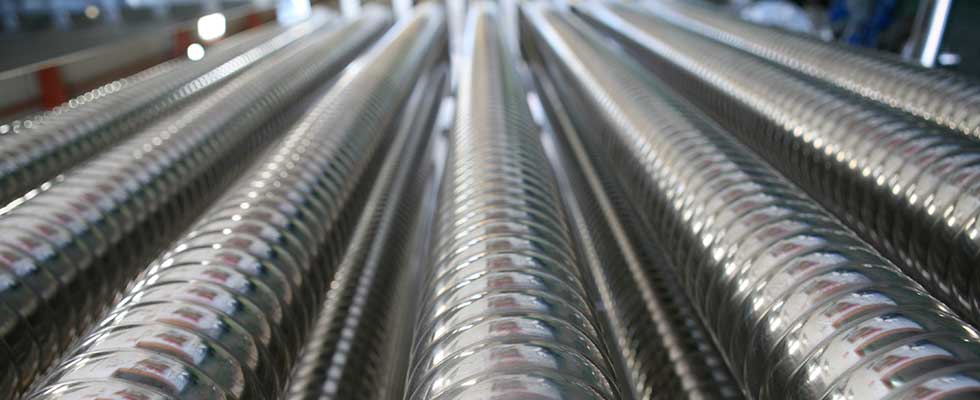
Heat exchangers are crucial to many processes in the water industry, whether as part of an aerobic or anaerobic digestion plant, for cooling or evaporation, and for sludge concentration. There are many different types of heat exchangers available, and choosing the right one can appear daunting.
For both economic and environmental reasons, maximizing productivity is essential, and correct heat exchanger selection is key to that success.
What Is Productivity?
Productivity is measured by the ratio of output per unit of input. Many water companies see it as a balancing act—how can they increase output without increasing costs?
The answer is closely linked to efficiency, ensuring every part of the process is optimized.
Understanding the Process
The most important criteria when specifying a heat exchanger is to ensure that it will be fit for the particular purpose. To do this, it is important to understand both the material being treated, the heating (or cooling) medium and the process involved.
Is the material in question liquid (dirty or clean water) or semi-solid (sludge)? Is it viscous? What is the extent of the temperature difference required?
Other information must be provided for correct heat exchanger selection. For example, does the product contain solid particles? Consider also whether it is shear sensitive, if the process needs a scraped surface heat exchanger (SSHE), or whether well-designed corrugated tubes will be enough to prevent fouling.
Also bear in mind the space available for the heat exchanger and the connection pipework and fittings. The more information, the more likely the end user is to get the right heat exchanger for the job.
Avoiding a False Economy
It may be that more than one type or model of heat exchanger is suitable. To ensure productivity, it is crucial to consider the total cost of ownership (TCO). Although some operators can be swayed by the initial purchase price, this can be a false economy.
The life cycle cost of a heat exchanger, particularly one used to process difficult materials, heavily depends on cleaning and maintenance costs. Buying a cheaper design that is more prone to fouling can quickly become more expensive to operate.
Consider the TCO of a heat exchanger, not just the purchase price. The Hydraulic Institute has a whitepaper explaining how to determine the TCO of equipment. Visit pumps.org for more information.
Energy Efficiency
The running costs of a heat exchanger also have a large effect on its overall financial viability, so selecting a heat exchanger that is energy efficient is key to enhancing productivity. Consider corrugated tubes specifically designed for high fouling sludges.
There are a number of scraped-surface heat exchanger designs available that contain a stainless-steel scraping mechanism, which is hydraulically moved back and forth within each interior tube. This movement minimizes potential fouling of the product by keeping the tube wall clean, and also creates turbulence within the material.
Both actions help to increase heat transfer rates and, together, they create an efficient heat transfer process ideal for high-fouling viscous materials like sludges.
Beware Hidden Costs
Using the wrong heat exchanger can prove costly in terms of maintenance and spare part costs. Another consideration is the overall installation costs and whether fitting the heat exchanger will require the purchase of ancillary equipment.
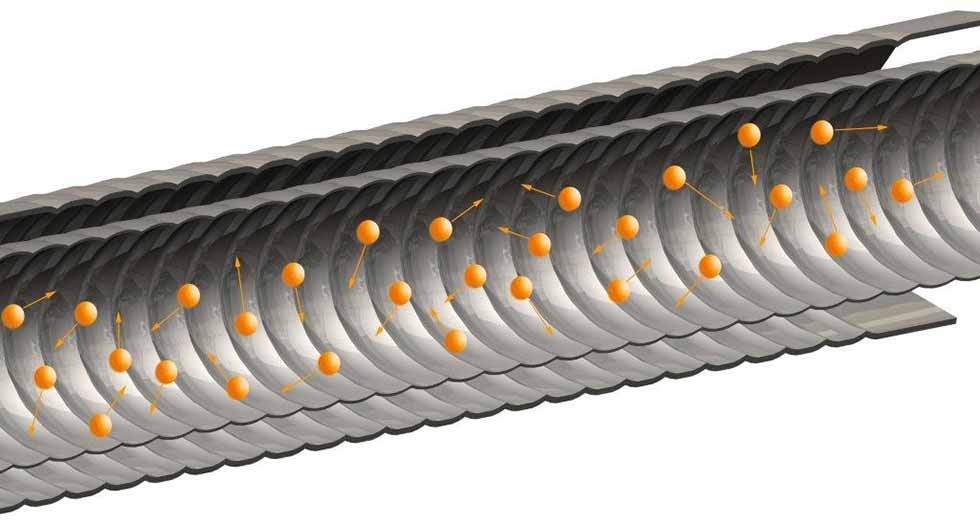
Corrugated designs can result in improved efficiencies, providing comparable thermal performance to other designs, but in a smaller footprint.
These can often be skid- or frame-mounted, reducing the need for significant support infrastructure. Both standard clamp and flange fittings are typically available, although a bespoke fitting can often be fitted and supplied.
A Balancing Act
While a low purchase price may appear attractive, with most of the TCO coming from running costs, keeping expenses lower over the life of a heat exchanger will provide a greater return on investment in the long run. Whatever solution is chosen, consider energy efficiency, maintenance requirements and the costs of any ancillary equipment before signing on the dotted line.
Put simply, specifying the wrong heat exchanger could decrease user productivity. Choosing the right heat exchanger will almost certainly increase it.