A large chemical company in Tennessee had experienced frequent pump failures due to solids and pH issues in a waste pit application. Mechanical seal failure due to solids contamination was suspected to be the main culprit. The manufacturing facility had a sump that relied on two effluent pumps to transport wastewater out of the plant. While one pump had initially been intended to operate as a backup, both pumps had been operating continuously to accommodate the high flow rate into the wastewater sump. Solid materials, such as zip ties, plastic tags and bags that entered the wastewater stream from drains throughout the production facility would enter the wastewater sump and damage the effluent pumps. When the first pump failed, it was sent to a repair facility in Virginia. The repair technicians found that the plastic debris had become trapped on the backside of the pump impeller, causing the mechanical seal to fail. The mechanical seal failure allowed wastewater fluid to enter the motor, resulting in failure of the effluent pump. The first effluent pump was repaired and reinstalled, but only lasted a month in the manufacturer’s wastewater sump. According to a company who provides rental equipment, the chemical company had an emergency spare, but it failed after a few weeks. They learned that the manufacturer’s in-house maintenance team had set up a backup diesel pump in case both effluent pumps failed at the same time. At that point, the rental equipment company provided them with a submersible shredding pump to use as an emergency spare.

A Temporary Solution Provides Lasting Value
The rental equipment company worked with an inside applications engineer at the pump manufacturer to select an explosion-proof, submersible, corrosion-resistant shredder pump for the chemical manufacturer’s wastewater sump. It was a priority for the chemical manufacturer to keep workers safe and with the potential for an explosive atmosphere, the plant required pumps with explosion-proof motors. The submersible shredder pump was chosen for its FM-approved explosion-proof motor (for use in Class I, Division 1, Groups C & D hazardous locations) as well as its ability to effectively shred and pass large solids. There’s a constant flow into this wastewater sump, and even though it’s 30 feet deep, it’s critical that the sump doesn’t overflow. The pump manufacturer was confident that the submersible shredder pump was going to pump reliably in that sump because it’s made of 316 stainless steel, has a cutting impeller with a tungsten carbide tip to shred solids and an epoxy-coated motor housing, which was needed because of the high pH of the pumped fluid.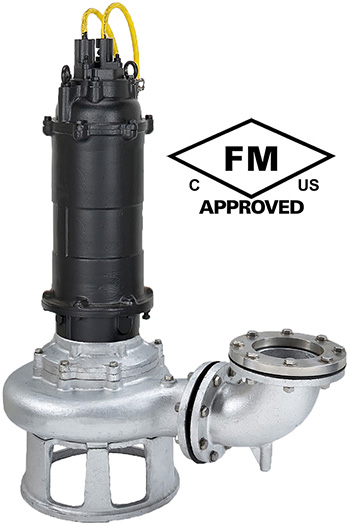