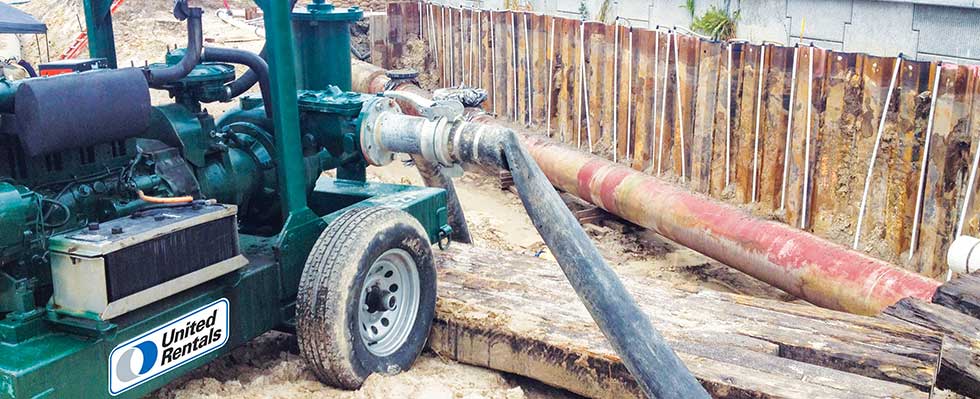
Jobsite dewatering is increasingly essential to today’s construction projects. Excavations are getting deeper as developers are building more levels below ground to gain the maximum value from their real estate investment. At the same time, groundwater levels are rising in many areas due to increases in snowmelt and storms that bring major rainfall.
The success of jobsite dewatering depends on the selection of an appropriate dewatering system and appropriate pumps. Dewatering systems are not one-size-fits-all, and neither are pumps. Pump failure, and resulting downtime, is all too common, especially when the pump is not sized or set up properly.
One of the leading causes of pump failure—pump cavitation—often signals a problem with the dewatering system design, not the pump.
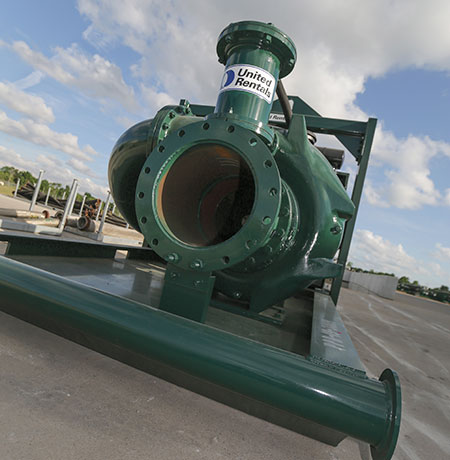
Causes of Pump Cavitation
Pump cavitation happens when air bubbles form in the pump and violently implode. It can cause loud rattling noises, vibrations and pump damage. There are two main reasons for cavitation: insufficient pressure at the suction end of the pump (suction cavitation) and excessive discharge pressure (discharge cavitation).
Suction cavitation occurs when the pressure at the suction end of the pump is too low and the pump cannot take in enough fluid to operate properly. When the net positive suction head (NPSH) falls below the pressure at which the liquid will vaporize, air (vapor) bubbles form and then quickly implode as they reach a
point of higher pressure, such as the pump’s impeller.
Discharge cavitation occurs when the liquid that has been drawn into the pump cannot exit because the discharge pressure is too high. Air bubbles form and then implode as the liquid continues to circulate in the discharge area.
The rapid formation and implosion of air bubbles in the pumped liquid creates shockwaves that can severely damage the pump and reduce its performance or cause it to stop functioning. Pieces of the metal impeller may break off, and the pump’s seals may fail. The pump may consume power erratically. Reduced flow or outright pump failure could bring work on the jobsite to a halt.
How to Reduce Cavitation Risk
The best way to avoid pump cavitation is to choose an appropriate dewatering system for the site and size the pumps properly. Common dewatering methods include wellpoint systems, deep well systems, open pumping systems and sock dewatering systems. Factors used to determine the best type of system include the size and depth of the excavation, the volume of water that needs to be removed and the speed at which it must be drawn down. The percentage of clay, sand or gravel the water contains should be considered as well.
No matter what type of dewatering system is deployed, choosing the right pump is critical. A host of variables must be considered when sizing a pump, beginning with the scope of the dewatering project and the type of fluid to be moved. Moving water that is laden with solids requires a more powerful pump than moving clear water. The choice of pump is also dictated by the required flow rate, the distance
from the fluid source to the discharge point, elevation changes along the discharge route and even the pH of the fluid. If the fluid is acidic, a pump made of corrosion-resistant materials and seals should be used.
One of the most important steps in choosing the correct pump size is calculating the NPSH. This is the difference between the pressure available at the pump’s suction port (the NPSH available [NPSHa]) and the minimum pressure required to keep the pump operating properly (the NPSH required [NPSHr]). If
the difference is insufficient, cavitation can occur.
The NPSH will vary according to the atmospheric pressure at the pumping site, the vapor pressure of the fluid, the vertical difference between the centerline of the pump and the surface of the liquid that’s being moved (the static suction lift) and losses in suction pressure due to friction from the pipes, hoses and fittings.
Reducing the distance between the pump’s intake point and discharge point, when possible and avoiding long lengths of hose or pipe can help ensure that the NPSH will be sufficient to move the fluid through the system at the desired rate.
Partnering With a Pump Expert
Redesigning a dewatering system once a pump fails is disruptive, time consuming and potentially expensive, so choosing an appropriate system and the right sized pump from the beginning is critically important. However, most construction companies are not dewatering experts with deep knowledge of pumps, dewatering system design and NPSH calculation.
Partnering with a temporary equipment vendor that knows pumps and dewatering systems inside and out is one of the most effective ways to avoid dewatering difficulties. The vendor should be able to provide guidance not only on the best dewatering system for the application and the type and size of pump needed, but also on the setup of the system. Although setup is something a contractor can do on its own, the proper placement of a pump and hoses can make the difference between a pump that operates optimally and one that breaks down due to cavitation.
At a time when project owners are closely scrutinizing construction budgets, contractors may be tempted to take a seat-of-the-pants approach to dewatering a site, using whatever pumps and hoses are already on hand and hoping for the best. However, it takes only one failed dewatering attempt to realize the importance of performing the necessary calculations upfront and choosing a dewatering system that will get the job done efficiently and effectively.