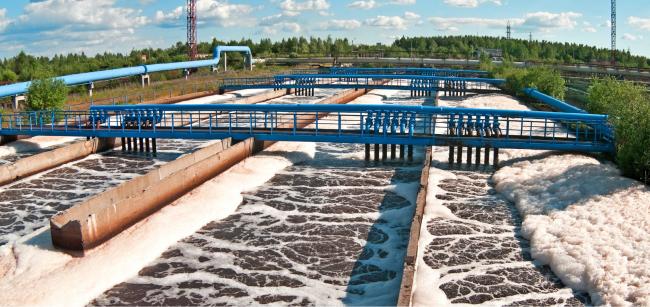
These pumps enhance cost efficiencies and reduce breakdowns.
No matter where a community is located, one thing remains constant—it will produce both solid and liquid waste. Wastewater includes household wastes (from toilets, showers and sinks), storm water runoff and industrial waste from commercial facilities.
Most modern communities dispose of wastewater through a sewer system, where it is collected and transported through a network of pipes and pump stations until it reaches a wastewater treatment facility. These treatment facilities remove physical, chemical and biological contaminants from the wastewater and produce a liquid waste stream that is suitable for reuse or for discharge back into the environment.
Once it reaches a treatment facility, wastewater undergoes an extensive treatment process that ensures that it is sanitary enough for reuse or release back into the environment. This process can be extremely harsh and involves specialized, industrial pumping equipment. Pumps are used during virtually every step in the treatment process and serve many purposes—including inlet raw wastewater pumping, grit removal, chemical feed and sludge transfer.
The Challenge
To say that the wastewater treatment process is unforgiving and abrasive on pumping equipment would be an understatement. Pump breakdowns due to erosion and clogging are constant. These breakdowns only increase when the incorrect pumping technology is used. Selecting the correct pump for each application is essential.
“One of the biggest problems we have seen when it comes to pumping systems, is that if you don’t select the correct pump for the right application—and it might be an excellent pump—it still isn’t going to function properly,” says Scott Maring, assistant superintendent of wastewater treatment for the Metropolitan Sewer District of Cincinnati, Ohio. “If we buy a pump that is able to handle a certain type of application but just beats itself up in the process, it’s not going to be very reliable and is going to have lots of problems that are symptomatic of other things. Many factors go into why we purchase a pump. It has to be able to perform reliably in its service and be maintainable. It is critical that the pump is perfect for the application. If not, we would be replacing a lot of pumps.”
Sludge Transfer
One application in which extra caution is needed prior to selecting a pump is sludge transfer. As mentioned above, once wastewater reaches a treatment facility, it must go through different treatment processes. Two of these processes include primary and secondary treatment, and both produce large amounts of sludge.
During primary treatment, wastewater flows into a primary clarifier or sedimentation tank. Once collected, the wastewater is held until the larger, heavier solid objects settle to the bottom, while the oil, grease and lighter solids float to the surface. What settles is called primary sludge, which is then removed from the tank by mechanical scrapers and pumps. Occasionally, primary sludge is pumped out of the facility to a different location where it is treated and reused in different ways.
![]() |
Wastewater treatment facilities use specialized pumping equipment to help provide sanitary water. |
Only about 60 percent of the suspended solids are removed during primary treatment. Therefore, the wastewater must undergo a secondary treatment process. This secondary treatment involves removing biological matter and soluble materials that require oxygen for decay from the wastewater, as well as the removal of any additional suspended solids. Secondary treatment can be accomplished through many methods. One of the most common methods is the activated sludge process.
Activated Sludge Process
During the activated sludge process, wastewater and biological sludge are pumped into an aeration tank and combined. Air is then injected into the mix to help break down the biological matter. This mixture then flows to a second clarifier, or settling tank, where the activated sludge settles and is pumped out. Typically, about 35 percent of the sludge is then returned to the aeration tank to help maintain a high population of microbes to break down the organic material. This sludge is commonly referred to as return activated sludge. Because more activated sludge is produced than is needed for return sludge, any surplus activated sludge, commonly referred to as waste activated sludge, is pumped out of the tank for disposal.
Due to the difficulty inherent in pumping sludge, gravity is used to transfer sludge whenever possible. However, whenever gravity is not a viable transfer method, heavy-duty pumping equipment is required to do the job. Since sludge is a viscous, thick material that often contains large amounts of grit and grease, not every type of pumping technology is an ideal choice. When a pump has not been specifically designed for sludge transfer applications, the end-user often experiences a variety of problems.
“If grit gets into the sludge, it can be destructive to the equipment,” explains Maring. “So if we don’t get the grit out early, it just wears on all the pump’s rotating pieces. Grit, along with grease, can thicken the sludge and make it very difficult to pump.”
Primary Sludge and Waste-Activated Sludge
Although the wastewater treatment process is designed to remove any large solids before primary and secondary treatment occurs, removal of these objects is not flawless. Often, primary sludge and return or waste activated sludge will still contain large, stringy solids. These solids frequently clog the pumping equipment. This happens when solids come in contact with the pump’s impellers, especially if the pump’s discharge port is too small to pass these objects. Additionally, even pumps designed to pass large solids can experience clogs when stringy material gets weaved into a mass and gets caught in the pump. Regardless of the specific cause, service technicians must disassemble and clean the pump whenever a clog occurs. This shuts down the treatment process and can result in unnecessary operating costs.
“Grit and grease are two of the biggest killers in this type of pumping application, as are the large objects that clog the pump,” says Maring. “Because of these issues, it wears valves, damages instrumentation, and clogs a pump’s piping. Once the pump’s pipe is restricted, it’s essentially changing the dynamics of the pumping system. If the pipe is choked off so that it’s smaller, the pump has to work harder to squeeze the sludge through a smaller hole. This is not very efficient.”
In addition, pumping equipment accounts for a large amount of the energy consumed at a wastewater treatment facility. Because of this, a pump that is able to continually perform at its best efficiency point (BEP) while pumping sludge is the ideal option. Pumps represent a large part of the facility’s total investment in equipment. Pump maintenance and replacement can be costly, which increases the cost of investment, so pumps that minimize maintenance and downtime are the preferred choice.
“Fixing and replacing pumps is a significant part of our job,” says Maring.
![]() |
Pumps represent a large part of the facility's total investment. |
Therefore, the pumping equipment selected for sludge transfer applications must not only be designed to handle large solids but also be cost-effective and require low maintenance. Fortunately for those involved in the transfer of sludge, a pumping technology is available that offers a smooth, cost-effective operation with trouble-free maintenance.
The Solution
The preferred pump for demanding wastewater applications is the centrifugal vortex pump. This type pump has been designed with a semi-open impeller recessed into the volute section of the pump. A recessed impeller design allows for the clear passage of solids through the ports. Because of this, vortex pumps are ideal at handling the large, stringy and abrasive solids often associated with primary and activated sludge.
“When it comes to the pumps we use during our primary sludge applications, we typically use centrifugal pumps that feature end-suction, open-face type impellers that can pass at least three-inch solids,” says Maring.
Unlike typical centrifugal pumps, the impeller of a vortex pump is recessed into the back of the pump’s casing and creates a liquid vortex in the open casing which directs solids, slurry, sludge, grit and stringy or fibrous material through the pump.
A vortex design offers some significant advantages during sludge transfer applications. Since the impeller is recessed and not in the primary flow path, it minimizes contact with the process fluid and the majority of the solids that pass through the pump, allowing for clear passage of solids with minimal clogging. Basically, whatever goes into the pump will be pumped out as long as the solids are nominally smaller than the ports. This is ideal when handling liquids that contain long stringy material and larger diameter solids. Lowering the amount of clogs results in fewer breakdowns.
In addition to allowing for the clear passage of solids, the vortex pumping action also offers other advantages over traditional pumping technology. Because only 15 to 20 percent of solids come into contact with the pump’s impeller, erosion is greatly reduced. The design also allows for the handling of entrained air far beyond the capabilities of a standard centrifugal pump. Additionally, because of their concentric casing design, recessed impeller pumps offer more reliable operation at low flows and can even shutoff for extended periods of time.
Because pumping equipment can represent a large part of the facility’s investment in equipment, the total cost of ownership should be a major consideration when selecting a pump. Not only will centrifugal vortex pumps help reduce maintenance costs, but typically will be much less expensive to purchase compared to other pumping technologies. For example, on a price-per-given-flow basis, centrifugal vortex pumps are typically much less expensive to purchase than positive displacement (PD) pumps.
Certain vortex centrifugal pumps can help maximize reliability during wastewater applications. This includes the transfer of sludge and slurries with large particle solids, materials with entrained air and stringy or fibrous materials. Designed around the seal, where 90 percent of pump failures occur, these pumps help improve mean time between failures, resulting in reduced maintenance costs. In addition, the have been designed to offer the widest window of operation off BEP than any other conventional centrifugal pump.
Some vortex pumps feature heavy-duty, solid, low deflection shafts that prevent common vibration damage and create greater stability at the seal area to improve seal life. They also feature heavy-duty bearings that offer a greater load capacity and extend bearing life, while the specialized seals provide non-wearing lifetime protection for radial and thrust bearings. This all results in better pump reliability even in the most extreme environments.
These pumps are available in different frame configurations and can reach capacities of 340 cubic meters per hour (1,500 gallons per minute). Available with discharge passages from 2 to 4 inches, the larger pumps can pass solids up to a nominal 4 inches. These vortex pumps are available in standard, ductile iron or CD4MCu material, with an optional spacer flange that allows for the removal of the separate suction cover for cleanout without disturbing piping.
Conclusion
Every community produces wastewater, and the wastewater must be treated. Selecting a centrifugal vortex pump for sludge transfer applications may go a long way in helping treat wastewater in a cost-effective way.
* No endorsement of Blackmer® System One® Vortex Pumps by Scott Maring is to be inferred.