Three trailer-mounted concrete pumps combined to form a single pump station that set the world record for vertical concrete pumping.
07/20/2015
In April 2008, three trailer-mounted pumps reached the current world record for vertical concrete pumping. At the construction site of the Burj Khalifa, the world;s tallest building, concrete was pumped to a record height of 606 meters (m). A strategically designed concrete pumping system made the final conveying height a reality, as the concrete flowed through several stages up the 828-m tower.
The Pump Station
Preparations for the concrete pumping system began in early 2005. Three trailer-mounted concrete pumps were paired with a carefully engineered delivery line system. Four non-ballasted stationary placing booms and several truck-mounted boom pumps were added to support the system.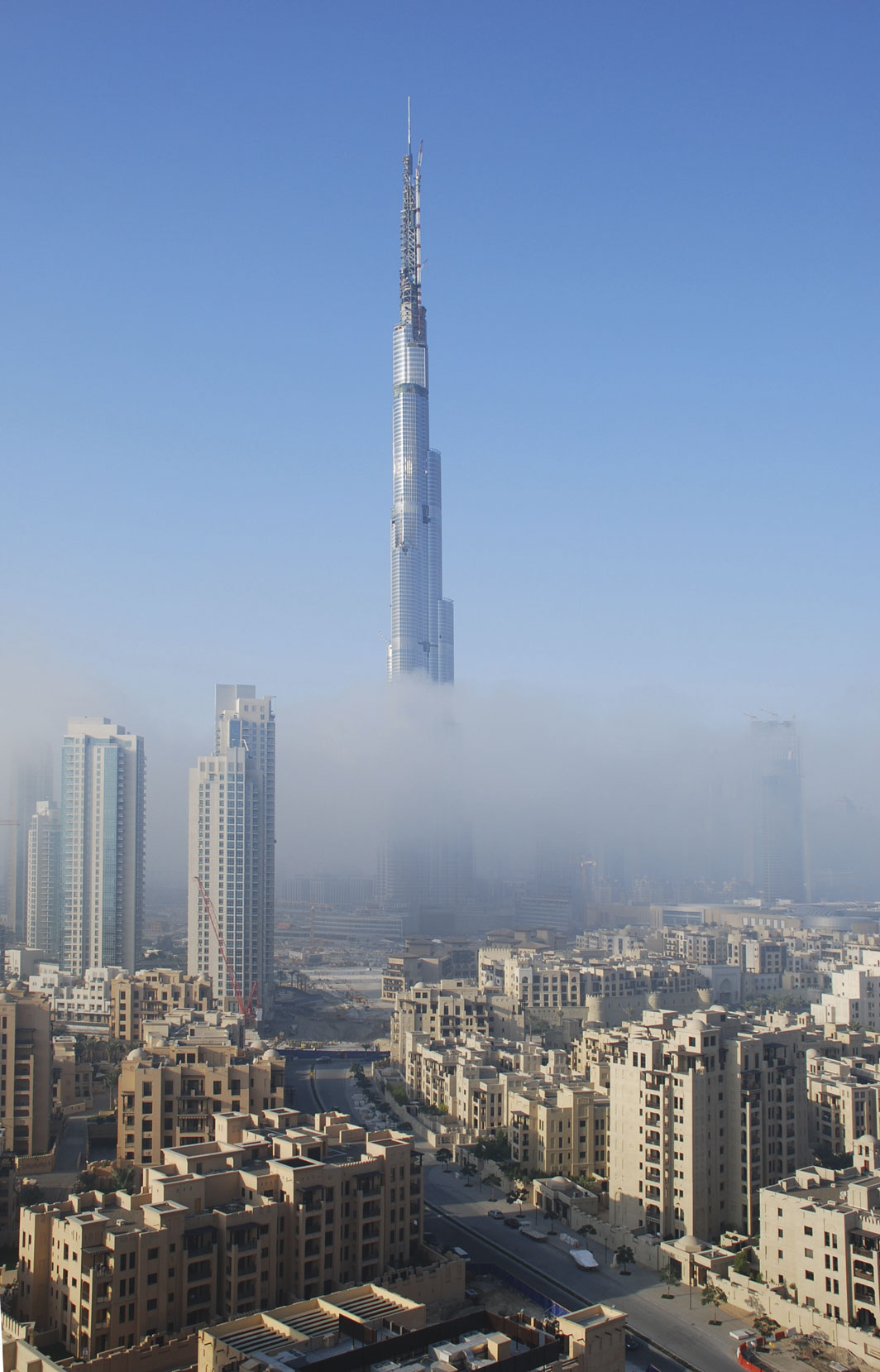
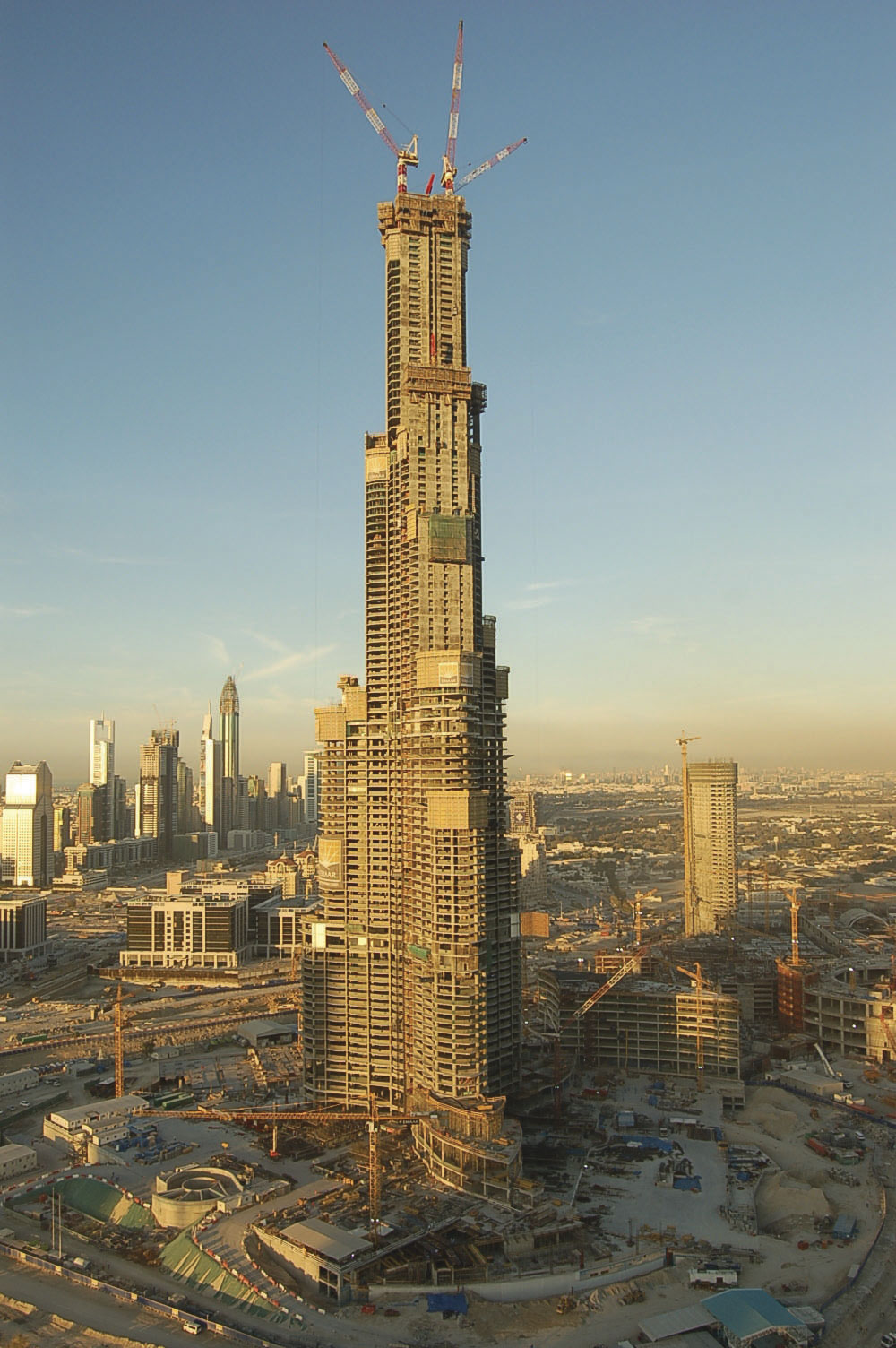
The Concrete Mixture
Throughout the project, operators could only use high-strength concrete mixtures. The mixtures were only poured at night because of hot temperatures during the day. The concrete had to be chilled in the plant before preparation. Some of the water was replaced with ice, allowing the concrete to remain at 28 degrees Celsius as it was transferred to the site. Plant personnel monitored and logged each batch of concrete. Temperature and viscosity were checked regularly before the concrete arrived at the pumps. Then, samples were poured to check pressure. While developing the delivery line system, engineers considered wear behavior, compressive strength and flow path. Truck-mounted boom pumps placed the structure'2s 7,000-square-meter (m2) foundation. Two hundred concrete piles (1.5 m in diameter) support the foundation for the core tower, and 650 piles support the tower's wing sections.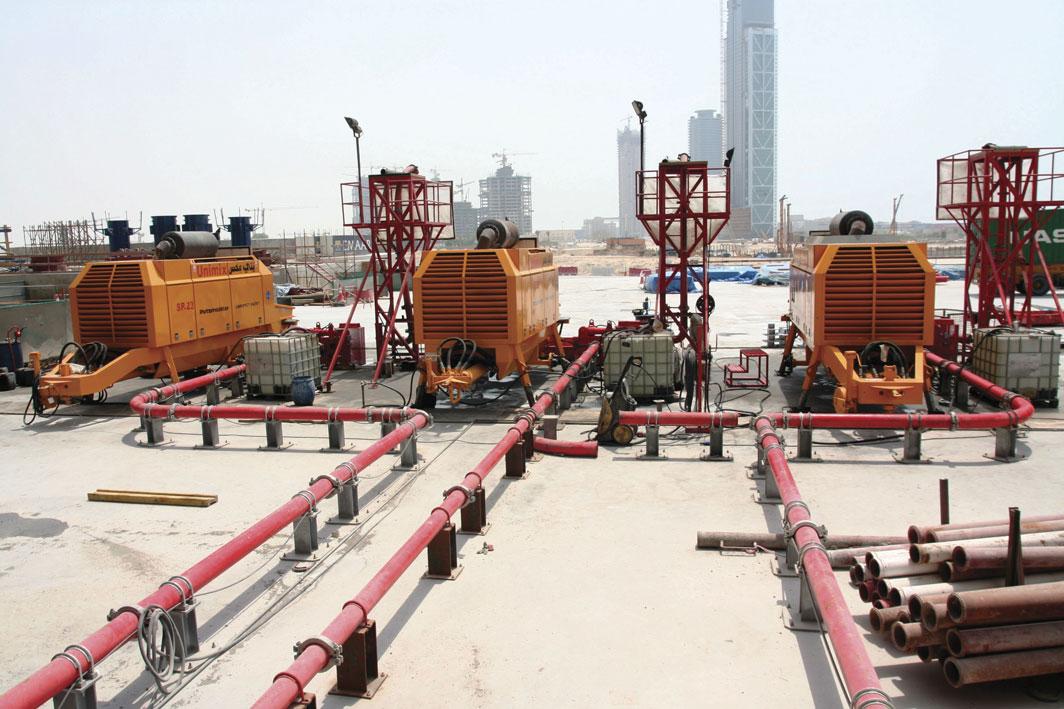