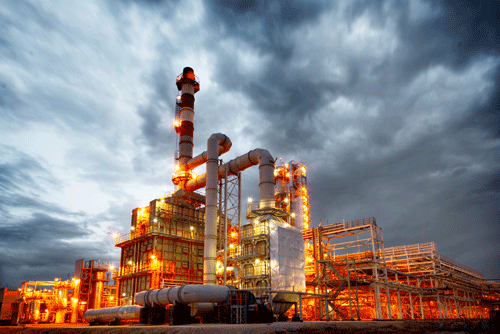
The United States chemical industry is one of the largest in the world, and in the U.S., it is a critical part of the nation’s economy, providing essential products that support various industries and daily life. It encompasses a diverse range of products, including basic chemicals, specialty chemicals, agricultural chemicals, pharmaceuticals, petrochemicals and more.
Compressed air plays a vital role in operations at chemical manufacturing plants. Compressed air is a versatile utility that is used for a range of applications, including conveying materials, controlling processes and ensuring safety. One of the many challenges faced by the chemical industry is the need to meet specific air quality standards.
Why Is Air Quality Important?
Compressed air is used in a variety of processes in the chemical industry, such as mixing, conveying and packaging. The quality of compressed air in the chemical industry is of importance because it can directly impact product quality and the efficiency and reliability of manufacturing processes. Many chemical manufacturing processes in the industry require precise and controlled conditions to produce high-quality products. Contaminated compressed air can introduce impurities or contaminants into chemical products, compromising their quality, purity and consistency. Ensuring clean compressed air helps maintain product integrity.Compressed air exiting the air compressor carries traces of impurities such as dust particles, moisture and oil.
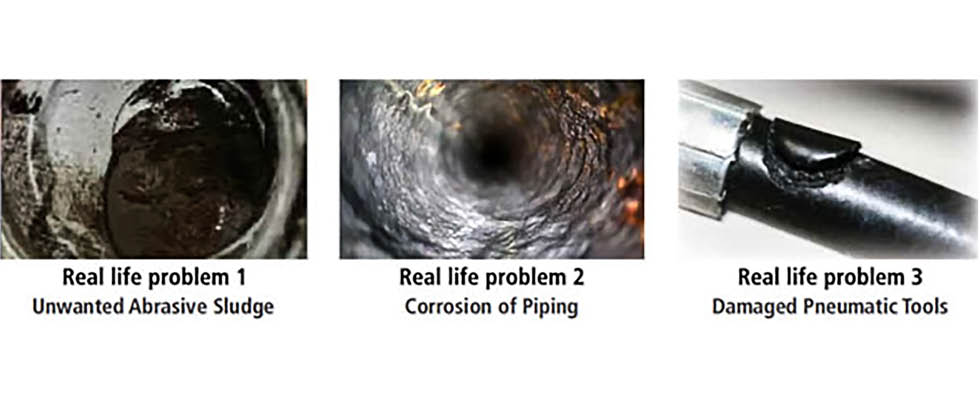
IMAGE 1: Dirt particles, moisture and oil can lead to unwanted abrasive sludge, corrosion of piping and damage to pneumatic tools. (Images courtesy of ELGi)
Dust particles:
The compressed air that emerges from an air compressor often contains dust particles originating from various sources. These sources typically include rust particles from the compressed air piping, the peeling of internal coatings, welding spatter from the piping and aftercooler and the air-oil separator filter media.
Additionally, dust particles can be picked up from moisture traps, wet receiver tanks and the piping system. The quantity of dust present in the compressed air can be influenced by several factors, such as the construction quality and material choices used in the compressor’s internal components, adherence to a proper compressor maintenance schedule, the material selected for the piping and the internal coating of the wet tank.
Moisture:
As compressed air passes through the aftercooler and cools down, any moisture carried within the air undergoes a phase change and transforms into liquid water. While the majority of this water condensate is removed by the moisture separation filters within the compressor, some traces of moisture may still persist in the compressed air. The primary factors affecting the amount of moisture in the compressed air include the relative humidity of the air entering the compressor for compression, the efficiency of the condensate removal system within the compressor and the operational temperature of the air compressor.
Oil:
Oil-lubricated air compressors represent the most prevalent source of compressed air in the market. If operations use an oil lubricated compressor, it can be guaranteed the air contains traces of oil.
Various factors can influence the quantity of oil present in compressed air, including the efficiency of the air-oil separation system, operational temperature and pressure, the duty cycle of the compressor, the proper functioning of the compressor valves and the velocity at which compressed air exits the compressor. Contaminated air can lead to equipment clogging, reduced efficiency and increased downtime, all of which can negatively impact production efficiency, increase operational costs and affect the quality of chemical production.
The air quality required to ensure efficiency and reduce risk of contamination is based on the specific application. Depending on how the compressed air is used, it can be classified into contact or non-contact applications.
In contact applications, compressed air comes into direct contact with the final products that consumers interact with. Non-contact applications, on the other hand, involve the activation of a pneumatic system or device that subsequently interacts with the end products affecting consumers.
The International Standards Organization (ISO) is the world’s largest developer and publisher of international standards. The standard 1508573:2010 is the latest standard most commonly used in the industry to specify the quality of compressed air.
The first part of the standard (1508573-1:2010) specifies purity classes of compressed air with respect to particles, water and oil independent of the location in the compressed air system at which the air is specified or measured. The purity level of each contaminant is shown separately in tabular form, however, for ease of use, Image 2 combines all three contaminants. The quality of compressed air is an essential utility in the chemical industry.
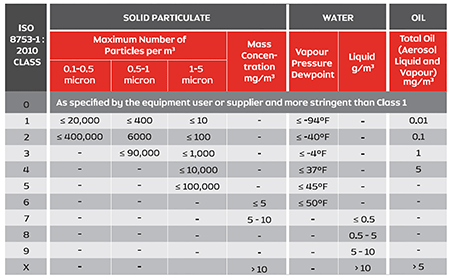
IMAGE 2: Easy-to-use chart that combines particles, water and oil
As an industry that relies on precision and stringent standards, ensuring the purity of compressed air is not a matter of compliance, but a fundamental necessity. The significance of clean compressed air cannot be overstated, as it directly influences product quality, manufacturing efficiency and operational reliability. The challenges of maintaining air quality standards are met with rigorous measures and adherence to international standards, notably ISO 1508573:2010, which serves as a beacon for the industry.