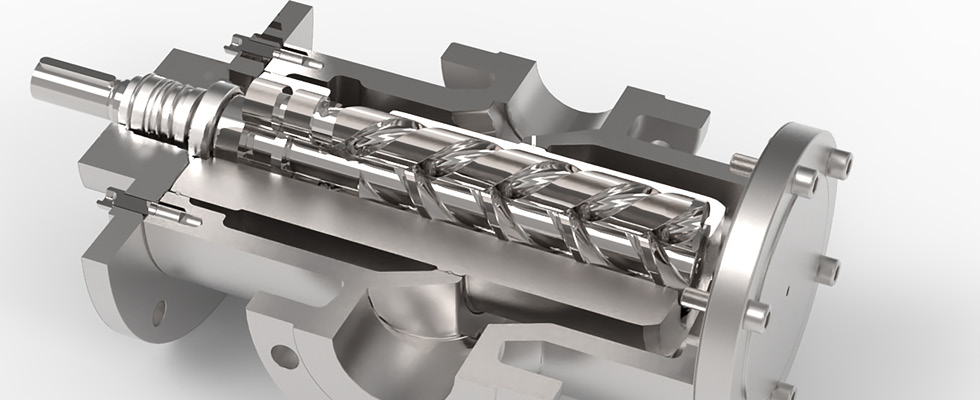
In the first part of this discussion, we examined the fundamental differences between positive displacement (PD) pumps and their rotodynamic counterparts. We established that PD pumps excel in applications requiring precision, reliability and adaptability, making them indispensable in industries such as oil and gas, food and beverage, pharmaceuticals and wastewater treatment. Unlike rotodynamic pumps, which rely on velocity to generate pressure, PD pumps operate by displacing a fixed volume of fluid. Please note that PD pumps do not generate pressure but move fluids from their inlet ports to their discharge ports. As the fluid moves from the discharge port through the system, it encounters system pressure, which must be managed accordingly. The PD pump drivers are sized to handle this increased system pressure.
In this continuation, we take a closer look at the specific types of PD pumps, their inherent limitations and best practices for optimizing their performance.
Rotary PD Pumps
Rotary PD pumps move fluid through the continuous motion of internal components, offering smooth and consistent fluid flow with minimal pulsation. They are particularly well-suited for handling viscous and shear-sensitive fluids.
1. Screw Pumps
How they work:
Screw pumps use intermeshing screws to transfer fluid efficiently, ensuring a steady flow with minimal turbulence.
Advantages:
o Handles both low- and high-viscosity fluids
o Minimal pulsation ensures steady operation
o High efficiency across varying
pressure conditions
o Suitable for multiphase fluid
applications (up to 97% gas volume fraction [GVF])
Limitations:
o More complex design requiring precision engineering and machining
o Requires tight clearances for optimal performance
Best practices:
o Regularly check alignment and lubrication
o Ensure proper clearance settings to prevent wear and inefficiency
o Verify operation pressure differential is neither too high nor too low
Applications:
o Oil and gas processing, fuel transfer, wet gas compression, marine applications, chemical transfer applications and power generation
2. Gear Pumps
How they work:
Gear pumps use interlocking gears to transport fluid at a consistent rate. They create a pinch-point where fluids are pushed through the discharge ports.
Advantages:
o Simple, durable design with fewer moving parts
o Effective for moderate-pressure applications
o Well-suited for transferring lubricants and moderate-viscosity fluids
Limitations:
o Prone to internal wear over time
o Limited capability for handling gas-entrained fluids
Best practices:
o Perform regular maintenance to inspect for gear wear
o Use in applications with clean, nonabrasive fluids
Applications:
o Chemical processing, lubrication systems and fuel transfer
3. Progressive Cavity (PC) Pumps
How they work:
A single helical rotor with external threads rotates within an elastomeric stator with internal threads, allowing for smooth fluid transfer.
Advantages:
o Ideal for shear-sensitive and high-solids-content fluids
o Provides a steady, nonpulsating flow
Limitations:
o Stators can wear over time, requiring frequent replacements
o Limited pressure-handling capability
Best practices:
o Avoid excessive pressures and temperatures, which can degrade the stator
o Regularly inspect elastomer materials for wear and tear
Applications:
o Wastewater treatment, food and beverage processing and oil sludge handling
4. Sliding Vane Pumps
How they work:
Sliding vanes within a rotor create chambers that move fluid from the inlet to the discharge port. The vanes are mounted in a circular center rotor that is offset from the external pump circular casing internal diameter. This offset allows the pumping chambers to grow near the pump inlet and shrink near the pump discharge, effectively transporting the fluid.
Advantages:
o Compact and efficient design
o Suitable for low and moderate-pressure applications
Limitations:
o Not ideal for high-viscosity or abrasive fluids
o Wear over time, leading to efficiency losses
Best practices:
o Use in clean fluid applications to minimize wear
o Regularly replace worn vanes to maintain efficiency
Applications:
o Fuel transfer, automotive applications and light industrial processes
Reciprocating PD Piston Pumps
Reciprocating PD pumps operate through a back-and-forth motion, generating high pressures but often requiring pulsation dampening. As the plunger is pulled from the chamber, one set of valves opens to allow fluids from the pump inlet to enter the expanding chamber. When the plunger is pushed into the chamber during the discharge stroke, another set of valves opens forcing the fluid into the pump discharge line.
1. Piston Pumps
How they work:
A piston moves back and forth in a cylinder, drawing in and expelling fluid.
Advantages:
o Capable of handling very high pressures
o Precise flow control for metering applications
Limitations:
o Generates pulsations, which may require dampeners
o Requires regular maintenance due to valve wear and moving seals
Best practices:
o Use pulsation dampeners to reduce system strain
o Schedule periodic seal and valve replacements
Applications:
o Chemical injection, high-pressure washing, oil and gas well operations and industrial fluid transfer
2. Plunger Pumps
How they work:
Similar to piston pumps but the chamber seal is located in the chamber housing and not on the piston rod. This allows for the use of a harder seal material for greater durability and higher-pressure handling.
Advantages:
o Handles extremely high pressures effectively
o More robust for corrosive and high-viscosity fluids
Limitations:
o Higher energy consumption
o Requires frequent maintenance
Best practices:
o Ensure proper lubrication of plungers
o Regularly inspect for wear and corrosion
Applications:
o Offshore oil rigs, oil well servicing, hydraulic power systems and industrial cleaning
Comparison of Rotary & Reciprocating PD Pumps
The table below shows a comparison for each type of pump we’ve discussed.
Selecting the Right PD Pump for the Application
Each type of PD pump has distinct strengths, limitations and best-use scenarios. Screw pumps are the most versatile option, excelling in a wide range of viscosities, providing minimal pulsation and performing efficiently under various pressure conditions. For applications requiring extremely high pressure, reciprocating pumps like piston and plunger pumps are well suited but come with increased maintenance demands.
Understanding these differences is key to making informed decisions when selecting a pump for industrial applications. By considering factors such as fluid properties, pressure requirements, maintenance expectations and energy efficiency, operators can optimize performance, reduce downtime and ensure long-term reliability in their pumping systems. As technology continues to advance, innovations in PD pumps will further enhance their efficiency, making them an increasingly vital component in industrial fluid management.