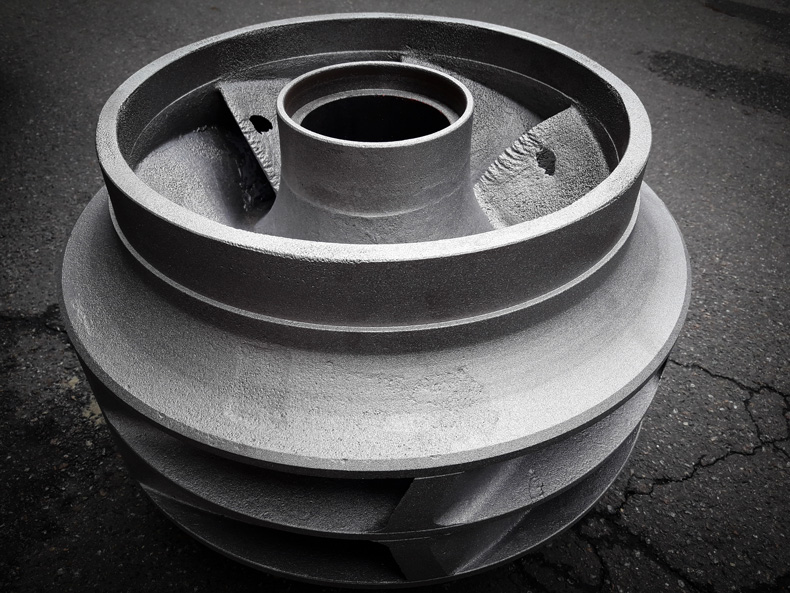
What causes cavitation?
Cavitation results from the formation and subsequent collapse of vapor bubbles within the pumped liquid. There are many possible causes, such as low net positive suction head (NPSH) margin, high velocity recirculating currents in the impeller, hot liquid, etc., but all causes result in the pressure on the pumped liquid dropping below the vapor pressure of that liquid, allowing the formation of vapor bubbles.
In which environments/applications is cavitation the biggest worry?
Cavitation is most common in systems where there is significant, dynamic loss on the suction side of the pump (dry pit pumps), pumps that are running to the extreme right side or left side of their performance curve or in installations at high elevation or with hot liquid. Any situation that results in the pressure of the liquid in the suction area dropping below the liquid’s vapor pressure will cause cavitation.
What does cavitation do to equipment in use?
Cavitation causes shock loading to the pump wet end components as a result of the energy released when the vapor bubbles collapse. This can result in bearing, seal, shaft or other component failure.
More immediately, the high energy collapse of the bubbles eats away or erodes the surfaces of the impeller, wear plate and, in severe cases, the volute, resulting in damage to and failure of these components.
Does cavitation always damage a pump?
Pumps can tolerate a small amount of low energy cavitation without damage or significant reduction in life. The more intense the cavitation is, the quicker the pump will be damaged.
What is the difference between cavitation and air entrainment?
Cavitation is the formation and subsequent collapse of vapor bubbles in the pumped fluid. Air entrainment is the introduction of air bubbles mixed in with the pumped liquid. Both can damage a pump, but damage from cavitation is normally quicker and more severe. Inspection of the impeller and various operational tests can be done to determine if a pump is suffering from cavitation damage or air entrainment damage.
Once cavitation occurs, how can it be corrected?
Cavitation normally occurs because of a poor system design so it is hard to correct after the fact. Designs with inadequate NPSH margin, poorly designed piping systems or those where the pump is expected to run to the extreme right or left side of the performance curve are the most likely to suffer from cavitation. The ultimate solution would be to correct the design deficiencies and/or select different pumps that are more suitable for the pump station requirements.
How can cavitation be prevented?
Preventing cavitation requires good and thorough system design, starting with understanding the factors that affect a system’s propensity to cavitate. Checking NPSH margins, designing piping systems with minimal dynamic loss and selecting pumps that run in an acceptable area of their performance curve all contribute to good station design.
Submersible Solutions is produced by the Submersible Wastewater Pump Association to inform and educate in the design and operation of submersible wastewater pumping systems. For more information, visit pumpsandsystems.com/swpa.