First of two parts
Badger Meter
11/01/2017
There are significant differences between flow meter technologies, with each type of device having its own advantages and disadvantages. With a growing focus on corporate responsibility and sustainability, the monitoring of greenhouse gas (GHG) emissions is critical. Firms must ensure regulatory compliance while protecting assets, personnel and the environment. Another crucial concern is custody transfer, with increasing energy costs driving the need for improved fiscal metering of high-value products.
Common Flow Applications
In modern industrial plants, personnel need to make faster and better decisions by capturing, managing and analyzing data. These facilities rely heavily on flow processes, and thus accurate and reliable measurement technology is vital. Most plants have two flow measurement challenges: accuracy and cost. The goal is to correctly match the right flow meter to the right application to achieve the best performance for the lowest purchase price and total cost of ownership.Popular Measurement Devices
Flow meters are excellent tools to measure, monitor and control the distribution of a host of fluids. The question is which technology to use. Coriolis. Coriolis meters have a vibrating tube in which a fluid flow causes changes in frequency, phase shift or amplitude. The sensor signal is fed into the integrally mounted pc-board. The resulting output signal is strictly proportional to the real mass flow rate, while thermal mass flow meters depend on the physical properties of the fluid. Coriolis flow meters directly measure fluid mass over a wide range of temperatures with a high degree of accuracy. Their unobstructed, open flow design is suitable for viscous, non-conductive fluids that are difficult to measure with other technologies. With no internal moving parts, Coriolis meters require minimum attention once installed. However, they are sometimes considered too sophisticated, expensive or unwieldy (see Image 1).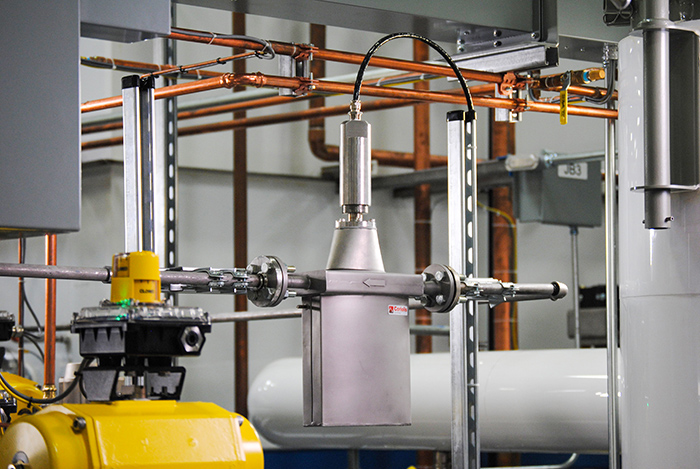
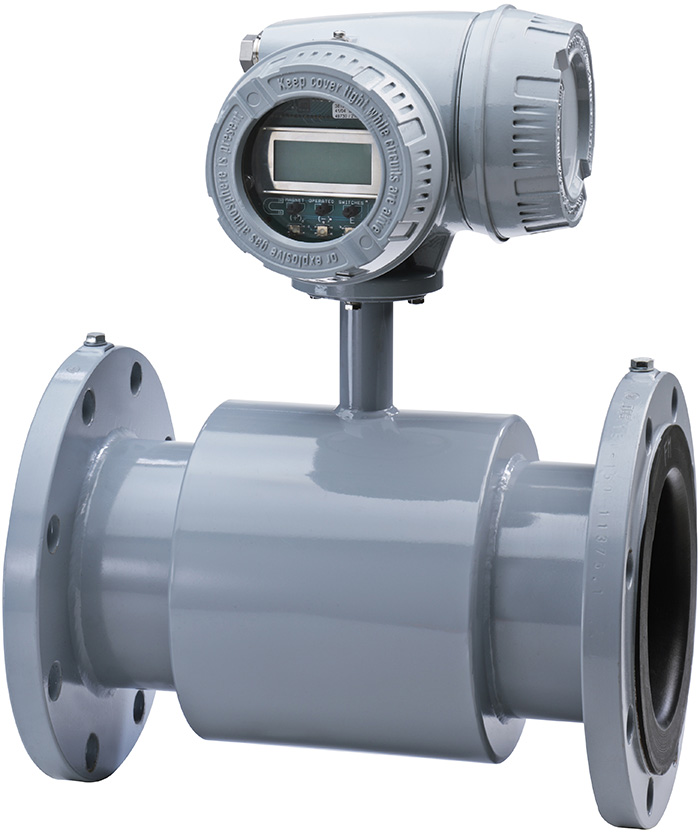
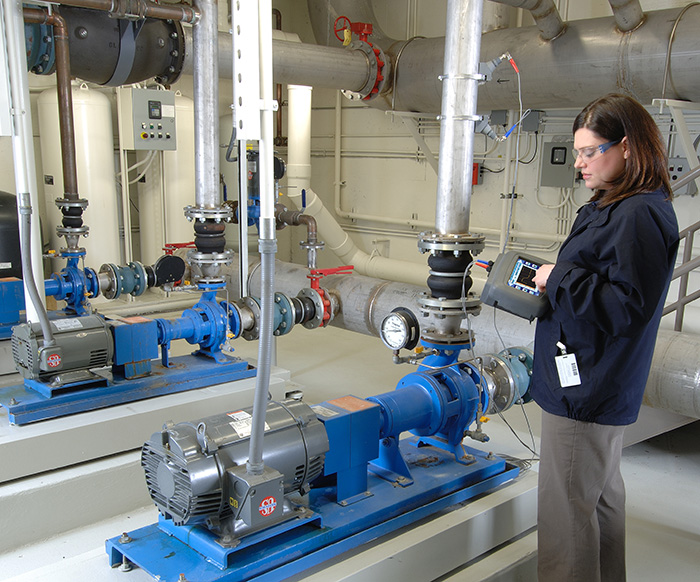
See other Flow Meters articles here.