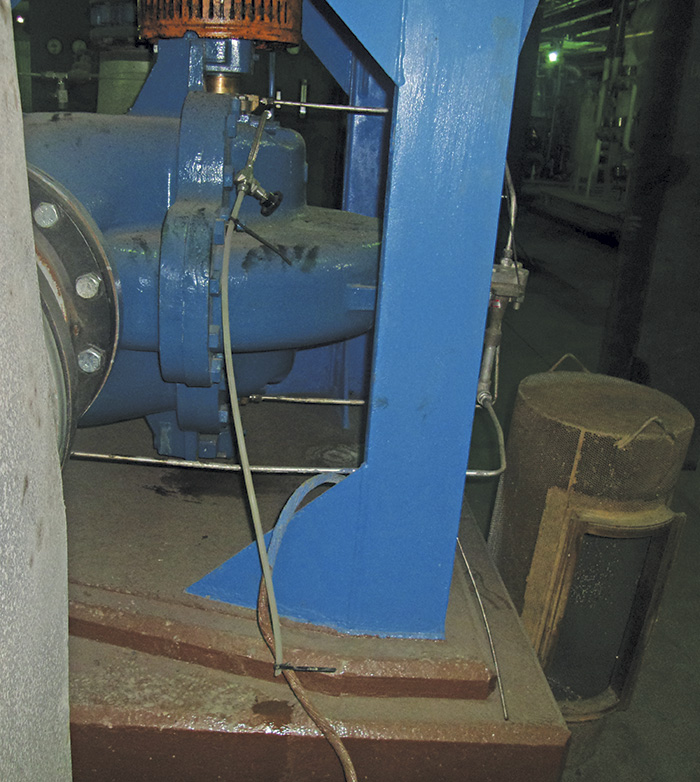
To read more Pumping Prescriptions columns, click here.