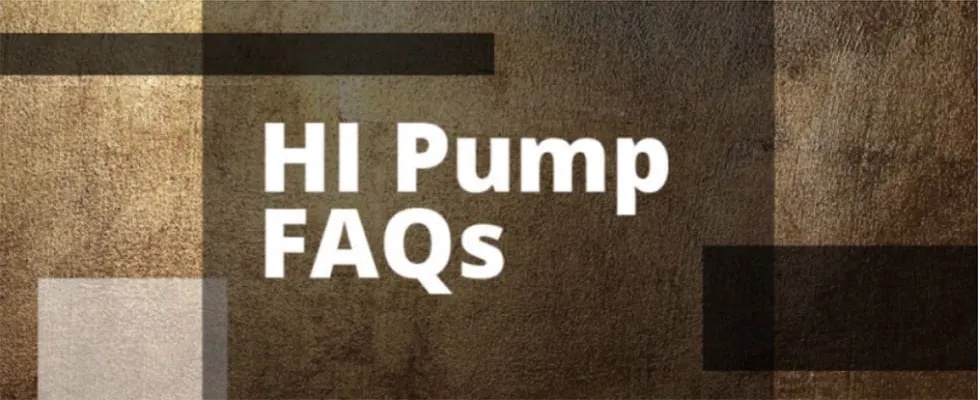
Centrifugal pumps and positive displacement pumps have differing hydraulic designs, which results in unique application considerations that affect which type is best for an application.
Centrifugal pumps utilize a rotating impeller to impart kinetic energy to the applicable fluid, and the fluid exits the impeller radially. The performance of a centrifugal pump is such that the flow rate is variable as a function of system differential pressure or total head. This means it can achieve variable flow while operating at a constant rotational speed (Image 1). Additionally, centrifugal pumps shear the liquid they are pumping; therefore, their performance is significantly affected by the liquid viscosity.
One other factor to consider is that even though centrifugal pumps can operate over a wide flow range, they are specifically designed for a single best efficiency point (BEP) flow rate. As the pump is operated away from BEP to lower or higher flow rates, the efficiency will decrease and the allowable operating region (AOR) is limited. Another factor to consider is that if the application considers low flow rates and high differential pressure, the centrifugal pump design to meet this condition will have a relatively low efficiency compared to a centrifugal pump designed for a higher flow rate.
Positive displacement pumps include rotary and reciprocating pump technologies. Rotary pumps have meshing parts that trap liquid and convey it from the pump inlet to the outlet. Reciprocating pumps have pistons, plungers or diaphragms, which function by trapping a fixed volume of liquid in the pumping chamber and forcing or displacing it through a discharge pipe. The positive displacement design results in a nearly constant flow rate as a function of differential pressure (Image 1), which is a key difference compared to centrifugal pumps. Additionally, these pumps have less shearing of the liquid and therefore their performance is less affected by the liquid viscosity. For these reasons, positive displacement pumps are commonly used in applications that require low flow rate, high differential pressure or constant flow rate, or have a high viscosity liquid.
One application where positive displacement pumps are often used is in the precise metering of liquids. Because these pumps have limited flow variation as a function of pressure, they can be designed to accurately and precisely meter the injection of chemicals or additives into a system. Positive displacement pumps for this specific application are called controlled volume-metering pumps (CVMP) or dosing pumps. CVMPs are widely used in dosing applications in food, chemical and pharmaceutical processing.
For more information on positive displacement pumps and their applications, refer to the Positive Displacement Pump Basics course at training.pumps.org.