In this month’s column, we will look at a pressurized forced main waste treatment system in an industrial process facility. A major facility expansion was completed consisting of a new research and development center and new offices for the administrative, financial, maintenance and engineering departments. In addition, the expansion affected the maintenance shop, doubling the building size. Issues began six months after the completion of the expansion. The waste collection sumps for some of the buildings began to overflow. Each time a waste collection sump overflowed, an extensive cleanup was required, along with major operational changes to the buildings affected. There appeared to be no rhyme or reason causing a specific waste sump to overflow. The only buildings not affected by overflowing sumps were the two new office buildings and the expanded maintenance shop. An environmental cleanup contractor was called in to clean up the mess and to install rental sump pumps, temporary piping and storage tanks. Major operational changes were required within the affected building to prevent further overflow. The problems associated with the waste collection system caused a drop in workers’ morale, affected the operation of the entire facility and resulted in unwanted attention by the local news media. After more than nine months of trials and false starts, the underlying cause for the overflowing sumps was identified and corrected. The problem had been the subject of many managerial meetings and changes in operational schedules, as well as additional expenses for outside engineers, consultants and clean-up contractors. The remainder of this column describes how the problem was identified and corrected.
System Operational Group
A sketch of the waste collection system is displayed in Figure 1. The new office buildings, as well as the expanded shop, are noted on the drawing.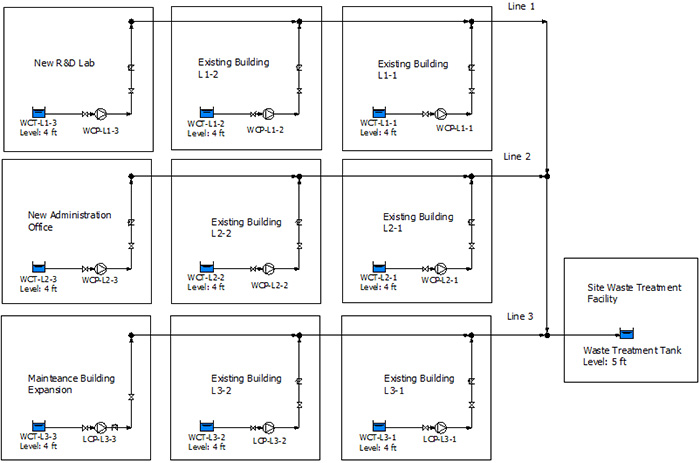