Multiple lip seals are commonly used in centrifugal pumps and positive displacement pumps. There are many variations, but one version that has been particularly effective is a triple lip seal arrangement. The key feature is the third outboard lip seal element, which can be used for several functions. Sealed media can be compartmentalized, providing the opportunity to apply any of the API piping plans based on the type of media being sealed. For instance, it can serve as an excluder or a secondary seal in a quench gland design for media that crystallizes or hardens with exposure to ambient temperature and pressure. Unlike a mechanical face seal, there are no rotating parts, and all internal components are not just replaceable, but replaceable on-site by in-house or field maintenance staff. The design of a triple lip seal yields a pressure-actuated sealing element with a membrane-like body, which can be manufactured from many polymer types such as filled or virgin polytetrafluoroethylene (PTFE), polyetheretherketone (PEEK), and polyurethane. Other triple lip seals are also designed and manufactured in various elastomeric and elastomeric energized PTFE configurations (see Figures 1 through 4). In this article, we will focus our discussion on the most versatile sealing element material—filled or virgin PTFE.
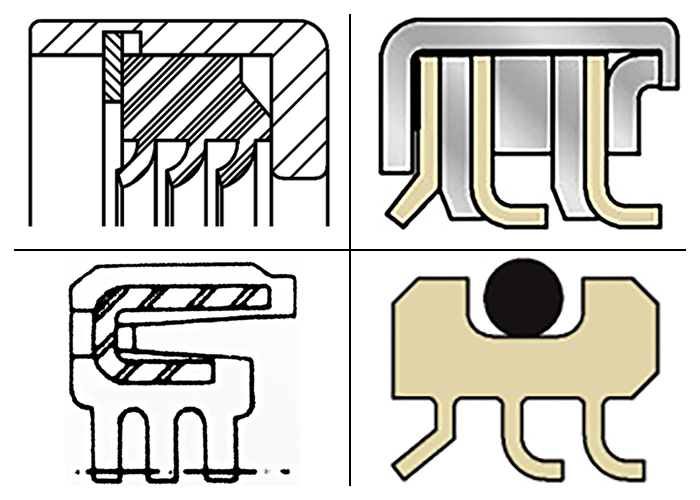
PTFE Triple Lip Seals
Several different materials have been used for lip seals, including various polymers and elastomer blends. PTFE has been the most dominant of the triple lip seal element materials. Properties of PTFE, most importantly low coefficient of friction, yield greater versatility than elastomers due to the need for minimal heat generation at the sealing surface. The key to PTFE is the carbon-fluorine bond. Because this bond is extremely strong, the potential for chemical attack is dramatically reduced, creating a nearly inert, tough, non-flammable, lubricious compound after polymerization. When using filled PTFE, properties can be achieved that both enhance the lubricious surface and dissipate heat from the sealing area. These properties also allow dry-running operation without generating detrimental heat at the sealing surface. At the microscopic level, the surface finish of the lip seal has void spaces that allow gaseous and liquid particles to flow at lower actuating pressures. When operating in the proper viscosity range, fluids can only flow in one direction—from the lip seal’s back to front—due to the flexibility of the lip seal material. Flushing the sealing surfaces can take place during shutdown, or while the pump is in service.Lip Seal Design Theory
Temperature effects at the interface of the lip seal element and mating shaft or sleeve are crucial to seal performance. Temperature directly affects the wear rate of the lip seal element. As the frictional heat between the seal contact area and mating shaft or sleeve surface increases, the seal element’s beneficial properties—such as its tensile strength, modulus of elasticity, and elongation—begin to degrade. If this heat does not dissipate quickly enough, seal elements may fail. The lip seal element should be designed with the proper material and thickness so that it can conduct the interface frictional heat from the mating interface to the media. These thermal effects may be treated for a lip seal element using Fourier’s law, the fundamental differential equation for heat transfer by conduction,
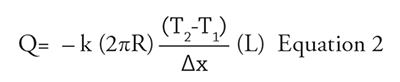
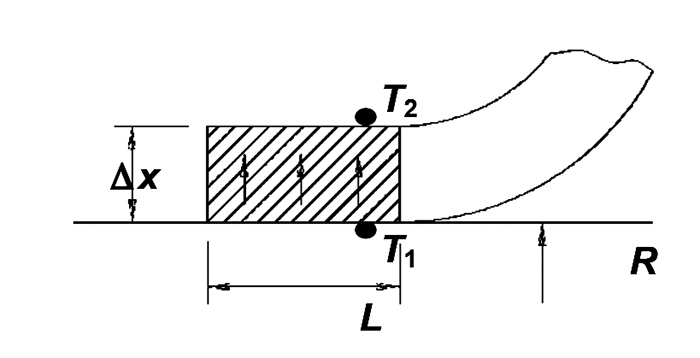

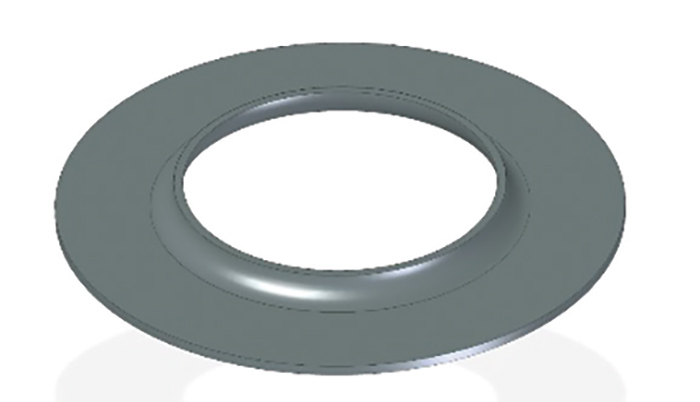
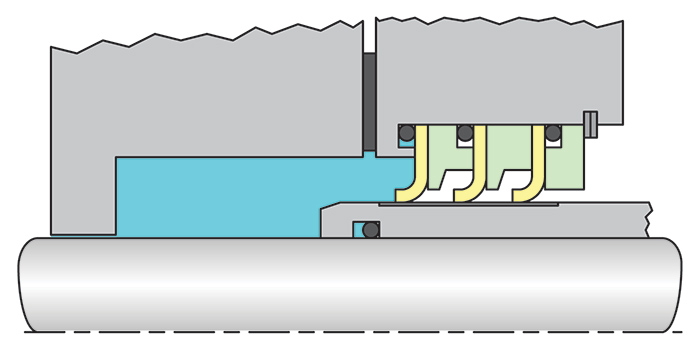
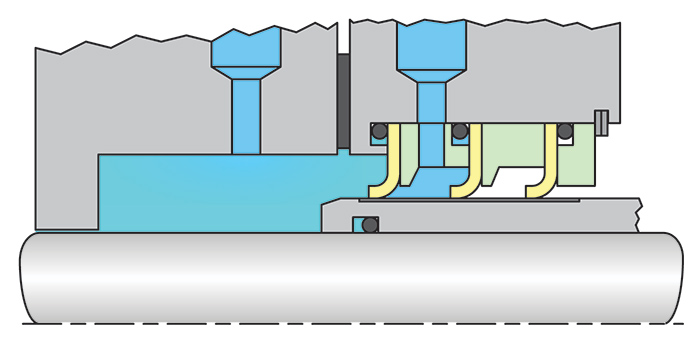
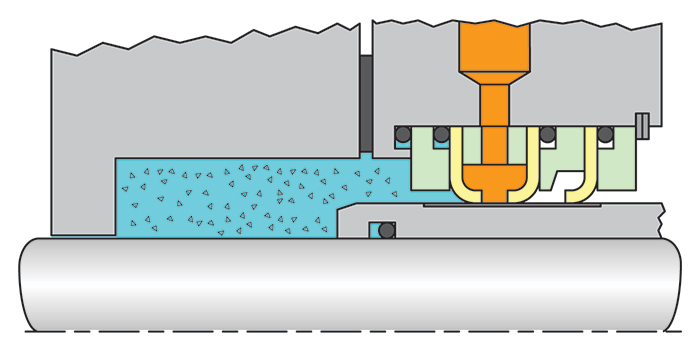