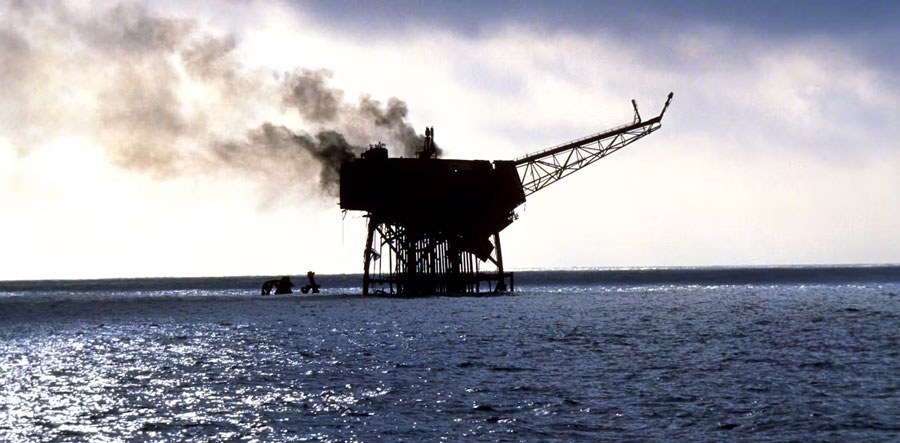
Late in the evening of July 6, 1988, the Piper Alpha offshore platform in the North Sea was devastated by a series of catastrophic explosions. The disaster, which remains the world’s deadliest offshore oil accident, resulted in the deaths of 167 workers, extensive injuries and an estimated $5 billion in losses. The root cause? A simple but critical failure in communication and procedural adherence—a missing pressure relief valve and an improperly secured blind flange on a condensate pump.
This tragedy highlights the devastating consequences of breakdowns in communication during maintenance operations. The failure of a single flange in a high-pressure system ignited a chain reaction that ultimately destroyed the platform. This article will explore the importance of proper gasket installation, tag-out procedures and maintenance communication in industrial operations, ensuring such incidents are avoided in the future.
On July 6, 1988, maintenance work was underway on Condensate Pump A on Piper Alpha. As part of this maintenance, its pressure relief valve was removed, and a blind flange was installed in its place. However, this flange was not properly secured, leak-tested or pressure-tested. Due to the way the work permit system was structured, operators were unaware that this critical pressure relief valve was missing. Later that evening, Pump B suddenly failed. In a routine attempt to restore operations, the crew restarted Pump A—completely unaware that it lacked the necessary pressure relief valve. This small oversight led to high-pressure condensate escaping from the improperly tightened blind flange, resulting in a massive explosion. The subsequent rupture of oil and gas lines led to a rapid, uncontrollable fire, which escalated into a disaster that wiped out the platform’s entire topside. The root cause is a failure in proper gasket installation and communication between maintenance and operations teams.
While Piper Alpha’s failure involved multiple factors, the improper installation of a blind flange played a significant role. This underscores the critical nature of proper gasket and flange sealing procedures, which, if not followed, can lead to disastrous consequences.
Gaskets are essential components in industrial piping systems, designed to create a reliable seal between two flanges under extreme pressure and temperature conditions. The effectiveness of a gasket depends on multiple factors, including material selection, proper installation and adherence to torque specifications. Failure to consider these elements can lead to leaks, pressure loss or catastrophic failures.
Proper gasket selection is the first step in ensuring safe operations. Gaskets must be rated for the system’s pressure, temperature and chemical exposure. Selecting the wrong gasket can result in rapid degradation and unexpected failure. Ensuring that flanges are correctly aligned and free from debris is equally important. Any imperfections on the sealing surface can compromise the gasket’s integrity, leading to potential leaks.
Once a gasket is selected and placed, the tightening process is crucial. Flanges should be tightened incrementally using a cross-pattern method to apply even pressure, preventing warping or uneven compression. Torque values must be followed according to manufacturer recommendations. If bolts are overtightened, the gasket material may become excessively compressed, reducing its ability to seal properly. If undertightened, gaps may remain, allowing pressure to escape.
Leak and pressure testing are essential steps that should never be skipped. Every newly installed gasket or blind flange should be tested under real operating conditions before the system is restarted. Pressure testing following industry standards, such as American Petroleum Institute (API) 598 or American Society of Mechanical Engineers (ASME) B16.5, ensures the gasket is performing as expected and can withstand operational stresses. The failure to conduct such testing, as seen in Piper Alpha, can lead to tragic consequences.
Additionally, environmental and temperature conditions play a significant role in gasket longevity. In high-temperature applications, thermal cycling can cause expansion and contraction, leading to seal degradation over time. Vibrations from pumps and compressors can also impact gasket integrity. Maintenance teams should proactively replace gaskets before they reach the end of their life cycle rather than waiting for signs of failure.
One of the most crucial failures in the Piper Alpha disaster was a breakdown in communication between maintenance and operations teams. The missing pressure relief valve was part of an entirely separate maintenance job, yet this information was not properly relayed to the operators who attempted to restart the pump.
The permit-to-work (PTW) system is designed to prevent such incidents by ensuring clear documentation and coordination between different teams. Every maintenance job should be logged in a PTW system, detailing which equipment is out of service, which components have been removed and any temporary modifications such as blind flanges. In Piper Alpha, the operators were unaware that Pump A was missing a critical component because the PTW system did not effectively communicate this information.
In addition to PTW, lockout-tagout (LOTO) procedures should be rigorously enforced. LOTO ensures that equipment undergoing maintenance is physically locked out to prevent accidental operation. It also includes visual tags that state what has been removed or modified. Had a LOTO procedure been properly executed on Piper Alpha, the crew would have been unable to restart Pump A, preventing the explosion.
Before any equipment is brought back online, a verification process should be conducted to ensure all components are correctly installed. Cross-team communication is vital in this step. Utilizing digital permit tracking systems or visual checklists can provide additional safeguards to prevent premature equipment activation.
The Fluid Sealing Association’s Gasket Installation Manual provides a comprehensive guide on selecting, installing and maintaining gaskets to ensure safety and performance. The manual emphasizes proper material selection, flange surface preparation and torquing procedures—key factors that can prevent failures like those seen in the Piper Alpha disaster.
The Fluid Sealing Association also advocates for ongoing training and certification for maintenance personnel working with gaskets and sealing systems. Many industrial failures result from human error due to a lack of knowledge on proper gasket handling and installation. By implementing Fluid Sealing Association-recommended training programs, organizations can significantly reduce the risk of gasket-related incidents.
Companies should integrate Fluid Sealing Association guidelines into their maintenance protocols, ensuring every gasket installation follows best practices. This includes routine inspections, standardized testing and proper documentation to track gasket performance over time.
The lesson from Piper Alpha and other industrial accidents is clear: Small oversights in gasket installation and communication can lead to catastrophic consequences. Organizations must instill a culture of safety, ensuring every gasket is installed correctly, pressure-tested before use and documented in PTW and LOTO systems. Operators should never assume a system is safe without verifying its status first.
By enforcing strict installation procedures, improving communication and utilizing industry best practices from organizations like the Fluid Sealing Association, we can prevent gasket-related failures and ensure that disasters like Piper Alpha never happen again.
We invite your suggestions for article topics as well as questions on sealing issues so we can better respond to the needs of the industry. Please direct your suggestions and questions to sealingsensequestions@fluidsealing.com.