A frequently stated expression around the pump industry is that viscosity is the Kryptonite of centrifugal pumps. Pardon the allusion to Superman, but it is a reference most of us not only relate to, but also understand. Further, viscous fluids do have a negative and weakening effect on centrifugal pump performance. Viscosity is a measure of a fluid’s resistance to flow at a given temperature. You can also think of it as fluid friction. A more technical definition would explain viscosity as a force required to move a liquid plane (think plate) of some unit area, over some distance above another plane of equal area in a defined time period. In training classes, I simply define viscosity as a fluid’s resistance to pour but, more importantly, a resistance to be pumped. Isaac Newton was probably the first person we know to quantitatively define a coefficient of viscosity. His concept and related work was not completed, but was later refined by Jean Leonard Marie Poiseuille (see Poiseuille’s Law).
Why are we concerned about viscosity in regards to centrifugal pumps?
Mainly because viscosity has such an extraordinary and often negative effect on centrifugal pump performance. An increase in viscosity will dramatically reduce a pump’s efficiency in conjunction with marked reductions in head and flow. The net result is an increase in the brake horsepower required for the driver.Viscosity Corrections
All centrifugal pump performance curves are based on pumping water, unless stated otherwise. When I started in the pump business, there were no computer programs to cipher the necessary viscosity corrections and the manual methods could take hours to complete. With the advent of computerized programs for pump selection, it is now simple to correct the pump’s performance for viscosity in one keystroke, but we often overlook the details and effects of what viscosity changes do to the pump performance and especially the required brake horsepower. Prior to computer programs, there were basically three methods to correct a centrifugal pump’s performance from water to viscous.- The A.J. Stepanoff model was viable at the best efficiency point (BEP) for head and flow but reliability and validity diminished with increased departure from the BEP.
- The Paciga method was slightly better than the Stepanoff model because it could be more accurate across a wider range of flows. Paciga had incorporated specific speed and a flow ratio (actual flow as compared to BEP). The down side was that as viscosity increased the reliability diminished. This was mostly due to the effect of the Reynolds number in the formula calculations.
- Hydraulic Institute original method using viscous correction charts to obtain viscous correction factors (for head, flow and efficiency). The method was an improvement over previous ones because of the ease, accuracy and wide range of applicability. For people who have been in the business for some time, it would be prudent to review the newer methods presented by the Hydraulic Institute (Refer to ANSI/HI guideline 9.6.7-2010). The new method uses a formula called parameter B to yield viscous correction factors. The newer method also eliminates some of the confusion and inaccuracy in the 100 gallons per minute (gpm) range.
Corrections to Pump Curves
In a perfect world, a centrifugal pump performance “curve” would actually be a straight line, but in the real world, it is curved due to losses in the pump. The major factors are a combination of mechanical, leakage, shock and disc friction losses. Disk friction is the major contributor and most important factor when quantifying the losses. The curves as mentioned are based on water performance, but with applications on viscous fluids those water curves must be corrected for the viscosity to be accurate. The head, flow, efficiency and brake horsepower (BHP) curves will all require modification (viscous corrections).At what minimum value of viscosity to start corrections?
The pump manufacturer is the best source for this value, as it will depend on the application, fluid personality and the pump geometry. Note that at 100 centipoise, the viscous effects will be significant. I will state that at 30 to 40 centipoise or greater, you should use the corrections or risk adverse effects. I also recommend that somewhere in the area of 5 to 10 centipoise, you must at least be aware and conscious of the effects however minor. Since checking the correction curves is so easy these days it would be unwise not to check.Impeller Shape & Size Effects
The lower the specific speed (Ns) of an impeller, the higher the disc friction will be. This is simply due to the geometry of the impeller and the 90 degree flow angle that the fluid enters and then exits the impeller. As an impeller’s specific speed increases, the entrance-to-exit angle becomes lower and the interaction with the fluid is less. The smaller an impeller is, the more likely the disc friction effects will be higher simply because the surface area of the impeller and casings have more interaction with the fluid than in a larger pump.Maximum Viscosity for a Centrifugal Pump
I am frequently asked; what is the maximum viscosity that a centrifugal pump can handle? My short answer is that “it depends.” A better and less flippant answer is to consider the reduction in pump efficiency (also head and flow) and calculate the maximum required and corrected horsepower (hp) for the viscous fluid. Several references limit centrifugal pumps to a maximum of 3,000 centistokes. (Note that this limit is also published as 3,300 centistokes.) There is an older technical paper on the subject by C.E. Petersen (delivered at the Pacific Energy Association conference in September 1982). Mr. Petersen presents an argument that the maximum viscosity can be calculated by the size of the pump discharge nozzle. Mr. Petersen postulated a formula as follows: Vmax = 300 (D-1) Equation 1 Where: Vmax = the maximum kinematic viscosity in SSU (Saybolt Second Universal) allowed for that pump D = the diameter of the discharge nozzle in inches. I would only use this formula as a rule of thumb. To be accurate, you should have input from the pump manufacturer on this subject with regard to shaft torque and hp limits. There may also be frame limits and occasionally (rare) impeller blade load torque limits. Depending on the pump size and impeller geometry, the viscosity limits for the average centrifugal pump will vary from 250 to 700 centipoise, and I have witnessed many pumps successfully pumping fluids in excess of 1000 centipoise. If your application is above 250 centipoise, I recommend you work with your pump manufacturer/vendor to arrive at the answer. The two important points to take into consideration are these:- There is a torque and hp limit for the pump shaft that will be negatively impacted with an increase in viscosity. Make sure to check this viscosity correction factor to ensure a satisfactory and reliable installation.
- You may still be able to pump the highly viscous fluid with the centrifugal pump, but there will be a point of diminishing returns due to reduced efficiency. Perhaps you are using 25 hp to pump the viscous fluid with a centrifugal pump that would only require 5 hp with a positive displacement pump.
Horsepower/Torque
All pump shafts have a speed, horsepower and torque limit. In the case of single stage pumps many manufacturers will express this as a hp per 100 revolutions per minute (rpm) limit. Note that torque is inversely proportional to horsepower, so the lower the speed the more torque is applied to the shaft. While most shaft limits are based on speed, hp and continuous torque limits, keep in mind that if the pump is driven by an engine then the limits will be further reduced (internal combustion means intermittent in lieu of continuous torque). Additionally, if the pump shaft is side loaded, as in the case of belt or chain drives, there will be a striking reduction on the shaft limits due to the cyclic bending fatigue factor.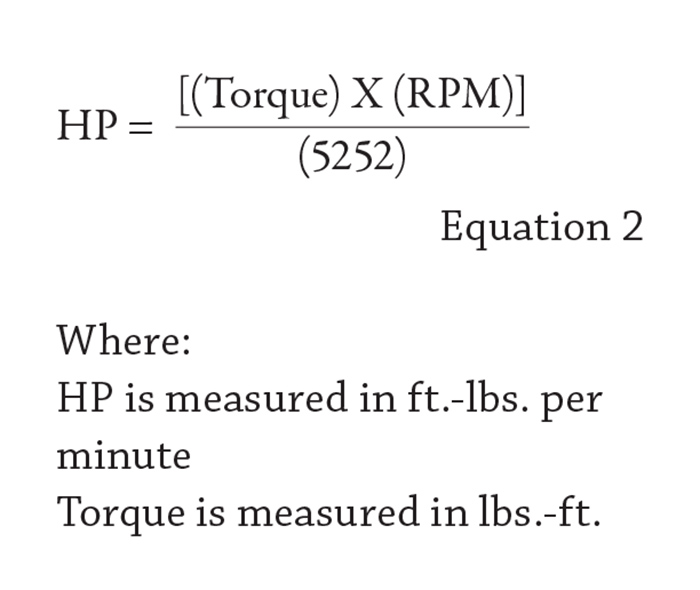