Smart pumping is not just about buying a pump for your system that has a high best efficiency point or installing a variable frequency drive to reduce power consumption and energy costs. Successfully designing a smart pumping system allows the plant to operate in steady state conditions with minimal downtime for long periods of time—the key to reliability and profitability in any facility. Operating in steady state improves product quality, reduces maintenance downtime, maintains environmental compliance and impacts the bottom line. Designing and operating a smart pumping system requires an understanding of the overall system requirements, the hydraulic performance of the system equipment and the expected range of operations. Steady state is achieved when the fluid properties (including the flow rate, pressure, temperature, pH and other critical quality parameters) at any given point remain constant with time. Because the pump, process and control elements all work together to achieve the design requirements of the system, it is critical that the engineering design team knows how much flow is required, what temperature must be achieved or what pressure must be provided to a given piece of equipment. The configuration of the system, the number of loops or end users, and the location of the critical path load (or most hydraulically remote loop) will come into the calculations.The presence and effect of a siphon must also be evaluated whenever there is a change in elevation from a high point to a lower elevation.
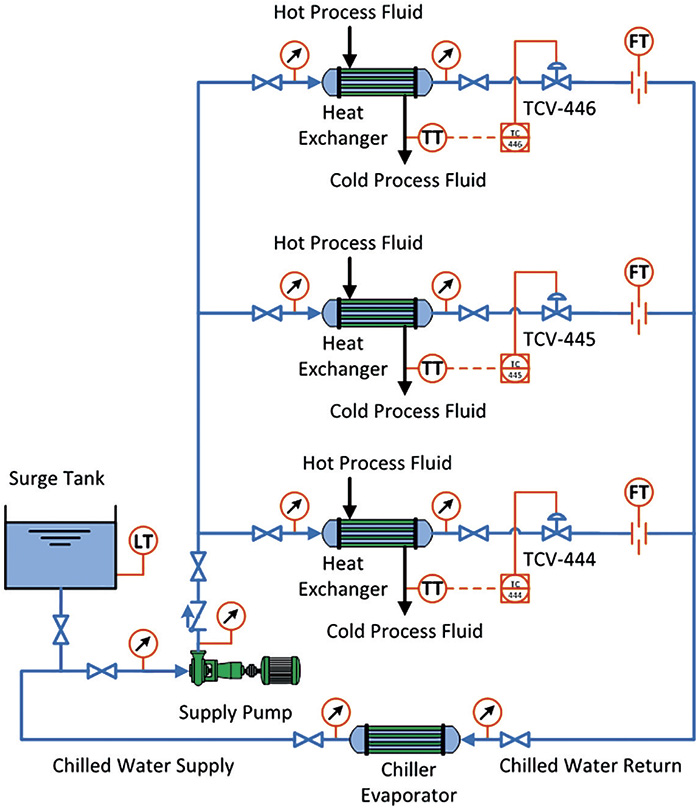