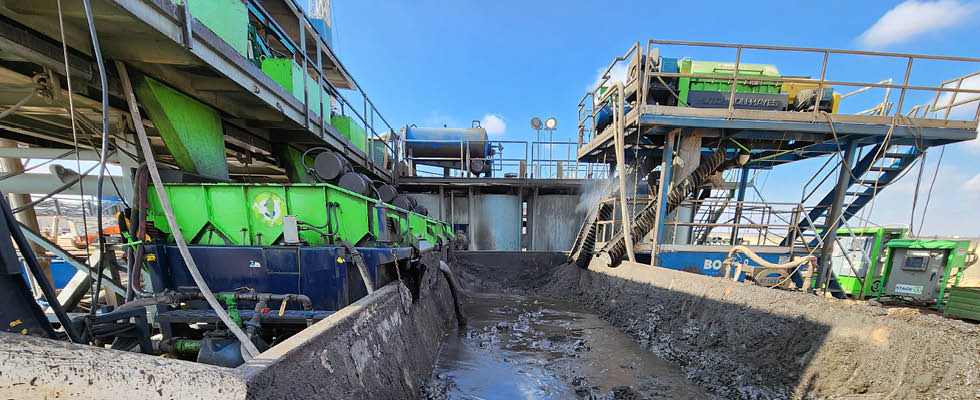
Modern oil rig operations employ various equipment types to handle drilling byproducts, notably drill cuttings—the broken bits of rock and soil brought to the surface during the drilling process. Two commonly utilized machines for this task are excavators and vacuum trucks. While both play crucial roles in managing drill cuttings, technical and operational challenges are associated with their use.
Excavators in Drill Cutting Management
With powerful digging and lifting capabilities, excavators have been
frontline machinery in handling drill cuttings. However, their application is not without problems:
Operational limitations
Handling variability: Drill cuttings can vary immensely in consistency—from wet sludge to dry, coarse fragments. Excavators may not efficiently manage these varying forms due to their standard scoop-and-dump mechanism.
Restricted reach: The operational radius of an excavator is limited by its boom and arm length, potentially restricting access to some areas of the drilling site.
Environmental concerns
Spillage: The excavator’s inherent design can cause some spillage during the movement of cuttings. Given
that some cuttings might contain toxic elements, spillage poses environmental hazards.
Ground damage: The constant movement and weight of the excavator can degrade the ground quality, complicating site restoration and leading to environmental repercussions.
Safety considerations
Equipment hazards: With moving parts like the boom and arm, excavators pose potential safety threats if operators and workers around are not vigilant.
Visibility issues: Excavators have blind spots. In the constrained environment of a drilling site, these blind spots can lead to mishaps.
Economic implications
Operational costs: The upkeep, fueling and maintenance of heavy machinery like excavators can strain operational budgets, especially in remote or inaccessible drilling locations.
Vacuum Trucks in Drilling
Vacuum trucks are another essential asset equipped to suck up and store liquid or semi-liquid drill cuttings. They, too, come with their set of challenges:
Efficiency concerns
Volume restrictions: These trucks have a finite capacity. The constant need to empty them can disrupt operations for large volumes of cuttings.
Dry cutting dilemma: Vacuum trucks best suit slurries or wet materials. Dry cuttings can hinder their efficiency and may even damage the equipment.
Environmental implications
Emissions: Running vacuum trucks, especially older models, generates emissions detrimental to the environment.
Leakage risks: Improperly maintained or damaged trucks might leak, contaminating soil and water.
Safety aspects
Pressure-related mishaps: The core mechanism revolves around creating a vacuum. Equipment malfunctions might result in dangerous pressure buildups or releases.
Exposure to harmful fumes: During suction, harmful gases may be inadvertently inhaled, posing risks to operators if safety protocols are not strictly followed.
Infrastructure and economic issues
Waste treatment needs: Post-collection drill cuttings must be treated or disposed of appropriately, necessitating additional infrastructure.
Fuel consumption: Vacuum trucks, when operated continuously, can
be fuel-intensive, elevating operational costs.
While excavators and vacuum trucks remain pivotal in managing drill cuttings on oil rig sites, it is important to understand their challenges. The objective is to combine their strengths, maintain equipment rigorously and adhere to safety and environmental guidelines to ensure efficient and safe operations.
The Benefits of Pumping Drill Cuttings With the Proper Open-Impeller Slurry Pump
The drilling industry, whether for oil, gas or other exploration purposes, produces a significant volume of drill cuttings. Managing these cuttings is crucial, not only for operational efficiency, but also for environmental compliance. An open-impeller slurry pump is one of the technologies that has proven effective
for this task.
High solids handling capability
The open-impeller slurry pump is known for its ability to handle high solids contents. Traditional centrifugal pumps often face challenges when pumping media with a high percentage of solids. However, due to its design, an open-impeller slurry pump can efficiently transport slurries with high solid contents, making it perfect for handling drill cuttings.
Reduced wear & tear
Drill cuttings can be abrasive. Many pumps suffer from wear and tear when handling abrasive materials. An open-impeller
slurry pump’s unique design reduces the direct impact of these abrasive materials on critical pump components, extending
the pump’s lifespan and reducing maintenance requirements.
Lower maintenance costs
Given its design and the reduced wear and tear, an open-impeller slurry pump generally requires less frequent maintenance than other pumps. This means lower maintenance costs over the pump’s lifespan and reduced downtime, which is crucial for drilling operations where time is money.
Environmental compliance
Environmental regulations around drilling activities are stringent, especially concerning the disposal of drill cuttings. An open-impeller slurry pump allows for efficient cuttings transport to treatment or disposal sites, helping operations comply with environmental standards.
High efficiency & lower energy consumption
Despite its ability to handle high solids contents, an open-impeller slurry pump operates with efficiency. Its design allows for a smoother flow of slurry, reducing energy consumption. This results in cost savings and contributes to a reduced
carbon footprint.
Versatility
An open-impeller slurry pump can be used in various settings and configurations, making it suitable for drilling environments. It can be adapted, whether it is an offshore oil rig or an onshore exploration site.
Safety
Handling drill cuttings can pose safety risks, especially if pumps become clogged or fail. The reliability and efficiency of an open-impeller slurry pump minimizes these risks, ensuring safer operations.