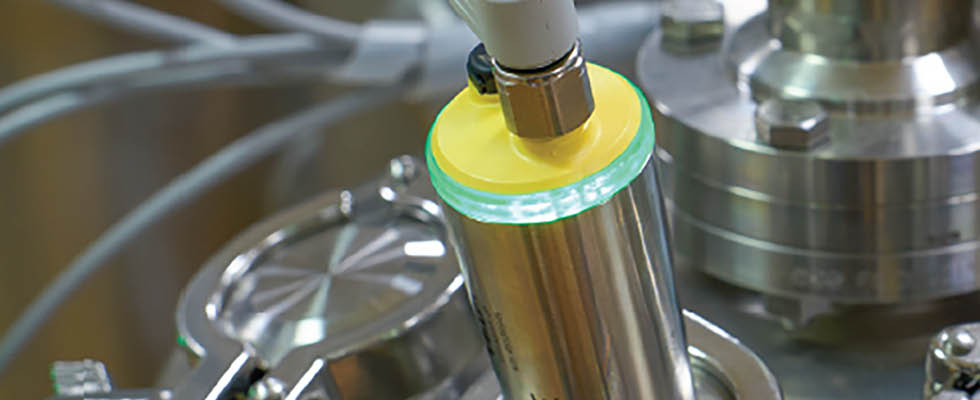
Control switch instrumentation is transforming traditional practices across varied fields, like food and beverage and pulp and paper. With its ability to deliver precision and efficiency to every operation, this technology is reshaping the way these industries function, enhancing productivity and sustainability. Control switches, for instance, intricately regulate pump operations, adjusting flow rates and output in real-time. This level of control not only guarantees consistent product quality, but also minimizes waste and energy consumption. Whether it is bottling sauces, brewing beverages or pulping wood chips, control switches ensure every process meets the desired standards.
Control switch instrumentation takes on many forms, as there are a wide variety of switching technologies that rely on different measuring principles. Some of the most-used switching devices utilize vibration forks, floats, capacitance probes, mechanical paddles or high-frequency radar. Each of these technologies focuses on different physical and chemical properties of the material being measured, and each device has its own strengths and constraints due to those properties.
Floats and vibration switches are particularly suitable for the measurement of non-adhesive fluids. These types of switches have been used for decades and were once a leading technology due to their simplicity and cost. Regardless of fluid conductivity and dielectric constant, floats and vibrating devices can be used as high- and low-level indicators in a variety of industries for pump control or for level limit indication, utilizing such methods as light emitting diode (LED) lights and audible alarms. Float switches, however, can be susceptible to mechanical failures, and their performance might be affected by fluctuations in liquid density. Buildup on any of the components of a float can also have detrimental effects on measurement reliability.
Vibrating switches generally use tuning forks that vibrate at a predefined frequency. In one manufacturer’s vibrating switch, the tuning fork is piezoelectrically energized and vibrates at its mechanical resonance frequency of approximately 1,200 hertz (Hz). The piezos are fixed mechanically and are not subject to temperature shock limitations. The frequency changes when the tuning fork is covered by the medium.
This change is detected by the integrated electronics module, transferred as a current value to the processing system and converted there into a switching command. Vibrating switches are used in such sectors as sauce manufacturing, dairy farming and ice cream production.
The food and beverage industry is filled with products that have high viscosity, adhesive properties and other physical traits that may cause thick buildup on switches. Buildup may cause false switching in vibrating and float-based instrumentation, which may result in hindered production and loss in equipment or materials. In these kinds of applications with a high probability of buildup, capacitance switches demonstrate a more reliable performance.
Capacitance switching for level and point level control is one of the oldest technologies in the instrumentation field. Capacitance is a property that describes how much electric charge can be stored between two conductive surfaces separated by an insulating material, typically referred to as a dielectric. The greater the surface area and the closer the proximity of the conductive surfaces, as well as the lower the dielectric constant of the insulating material, the higher the capacitance. One benefit of capacitance is its ability to handle thick buildup and still reliably register a switching state. This means fewer burned-up pumps or overfill spills.
One limiting factor of most capacitance-based measuring devices is the setup required. Generally, to correctly calibrate a capacitance probe, the device must be shown two operating states: completely full and completely empty. This is not always possible and can sometimes eliminate capacitance as a possible solution.
Some capacitance sensors, however, utilize the technology in a more user-friendly way with a resonance frequency generator. In this configuration, the sensor creates a capacitance field around its tip, and the integrated frequency generator inside the sensor sends out a predefined frequency range. When the sensor detects media, the electronic field changes, which triggers the switch.
There are several other important factors to verify when selecting a switching device for the food and beverage industry, such as which certifications are required and if the tank or vessel has hygienic fittings. Many production facilities require common certifications like the Food and Drug Administration (FDA), the National Sanitation Foundation (NSF) and 3-A on all devices that come in contact with product. Some instrument manufacturers have a long history of working in these industries and offer a wide variety of switches with these certificates readily available, as well as hygienic fittings, so tank modification is not necessary.
Due to the unique measurement challenges posed by aggressive materials commonly used in the pulp and paper industry, operators in this field must carefully consider the type of switch they employ for their needs. Some vibrating switches have special coatings applied to the forks and rods to prevent dust buildup or corrosion from hindering the reliability of the instrument. Another way to prevent damage to the instrumentation is by preventing contact with the measured medium in the first place. Radar technology has long been used for continuous measurement, and it can be used for point level detection as well. By mounting a microwave receiver and detector on opposite sides of a vessel, a break in the microwave signal indicates a switching state. This is a great solution for blockage detection on applications like pulper feed conveyors.
By utilizing the above information and working with the instrumentation manufacturer, operators can select the right solution for their measurement needs.