Improve reliability in LNG and CNG applications.
Bal Seal Engineering
12/19/2018
Designing a valve that performs consistently in cryogenic temperatures, high pressures, and thermal cycling of liquefied natural gas (LNG) and compressed natural gas (CNG) is one tough job. But choosing the right seal can make it a lot easier.
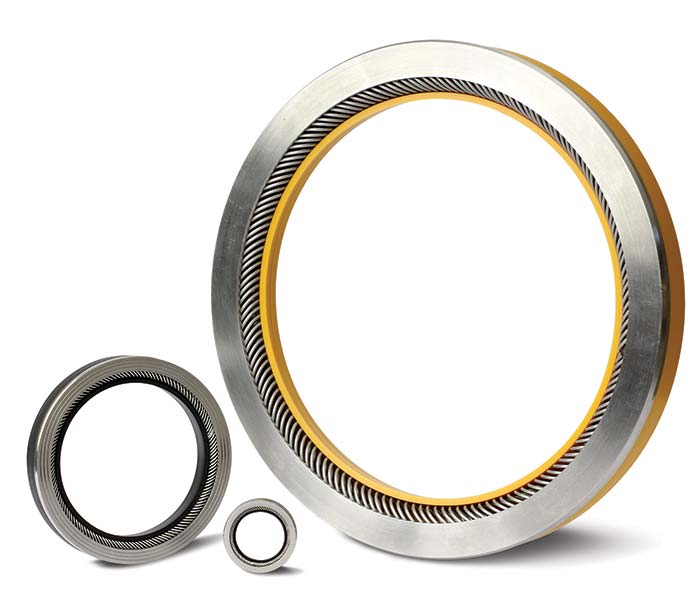
The MVPs of Energy
For decades, valves of all types have played a key role in the movement of product throughout the energy industry. They are considered especially important in LNG and CNG operations, where they facilitate flow in processing, liquefaction, loading and transport stages. Under demanding service conditions, valves are expected to perform for long intervals with high levels of consistency and reliability, and their failure can present significant danger to people and equipment, as well as loss of productivity and profit. In LNG/CNG operations, valves can regularly encounter temperatures below -320 F (-196 C) and pressures above 750 pounds per square inch (psi). They are also subjected to periodic variations in temperatures known as “thermal cycling,” which can result in hardware expansion as well as shrinkage and material stresses. These factors make reliable, long-term valve operation an engineering challenge.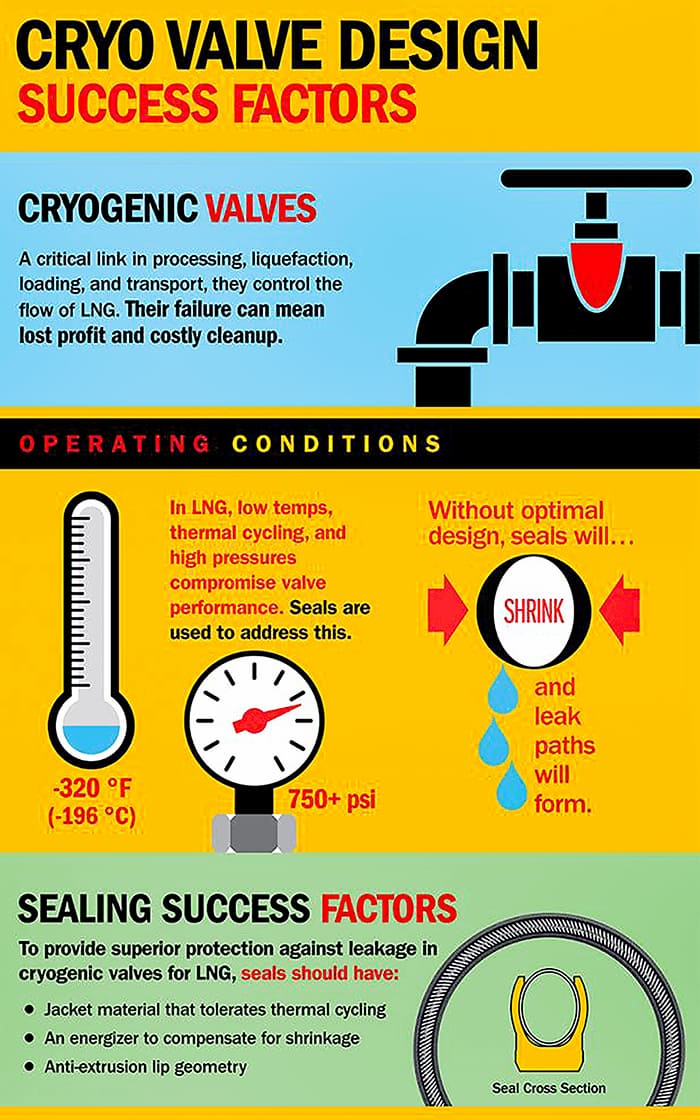