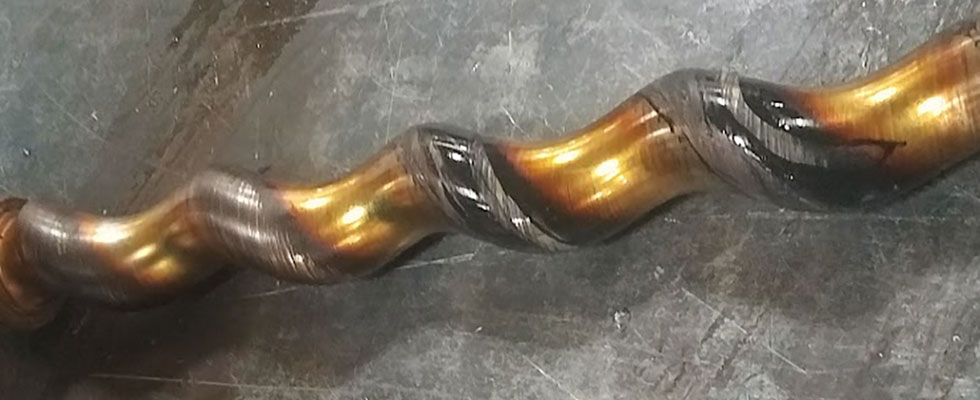
Manufacturing facilities have come a long way in measuring and archiving historical process data. Despite robust data collection, many facilities are failing to fully use this information in maintenance. From identifying trends to predicting failures, the benefits of properly integrating data into a pump reliability program is crucial. For this reason, it is important to understand the critical variables that contribute to pump failure and the potential pitfalls that may prevent an organization from profiting from existing data-based systems.
Traditional maintenance methods rely mostly on mechanical techniques to identify the root cause of failure and prescribe what is required for equipment overhaul. Robust data systems have been integrated into manufacturing systems and are used for optimizing production rates, ingredient additions and machine settings. To a lesser degree, some maintenance programs have capitalized on data-driven programs. It is hard to say why modern pump maintenance procedures have been slow to catch on.
That said, the industry has recognized the gap, and data-based maintenance has been a hot topic. It can be overwhelming with all the broadly defined methodologies and analytic systems, so it is important to look past the acronyms and understand the physics behind pump failures. Accurate measurement of pressure, temperature and flow, combined with a knowledge of “where, when and what,” are essential in understanding upset conditions and process design issues. By monitoring these parameters and identifying issues before they lead to failure, it is possible to prevent downtime and prolong the equipment life span.
Pressure is a fundamental parameter in many processes, and variations can indicate a problem. However, it is just as critical to understand where each pressure variable is measured. Pressure measurements are typically taken at various points, such as the suction and discharge side, as well as at the inlet and system outlet. The pressure measurements at the suction and discharge side of the pump provide information about pump performance, such as the flow rate, total head and efficiency. The measurements at the inlet and outlet of the system provide information about the system.

Pump flow rate is another critical parameter in predicting, solving and troubleshooting pump reliability issues. A great example is measuring flow rate per rotations per minute (rpm). When a pump is installed, the flow rate at a given rpm is at its maximum value. As internal components wear, the flow rate per rpm decreases. Understanding the limitations of the pump and system speed can allow for a predictive maintenance schedule.
Flow rate is also an effective tool in diagnosing centrifugal pump issues. When there is a deviation from a performance curve, it can indicate a suction issue or a permanent mechanical failure. For instance, if the discharge pressure is low and the flow is below its expected flow rate, then it can be an indication that something is wrong with the suction or that the impeller or volute is damaged. Knowing that a flow rate is too low for the given pressure should be an immediate red flag.
Another essential variable is temperature. Temperature is useful for mechanical and process driven failures. Examples of mechanical temperature indicators are:
- Temperature of a bearing will increase as it is nearing the end of its life.
- When a mechanical seal is operated without fluid, a dramatic stuffing box temperature increase proceeded by seal failure is an indication that more system interlocks are required.
- If a downstream valve is closed on a centrifugal pump causing the pump to deadhead, there will be heat in the volute that will continue to increase because of friction and the inability of moving fluid to take away that heat.
When it comes to mechanical temperature analysis, the bottom line is friction creates heat and is the main limiting factor of many mechanical systems. It is important to understand and measure mechanical temperatures where possible.
Temperatures can also explain issues in process systems. For instance:
- Cavitation creates heat that would cause the temperature to increase
- Contamination of chemicals could cause an exothermic or endothermic reaction increasing or decreasing temperature.
- An improperly sized valve could create a choke flow causing phase change resulting in a temperature increase.
WHERE: Location where data is being measured dictates how the data needs to be interpreted. If a pressure sensor is located upstream of a modulating valve, closest to the discharge of a centrifugal pump, then the pressure value would be inversely proportional to flow rate (higher pressure = lower flow). If the pressure measurement is downstream of a modulating valve and all other variables are held constant, then the pressure would become directly proportional. The point is that the location of the same type of variable can display opposite or noncorrelatable results depending on where the information is measured.
WHEN: Time correlation is a prerequisite to pinpoint when measuring upset conditions. This may seem obvious but can become more nuanced when considering frequency of data collection, compensating for lags in process control or linking cause and effect.
WHAT: Understanding the process fluid properties is paramount in understanding application limitations. A great example is understanding the vapor pressure of a fluid to identify the temperature, pressure and flow limits required to avoid cavitation. Imagine a brewery decides to launch a product with a higher concentration of ethanol. Higher ethanol levels can lead to cavitation at lower temperatures and higher pressures; therefore, new limits must be established to prevent failure.
The pump type in each location is also critical. Revisit the example regarding where the pressure is measured. If the same condition is true for a positive displacement pump with 100% volumetric displacement, the pressure upstream or downstream of the throttle valve would not affect flow. However, power would continue to increase as pressure upstream of the throttle valve increased. Power would be inversely affected on the positive displacement pump, as it would continue to increase until an equipment limit is reached. Conversely, a centrifugal pump would experience a lower power draw as pressure increased.
Secondary variables such as viscosity, pH, conductivity, suspended solids, consistency, particle size and lubricity are often overlooked but are valuable in diagnosing and solving equipment reliability issues. These variables provide a more subjective understanding of the process and can give insight into the root cause of equipment failures.
Conductivity, suspended solids, dissolved solids, particle size and lubricity are also valuable. Conductivity, for instance, is a measure of how well a liquid conducts electricity and can be used to detect impurities in the liquid. Suspended solids, dissolved solids and particle size are all indicators of the liquid’s condition and can be used to detect contaminants. Lubricity is an important parameter in lubrication systems and process lubricated mechanical components.
Vibration analysis is another powerful tool used for diagnosing issues. By measuring the vibration at various locations of a pump, it is possible to detect problems such as an unbalanced rotor, misaligned shafts, worn bearings and more. By identifying problems early, vibration analysis can help prevent downtime and prolong the life span of the pump. In addition to identifying specific problems, vibration analysis can also be used to monitor the health of the pump over time. By comparing vibration data from regular intervals, it is possible to detect changes in the pump’s vibration levels that may indicate an impending failure. Vibration analysis is a noninvasive and cost-effective method for diagnosing pump issues. Vibration analysis can help ensure pumps are running at optimal performance.
Pump maintenance programs can be greatly improved by using process data in combination with sound mechanical techniques. By leveraging process data to predict equipment failures and optimize maintenance schedules, facilities can build a next-level maintenance program.