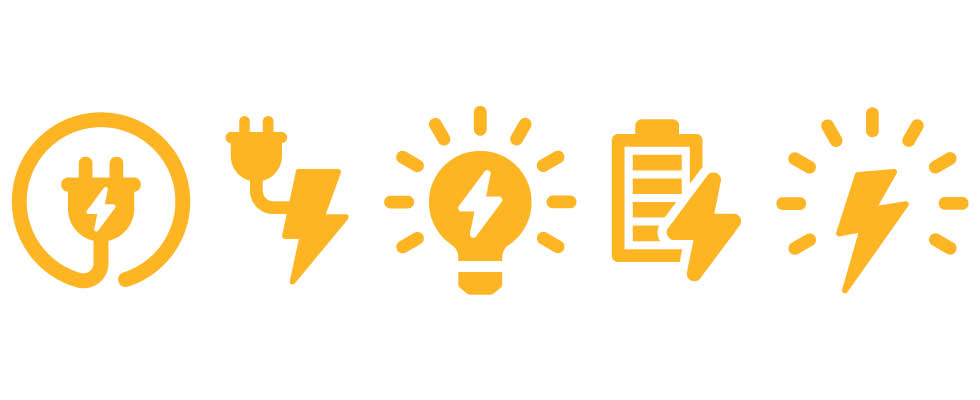
Open-Loop Control
This type of control can be accomplished using either constant speed motor starters (full voltage non-reversing [FVNR], soft starters) or variable frequency drives [VFDs].
For open-loop control, there is no feedback from any instrumentation to turn pumps on, off or control speed. A timer would be set, and the pumps would simply run at a constant or preset speed until the timer expires, shutting off the pumps. Hence the open-control loop (no feedback into the system). Common open-loop control systems would be a toaster or a standard clothes dryer.
Closed-Loop Control
Closed-loop control has many applications, and as the name implies, a feedback signal is generated within the control system that is compared to the desired setpoint of the system to produce a closed-loop control.
The proportional-integral-derivative (PID) controller looks at the error between the desired setpoint and the feedback signal to make decisions on what to do with the pumps. For a booster pump control application, for example, the PID controller is implemented to regulate the booster pump speed in order to maintain a discharge pressure at the discharge pressure setpoint.
When the discharge pressure drops, the proportional (P) part of the PID tells the VFD speed to increase, which begins to diminish the error between the feedback signal from the control system and the desired setpoint control of the discharge pressure for this booster application.
The integral (I) part of the PID control circuit can be thought of as the part that tells the control system how fast to get the feedback signal (the discharge pressure) back to the desired setpoint. The integral of the PID controller is the sum of the instantaneous error over a period of time and gives an accumulated offset that should have been part of the output correction. The accumulated error is then multiplied by the integral gain (Ki) and added to the controller output to improve control.
The derivative (D) part of the control system can be thought of as the part that controls the overshoot of the feedback signal as it tries to match the desired control setpoint. The derivative portion controls the rate of change of the control signal to minimize overshoot.
Tuning the Loop
To make the system operate smoothly, settings for the P, I and D parameters are adjusted, which give the response to changes in the discharge pressure (for the example of the booster control) a smooth recovery to the difference between the desired setpoint and its feedback signal (which changes as the demand changes) to maintain a constant discharge pressure. All PID control must be tuned once installed in the field under real operating conditions.
Incoming Power—Voltage
Voltage is the pressure from an electrical circuit’s power source that pushes charged electrons (commonly referred to as current and expressed in amperes or watts) through a conducting loop, enabling them to do work such as run a motor or power a control cabinet. It is measured in volts.
Most motor and control wiring is powered by 120- to 480-volt circuits. On larger motors and systems, the voltage can be much higher. Users must know the voltage they are working with and take
the proper safety precautions, always wearing the proper personal protective equipment (PPE).
Incoming Power—Circuits
Circuits normally consist of ungrounded conductors from a power source and a grounded conductor (neutral) providing the return path to ground. Electricity will always find the least resistive path to ground. This is called resistance and is measured in ohms. The lower the ohms, the lower the resistance.
Neutral conductors are intentionally grounded at the source and provide the path back to the ground and source. Grounding conductors are a safety net in case the electricity cannot utilize the neutral for this path back to ground. If the neutral is interrupted, the grounding conductor will hopefully pass the electricity back to ground.
This is called a ground-fault condition and is a serious safety hazard. Some circuits are not required by the National Electric Code (NEC) to include grounding conductors; therefore, metal conduits that are effectively grounded act as the grounding conductor.
Single-phase circuits usually consist of one or two ungrounded (hot) phase conductors and a neutral (grounded) conductor. A three-wire circuit (still considered single phase) would consist of two hot conductors (black and red) and a neutral conductor (white). A two-wire circuit consists of a hot conductor (black or red) and a neutral conductor (white). If a grounding conductor (green) is required in either of these circuits, the circuits would still be called two- and three-wire circuits. If the grounding conductor is included, the proper terminology would be a two- or three-wire circuit with ground.
Three-phase circuits normally consist of three ungrounded (hot) phase conductors and a neutral (grounded) conductor, providing the return path to ground. On these circuits, the neutral will also carry the unbalanced load (current in amperes) between the hot conductors.
On a perfectly balanced system, there should be no current running on the neutral. These systems are commonly referred to as a wye system, with a center point ground. Some three-phase systems only have three conductors, and one of the hot conductors is intentionally grounded. These systems are called corner grounded delta systems. They were popular years ago, as users could save the cost of one conductor; however, they have some potential safety problems and are not commonly used today. Many do still exist, so be careful when working on these systems.
The normal color-coding for conductors in a 120- to 208-volt systems is black, red and blue for the ungrounded (hot) phase conductors and white for the grounded (neutral) conductor. If a grounding conductor is used, it is normally green or bare.
The normal color-coding for conductors in 277- to 480-volt systems is brown, orange and yellow for the ungrounded (hot) phase conductors and gray for the grounded (neutral) conductor. Colors for both of these systems should indicate what the voltages are the user is working on; however, always take a voltage tester to confirm the voltage and to ensure the circuit(s) are de-energized when working on them. If a grounding conductor is used, it is normally green or bare.
Ground Current From a Ground Fault
The earth connection (grounding electrode system) is thought of as an almost infinite sink for ground currents. Proper installation of a grounded (neutral) conductor must be taken to ensure the path to ground is a low impedance path, and the current flowing in the neutral conductor finds its way to its source.
The same can be said for the grounding conductor. If the neutral conductor’s path to ground has been interrupted and a fault exists in the equipment, the grounding conductor or metallic conduit will act as
the neutral and carry the current to the ground path.
This is referred to as a ground-fault condition. The amount of voltage and current will determine the amount of destruction this ground-fault condition will create; therefore, it is important to have all PPE worn when working around any energized equipment. Without a grounding conductor to carry the current back to the source, the potential for bodily harm (or even death) increases tremendously. Extreme caution needs to be taken when ground-fault conditions exist.
Ground Current From Lightning
Another type of ground current arises due to lightning. When lightning hits the ground, the ground cannot absorb the huge amount of current, so a large voltage could be present near the source of the lightning strike.
The further a user is away from the strike, the less this voltage potential is. Imagine witnessing a strike close by; the closer the distance to the strike, the larger the voltage potential will be, and the further the distance from the strike, the less the voltage potential will be.
This is why golfers who experience a close lighting strike should shuffle with their feet close to one another instead of enacting a normal walking gait. The voltage potential between their feet is the least possible, as the distance between their feet is kept as small as possible.
Imagine a voltage potential between both legs across the impedance of their body. Therefore, there is low potential and low current flow with the feet close together and higher potential and higher current flow with the feet further apart.
Ground Fault Circuit Interrupters (GFCI)
A GFI outlet is a device used to protect someone from electrical shock or electrocution when an appliance or piece of equipment has developed a current path to ground that should not exist. Imagine a toaster element that has somehow come in contact with the outside/shell of the toaster. When this happens, there is now a potential path for current flow from this unintended path through a person to ground when using the toaster.
A GFI device monitors the current on the supply (hot) conductor that is powering a device, such as a toaster, and compares it to the current returning on the neutral conductor. If there is a difference of more than 5 milliamperes (mA) on the neutral conductor (from the hot conductor), the GFI trips the circuit, removing power to the device. Users will need to reset the GFI device in order to restore power to the device; however, they must determine what caused the GFI to trip in the first place. If the device trips again, the user should unplug or remove the power source to the device until they can correct the problem in the device. Users must not bypass the GFI device or plug this equipment into another non-GFI circuit or they will be putting their life at risk.
Two-Conductor vs. Three-Conductor Extension Cords
Modern appliances using a two-conductor power cord will have the cord double insulated, and the product itself usually has a plastic case. So, there should be no problem using a two-conductor extension cord with a product that has a two-conductor power cord (assuming the cord is rated for the load, and the length of the cord is not excessive).
Using an appliance or tool that has a three-wire power cord with a two-wire extension cord is another matter. People often remove the excess plastic found on a two-wire extension cord meant to block the ground pin. The plastic area is meant to discourage someone from using a two-conductor extension cord with a three-wire corded device.
Will the appliance work? Yes, but in the case of a ground fault, there is no path for the ground current to go, which represents a potentially lethal situation. The ground connector is there to provide a safe path to ground for ground fault current. Also, in the event of a power surge, there is no path to ground for the excessive voltage that could be induced on the power cord, again making it potentially dangerous, if not lethal.
Permanent Magnet Motor & the Squirrel Cage Induction Motor
Both the three-phase permanent magnet motor and the three-phase squirrel cage induction motor have a stator with three separate windings that create a rotating three-phase magnetic field in their stators.
The rotor of the squirrel cage induction motor uses stacked laminations with rotor slots. These slots hold the rotor bars which are moved upon by the rotating magnetic field of the stator and cause the rotor to rotate as a rotating magnetic field is induced upon the rotor. As this magnetic field of the stator is induced into the rotor, the rotor follows the stator’s rotating magnetic field with just a slight difference in speed between the stator and the rotor, which is called slip.
The permanent magnet motor uses a rotor that has permanent magnets embedded within the rotor which create a magnetic force on the rotor, making it ready to go. Because of this, when the stator current is applied, the rotor runs synchronously with the stator current.
For now, the advantage of cost still goes to the squirrel cage induction motor, while efficiency, weight and performance go to the permanent magnet motor.
For this article, resolution will be considered to be the distance within a wet well that is able to be broken down into units of length for use as setpoints for control. For measuring level in a wet well, for example, the resolution would be the fineness of the level data over a given range. The range to be concerned with would be the operating range of the wet well—the distance between the influent piping to the wet well and the bottom of the wet well.
Different methods of measuring the level have different resolution offerings. Float switches may have several feet between their control on/off setpoints. A conductance level probe offers a resolution of 6 inches to 12 inches, as seen by the distance between electrodes.
The resolution of an analog output device (such as a submersible transducer) can provide an output signal that is precise. The theoretical increments of resolution for a device with an analog output are so precise that wet well environmental conditions of flow, turbulence, starts and stops need to be considered to allow for the choosing of control setpoints that are not too close together. For example, “on” at 9.2 feet and “off” at 9.1 feet. While the output of the submersible transducer can provide this accuracy/resolution, the environmental conditions may not allow control settings this close together.
Additionally, resolution comes into play when matching the span of a submersible transducer to the operating range of the wet well. The operating range of a wet well is defined as the distance between the influent pipe and the bottom of the wet well.
When the span of the submersible transducer and the operating range of the wet well match, the entire 4-20 mA output (span) of the submersible transducer can be used for the selection of points of control across the entire range of the operating range, giving users great resolution for this application. This can be visualized with the x-axis being the 4-20 mA output of the submersible transducer, and the y-axis being the length of the operating range.
Sometimes, people want a one-size-fits-all choice, such as using a 15 pounds per square inch (psi) submersible transducer in a wet well with an operating range of 5 psi. When this occurs, a loss of resolution can be seen in the choice of the distance that can be applied to the control setpoints over, as it only has a small portion of the 4-20 mA signal to use for setting of the control setpoints within the 5 psi range.