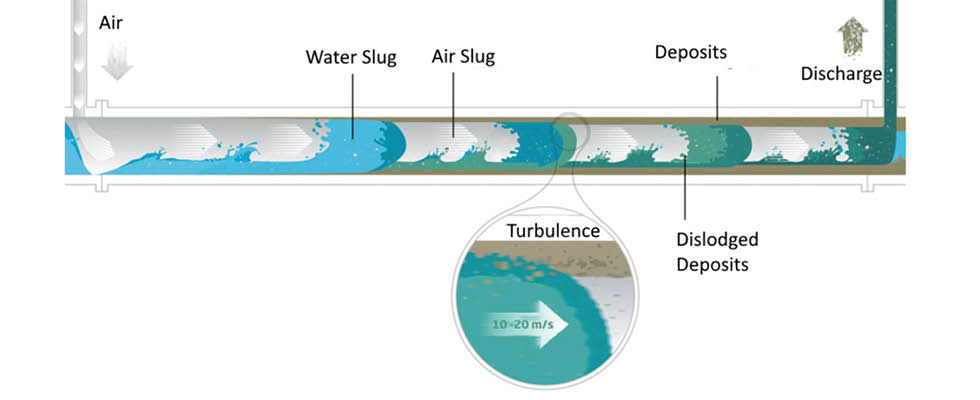
Clean-in-place (CIP) is a crucial process in the food, dairy and beverage industries to maintain sanitary conditions and prevent product contamination during production. Traditional CIP methods have been employed for years, ensuring effective cleaning of process lines. However, as industries strive for greater efficiency, reduced resource consumption and improved cleaning capabilities, innovations in the CIP process have become essential.
This article explores the traditional methods of CIP and introduces technologies that optimize chemical, energy and water consumption while delivering better cleaning performance. By combining traditional technologies with the latest methods, industries can take a significant step forward in achieving more cost-effective and sustainable CIP systems.
Traditional CIP Methods
The traditional CIP process has been widely employed in various industries, showcasing its adaptability and effectiveness in ensuring sanitary conditions and mitigating product contamination. Over the years, the process has undergone numerous iterations, each with nuanced differences tailored to specific applications. As industries continue to seek optimal cleaning solutions, the evolution of the traditional CIP process paves the way for the integration of advanced technologies and innovative approaches to achieve even higher levels of performance and sustainability. One of the more conventional CIP processes commonly involves the following steps:
Pre-rinse: Water is used to remove loose debris and residues from the equipment, generally at a velocity of 6 feet per second or greater.
Alkaline cleaning: An alkaline solution is circulated through the process lines. This step method involves the use of solutions, such as caustic soda (sodium hydroxide) or potassium hydroxide, to effectively remove organic residues, fats, oils and proteins from the surfaces of process equipment and piping. Often, the fluid is heated to maximize cleaning properties of the hydroxide detergent.
Intermediate rinse: Water rinses out remaining alkaline residues.
Acid cleaning: An acid solution is used to dissolve mineral deposits and scale.
Final rinse: A final water rinse
ensures the removal of all cleaning agents and residues.
Sanitization: Sanitizers kill or reduce the number of microorganisms—such as bacteria, yeasts, molds and viruses—that may remain on surfaces after the cleaning step.
Sterilization: Sterilizers are used to eliminate all forms of microbial life, including bacteria, yeasts, molds and viruses, from the surfaces of equipment and pipelines. Sterilization is a more intense process than sanitization and is essential in industries where the highest level of microbial control is required to ensure product safety, especially in pharmaceutical, biotechnology and some food processing applications.
These traditional CIP methods have been effective in maintaining sanitary conditions; however, they come with the requirement of large quantities of chemicals, water and energy consumption, making the process resource-intensive and expensive. Additionally, the effectiveness of the cleaning in removing stubborn residues can be limited.
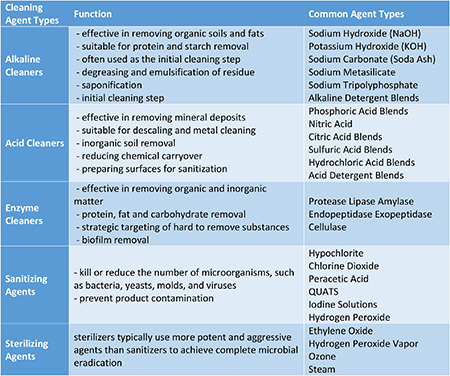
Impulse Cleaning
Impulse cleaning is a 25-year-old patented German technology that finds its origins in the domain of drinking water distribution. Over the last decade, the technology has evolved to cleaning large industrial and sanitary piping systems. As a result of its effectiveness, impulse cleaning has become commonplace in European cleaning standards across a number of market sectors. This process relies on the controlled pulsed injection of compressed air into a throttled water flow, as depicted in Image 2.
Impulse cleaning accelerates water slugs to a maximum flow velocity of 65 feet per second in less than 0.1 seconds. This rapid acceleration results in an extraordinary increase in wall shear stress compared to steady flow methods, as depicted in the chart in Image 3. Impulse cleaning outperforms traditional water flushing by up to 1,000 times the cleaning forces, all while maintaining lower pressures than conventional methods. As a result, impulse cleaning reduces water consumption and wastewater volume. Less volume required means less energy required for tempered cleaning fluid applications, yielding additional savings.
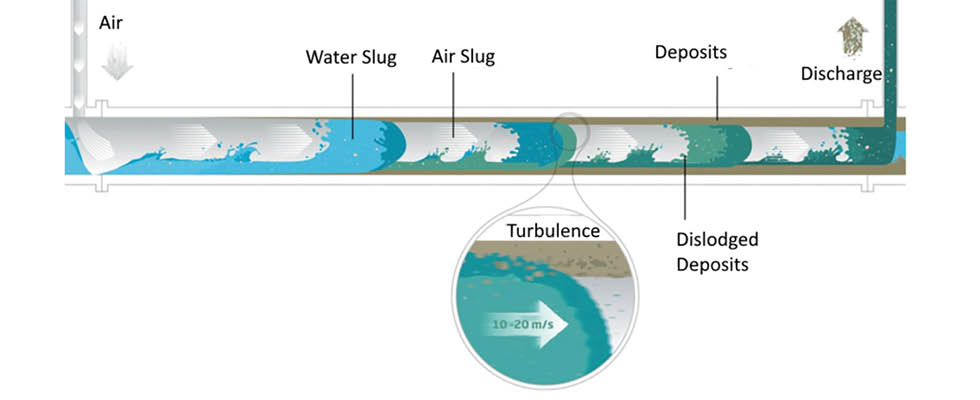
Like traditional flushing, impulse cleaning technology can be affected by obstructions in pipelines. The effectiveness of impulse cleaning relies on acceleration, which requires a minimum open area to enable proper airflow and cleaning fluid flow. This creates a differential pressure, resulting in fluid velocities along the inner surfaces of pipes and components.
It is crucial to assess each inline component in the cleaning path, particularly positive displacement pumps and meters. To overcome potential restrictions, lifting seat relief valves can be utilized where installed.
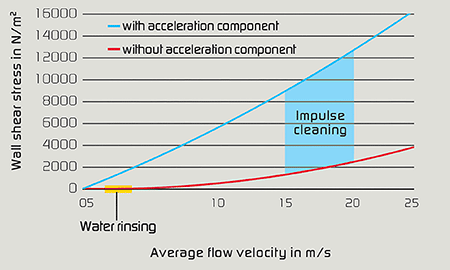
Impulse cleaning distinguishes between two cleaning modes: basic cleaning (curative) and routine cleaning (preventive). During basic cleaning, persistent deposits that have accumulated over time must be eradicated. This type of cleaning is usually scheduled as part of plant shutdowns and may require supplementary upstream chemical cleaning with specialized products to mobilize old, hardened deposits.
Routine cleaning, on the other hand, is a regular part of maintenance aimed at removing product residues that can still be mobilized and have not yet solidified.