Irrigation systems are dependent on sound pressure management techniques, which are typically incorporated at the design phase of the project. Controlling pressure is a critical component of designing an agricultural irrigation system, whether it is a drip, micro-spray, sprinkler or pivot system. For an irrigation system to adequately and uniformly distribute water to the intended crop, the water must be dispersed within the suggested performance range of the irrigation manufacturer. For sprinkler irrigation, if pressures exceed the manufacturer’s recommended levels, the sprinklers will mist; in a windy environment, water will be wasted. If pressures are too low, the sprinklers will experience a doughnut effect that will negatively impact water distribution near the head of the sprinkler. Drip or micro irrigation systems are built to respond to low pressures, so overpressure can damage the emitters, spray units or the low-pressure piping system. Having reliable low pressure is vital. Large drip or spray systems often have higher pressures near the water source (often a pump) and lower pressures at the extremities of the system because of pressure loss in the piping system. Controlling the higher pressure close to the source also is important. Pumps are required if a system produces insufficient pressure to obtain the minimum requirements for the irrigation equipment. This could be the result of insufficient pressure from a community-provided water source (piping network), using a well or pond as a water source or elevation increases that decrease pressure at greater heights. Pumps add another critical component to an irrigation system—pressure relief. Starting up or shutting down can cause surges or transients, so incorporating a pressure-relief valve is good practice. Numerous irrigation solenoid valves turning off and on also can add to system surges. Incorporating pressure relief valves will allow the system to dump excess pressure to the atmosphere when pressures exceed maximum levels. The larger the irrigation system, the greater the need to carefully analyze pressure requirements. A qualified irrigation consultant can complete a hydraulic study on the proposed system and ensure that pressures throughout the system are within the pressure range of the piping network and the irrigation manufacturer’s equipment.
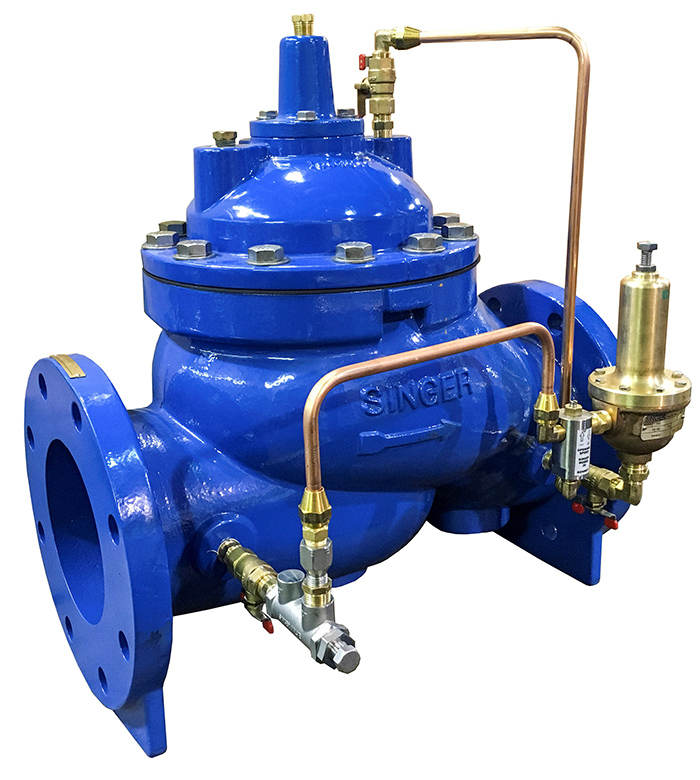
Standard Pressure-Reducing Valve
Standard pressure-reducing valves are available from ½ inch to 36 inches. They manage downstream pressures and are usually offered in ductile iron with a heat-fusion epoxy coating. Stainless steel options are available for 6 inches and smaller. For most irrigation applications, American National Standard Institute (ANSI) flanges will be either Class 150 or Class 300 pound rating. Models 3 inches and smaller are available in thread (Female National Pipe Thread [FNPT]) or flange, while larger sizes are only available flanged. Automatic control valves maintain a constant downstream pressure regardless of fluctuation in upstream pressures. This is different than direct-acting pressure-reducing valves that allow the pressure to change as flows change. Automatic control valves are also known as hydraulic control valves because they require no electricity and the pilots are adjustable, allowing the downstream pressure to be changed. To operate effectively, these types of valves require a differential pressure across the valve of about six meters.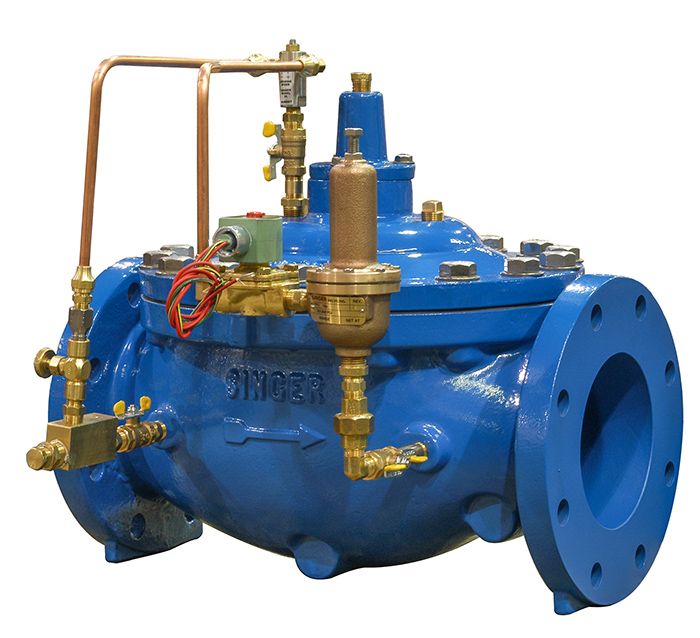
Standard Pressure-Reducing Valve with Solenoid
A solenoid can be added to a standard pressure-reducing valve so the equipment will respond to a timer. For example, this might be used as a master control valve for a system coming off a shared supply. The master valve is only on when irrigation is required. When irrigation is not required, the system is not pressurized.Pressure-Relief Valves
Pressure-relief valves are designed to protect an irrigation system from over-pressurization (usually pump-related) and are mounted off a tee near a pump. If there is a surge in the system or over-pressurization, these valves quickly open and discharge water into the atmosphere. They are fully adjustable to any pressure by rotating the nut on the pilot. In normal operation, these valves remain closed and only open quickly if pressure exceeds the set point. This prevents over-pressurization and helps avoid damage to downstream equipment. In addition, if valves downstream close too quickly resulting in high pressures or a surge, the pressure-relief valve will quickly open, relieving pressure and protecting equipment.Material Quality
For harsh environments, the following critical components must be specified:- 316 stainless steel seat (not bronze or 303 stainless steel)
- 303 stainless steel fasteners on the exterior of the valve
- 316 stainless steel stem (not 303)
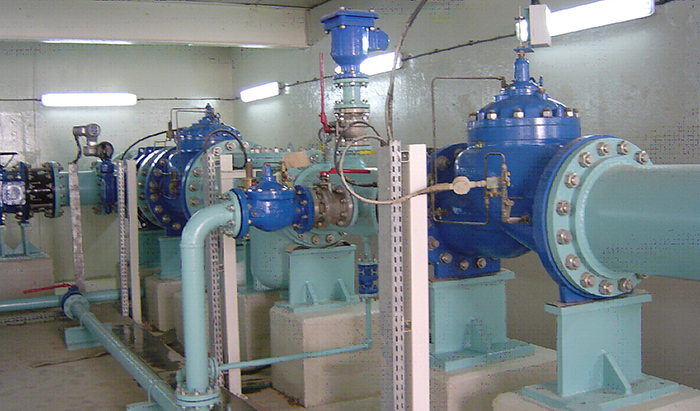