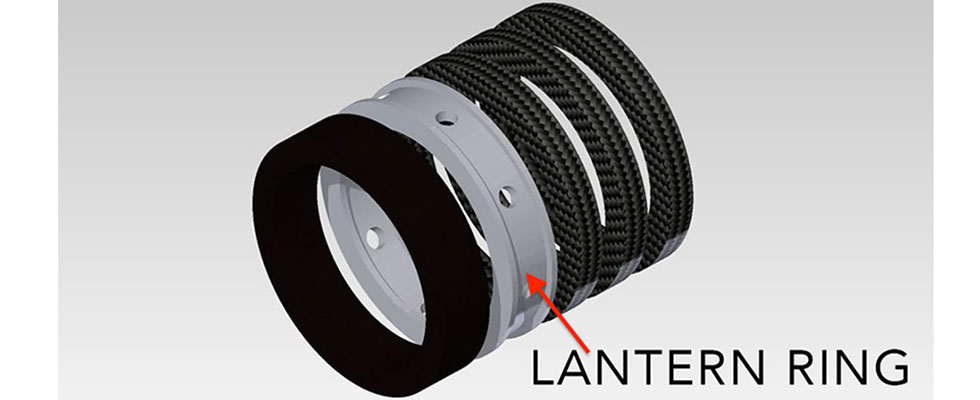
In the Tony-Award-winning musical Hamilton, one of the most impactful scenes is when Aaron Burr laments that he never gets to be “in the room where it (decision-making) happens.” What goes on in that room full of leaders is so great, and he yearns to be there. Of course, he blames Hamilton for keeping him out.
Do you ever wish you could see inside the stuffing box, which is the space where most of the activity happens within a pump? Sure, the intake, impeller and casing get a lot of attention. However, the fluid containment, shaft movement, shaft sealing and motor connection (as well as potential contamination points—lubrication into the process fluid/process fluid into the lubrication) all occur within this small but important space.
The stuffing box is where it all happens and also ripe with potential failure possibilities. So, how do we protect this notorious leakage path and increase stuffing box, and ultimately pump, reliability? While packing selection and proper installation are key, install the lantern ring incorrectly or allow it to be blocked, and failure is imminent.
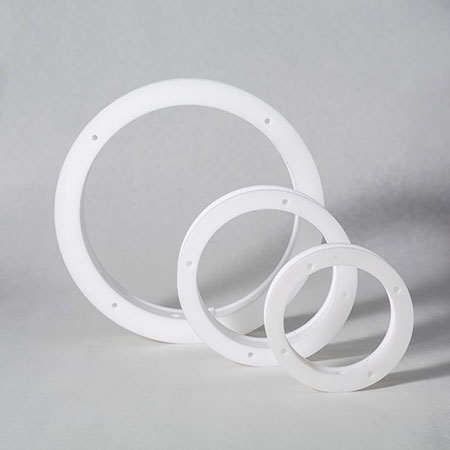
What Are Lantern Rings & What Is Their Purpose?
Perforated lantern rings are usually in the center of every packing set in a centrifugal pump. They are simple components, but get something wrong when selecting, installing or operating them, and big problems may occur in the stuffing box. A lantern ring is placed between packing rings in each packing set and extends the life of the packing, stuffing box and shaft. Ultimately, lantern rings increase the life span of the pump system.
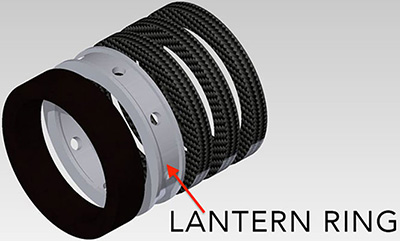
Lantern rings serve three purposes: protection, cooling and lubrication. They protect the stuffing box and the installed packing by providing an access point for flush water. If process fluids or other contaminants enter the stuffing box and are not removed by flush water, several problems occur, including:
- damaged or destroyed packing
- shaft or sleeve damage
- stuffing box wear
A lantern ring also gives the stuffing box an outlet to assist with cooling. It allows the system to avoid being completely closed off and assists in mitigating overheating.
The final lantern ring purpose is lubrication. Packing causes friction along the shaft and stuffing box walls or casing. Fluid entering through the lantern ring lubricates the packing. The liquid reduces friction, limits the wear of the machine’s parts and decreases heat within the system.
What Materials Are Ideal for Lantern Rings?
While lantern rings are humble components of a pump system, selecting a high-quality ring will extend the life of the rings and the system. With the heat generated in a stuffing box, low-quality plastic or the wrong plastic for the pumped fluid will cause problems. The material may soften or melt over time. If this happens, the lantern ring will no longer serve its purpose of protection, cooling and lubrication.
To make the right material selection, several factors should be considered:
- Is the system water-tight or air-tight?
- What flush media will be used?
- What is the system pressure?
- Does the system need flexibility?
- Does the process fluid contain abrasive or hard-wearing particles?
- What is the chemical makeup of the fluid touching the lantern ring?
- Are there hygienic concerns?
- What is the system temperature during operation?
- What is the ease of maintenance?
- Does the plant have financial limitations?
PTFE & PEEK Strengths & Weaknesses
Selecting the ideal material for the application is critical. Lantern ring selection should be given equal consideration because they are equally as important as packing. Below are some strengths and weaknesses of PTFE and PEEK.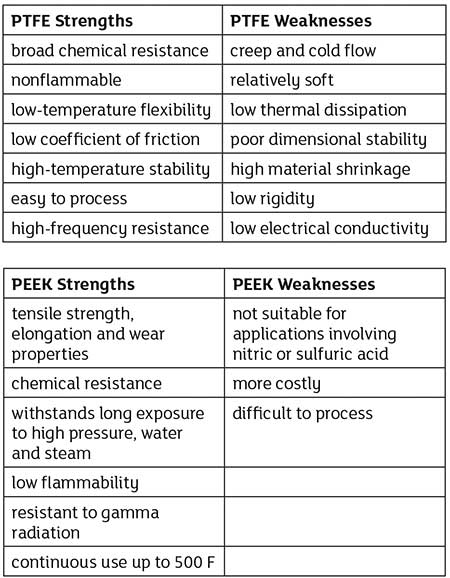
Looking back historically, lantern rings have been constructed of many different materials, including brass, other metals and low-quality plastics. The ideal materials are primarily polytetrafluoroethylene (PTFE) or polyether ether ketone (PEEK).
PTFE is a standard material for lantern rings. It can withstand a wide temperature range (-300 F to 500 F), which few other materials handle well. PTFE is compliant with United States Food and Drug Administration regulations and has broad chemical resistance.
While PTFE is the standard choice for temperatures up to 400 F, some processes exceed 400 F in the stuffing box. In these applications, PEEK is a better material choice for temperatures of 400 F to 500 F. It is a good choice and performs well, but it is more costly. See the sidebar above for the benefits and weaknesses of PTFE and PEEK. If temperatures exceed 500 F, bronze or an alloy should be used.
Since nearly 95 percent of industrial applications use PTFE, the next decision will be whether to use standard machined PTFE lantern rings or flexible lantern rings. If a plant has shafts with the same specifications or just a few different sizes, machined, standard rings may be the right selection (Image 3, left). However, if many different size pumps and shafts are involved, flexible virgin PTFE lantern rings may be a better choice (Image 3, right). With this material, end users may measure and cut lantern rings to fit the shaft they are working on.
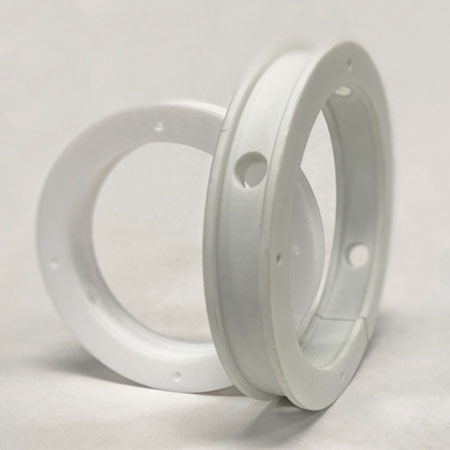
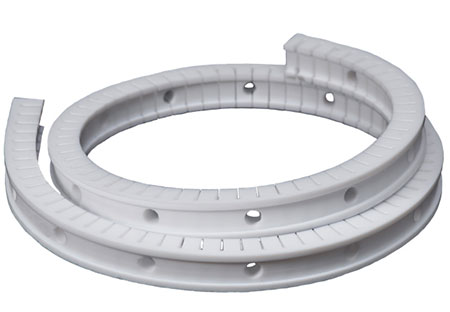
How Is a Lantern Ring Installed?
Most packing sets have five packing rings. The lantern ring can be inserted after the second or third packing ring is installed. This all depends on where the flush port of the stuffing box is located. To ensure that the lantern ring is installed correctly, insert a small object through the flush port and feel the lantern ring.
Once this is done and all the packing rings and packing follower are installed, end users should install the proper flush setup and start flushing the stuffing box. For many reasons, starting the flush before operating the pump is important. One reason is to ensure that flush water is moving through the lantern ring and into the stuffing box correctly.
Care must be taken to ensure the lantern ring’s fit around the shaft is correct. Most lantern rings have a larger fit on the inside diameter and a tighter fit on the outside diameter, so frictional heat is not an issue.
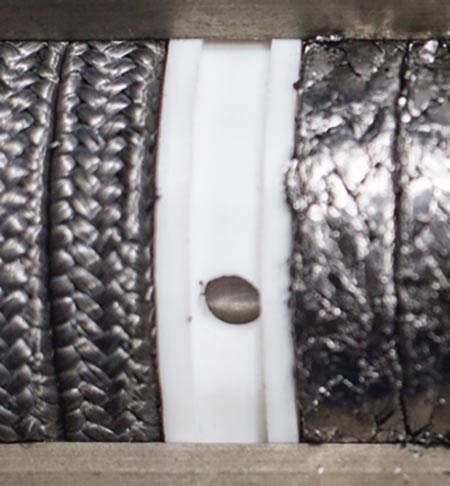
What Can Go Wrong?
A few problems can occur with lantern rings. The first is incorrect installation, which may result in improper flushing and lubrication. This will cause the packing to potentially overheat or be damaged by particulates in the process fluid. Without lubrication, the stuffing box and shaft may be damaged. Ensuring proper flushing and cooling are critical when installing the lantern ring and lining it up with the flush port.
If the fluid is high in solids and particulates, the lantern ring holes may also become clogged (Image 5). This will prevent flush fluid from entering the stuffing box, again causing wear and damage to the packing, shaft/sleeve or stuffing box walls.
In some applications, the lantern ring may be connected to the bushing and installed in the stuffing box as one unit. While this may help in stabilizing a deflecting shaft, other problems may arise. In particular, removing the lantern ring if it becomes clogged becomes more problematic and costly. Two system components must be replaced (the bushing and lantern ring) even though the bushing may be undamaged.
Another potential problem with this hybrid configuration is that the component may become lodged within the pump and be much more difficult to remove. In one hydrapulper application at a Southeast paper mill, a team needed to unpack and repack the hydrapulper. Removing the bushing-lantern-ring component took nearly 15 hours because it was full of stock and had become stuck on the shaft. In most situations, a separate lantern ring and bushing is recommended.
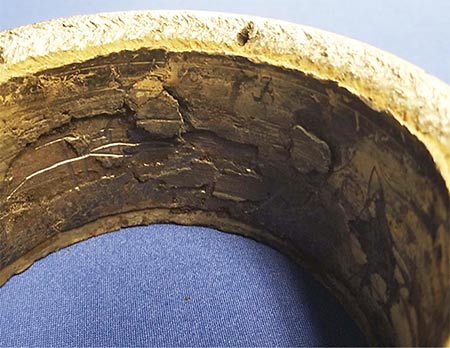
Why Should Lantern Rings Not Be Overlooked?
Ignoring the importance of lantern rings can be easy. They are small and may seem to be an inconsequential, consumable component. However, end users who regularly examine lantern rings for correct type, installation and clogging see longer packing life, fewer shutdowns for packing replacement, and less shaft wear and damage. This does not get anyone in the “space” where it happens, but correct lantern ring selection, operation and maintenance helps ensure stuffing box reliability, even when you cannot see inside. If only Aaron Burr could have had this perspective (and not been so jealous), the United States may not have lost Alexander Hamilton so soon.
We invite your suggestions for article topics as well as questions on sealing issues so we can better respond to the needs of the industry. Please direct your suggestions and questions to sealingsensequestions@fluidsealing.com.