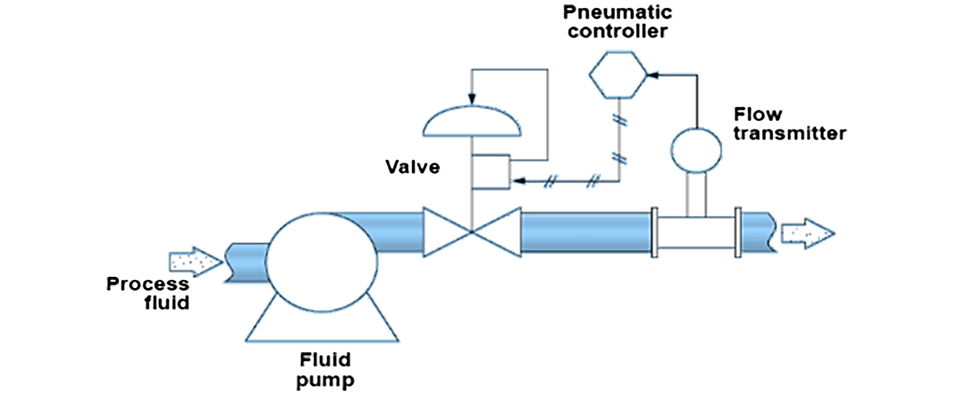
IMAGE 1: An example of a control loop (Images courtesy of Asahi/America, Inc.)
Control valves have a long history of applications going as far back as the bronze age when they were used in aqueducts during Roman times. Control valve developments during the late 18th century included the steam engine. With it, several inventors including James Watt, William Fisher and William B. Mason made advancements in control technology.
How does an engineer decide which type of valve to select? What are the differences among all options? What impact does this selection make on project cost and lifetime cost? How will it affect the control scheme? This article, which discusses some typical control valve considerations, can help the operator decide.
While globe style valves have a longer history in control applications, butterfly valves that are mounted to either pneumatic or electric actuators can provide robust control for decades depending on the application. Ball valves have also been making a strong case for control applications, with design improvements and technology updates over the years creating cost effective options for repeatable flow characteristics.
Diaphragm valves also have a storied history in chemical, slurry, abrasive environments and dosing applications. Engineers have multiple resources to secure a control valve package that offers the performance requirements of demanding applications.
Control Valve Considerations
As processes evolve and increase in complexity so does the need for more advanced process controls, including the control valve. Engineers and operators are constantly looking for solutions that optimize processes toward efficient production, reliable throughput and increased revenue. Engineers must also evaluate the costs of upgrading or automating their operations to ensure their investment will see meaningful returns. Relative to the industries where thermoplastics are often specified and excel, best practices include new technologies, comprehensive control schemes and an increasingly high standard for accurate flow control.
Engineers should ask a few questions when looking at control valve options:
- What is a control valve and what does it do?
- How do I specify a control valve?
- What options or technologies are available?
What is a control valve, and what will it do in the process?
Control valves are used in processes where variables such as flow, pressure or temperature directly impact the end
result. The basic valve design allows the fluid flow to be manipulated by varying or changing the size of the flow passage or vena contracta. The vena contracta is the point in the fluid stream where the diameter of the stream is at its minimum. A valve is designed to adjust this point through the act of moving the closing member. This could be a ball, disc or plug. They are often referred to as the final control element due to their direct physical influence on the process media.
How do I specify a control valve?
There are a number of factors to consider when looking to specify a control valve, but first it is necessary to understand the control loop.
- What variable is being manipulated? (Example: pressure, temperature, level, etc.)
- What measurement is necessary?
- What type of control scheme is being employed? (Example: solenoid, programmable logic controller [PLC], distributed control systems [DCS], etc.)
- What source of energy is being used? (Example: pneumatic, electric, etc.)
An example of a control loop might look similar to Image 1, with a pneumatic controller, pneumatic valve and flow transmitter identified.
It is important to understand the flow requirements of the application and how much flow is needed. As discussed before, varying the vena contracta manipulates the flow. The operator may be interested in sizing a control valve to know how much flow will pass through the valve at any given position as its member is closing and the differential pressure (DP) created during this process.
The relationship between DP and flow rate through a valve is expressed by a flow coefficient (Cv). Cv is defined as the number of gallons per minute (gpm) of flow that will pass through a fully open valve at 60 F with a DP of 1 pound per square inch (psi).
So, a valve with a Cv of 10 would pass 10 gallons of water in one minute with a 1 psi pressure drop. For incompressible fluids like water, Equation 1 would apply. The equation shows that the flow rate varies with the square root of the differential pressure across the control valve. The greater the pressure drop, the higher the flow rate. Pressure drop across a valve is highly influenced by the area, shape, path and roughness of the valve, i.e., its construction or type.
Flow Control Characteristics
When evaluating the type of valve to use in your control loop, it is equally critical to understand the valve’s flow control characteristics. All valves possess an inherent flow characteristic that defines the relationship between the position of the closing member (disc, ball) and the flow rate under pressure. This is a function of the relative position of the closing member to the seat. Examples of different characteristics are shown in Image 4, with various valve technologies providing an array of flow characteristics. Butterfly and full port ball valves, for example, are considered high recovery valves in that the effective rate of control between a certain percentage open and fully open is relatively small. A globe valve possesses near-linear characteristics, giving a steady, reliable and repeatable control across its travel.
Valve technologies and their flow control characteristics
Aspects such as control scheme and actuation technology can impact both the process and investment decision. One common scheme is a PLC with a 4-20 milliamp (mA) positioner and feedback control loop. Other options include manual loops, where an operator adjusts the valve based on downstream information, solenoid valves operating on a voltage change or DCS with advanced programming and communication protocols. There are also considerations relative to the valve actuation. Is the current system controlled with pneumatic or electric actuation? What type of positioner is required? Finding a control valve that meets the needs of both the process and the control scheme is critical to success.
What options are available?
While butterfly valves, ball valves, globe valves and diaphragm valves have been available and in control applications for years, recent improvements to valve and actuation technologies relative to thermoplastics have led to increased capability and agility toward flow control. Advancements in actuators, controls and overall design have increased reliability, giving engineers and operators more flexibility and choices in their application process. An example of such
an improvement is the v-port ball valve.
In many cases, these valves are designed with all the reliability and agility of a standard ball valve; however, they can include features that deliver a modified equal percentage flow characteristic, providing excellent flow control across the span of travel. There are also benefits to the use of these valves as they can deliver these features at a cost-effective price point, with serviceability more attractive when compared to other valve options.
When paired with the appropriate electric actuator, these packages provide reliable and repeatable flow control with high setpoint accuracy, position feedback and failsafe capabilities.
Engineers are looking for technologies and equipment that serve the fundamental purpose of process control in their facilities as well as suppliers who can maximize productivity and solve problems that contribute to lost uptime and profitability. Whether a loop needs a simple butterfly valve with a lever operator, an automated ball valve package with a pneumatic positioner or a specialized diaphragm valve, engineers can leverage manufacturer engineering and expertise for any application.