HI Pump FAQs
04/20/2018
Q. How do I determine if a motor is suitable for use with a variable frequency drive (VFD)?
A. Three major factors should be considered when determining if a motor is compatible with a VFD: the motor winding insulation, motor bearings and pump operating speed range. The reason why the motor winding insulation needs to be taken into consideration is that the typical voltage and current output of a VFD may impose high frequency “spikes” onto the motor windings. These high frequency spikes are due to the nature of the semiconductor switching technology used in VFD power circuits. As a result, it is important to know the capabilities of the motor winding insulation. Manufacturers offer motors with various nameplate annotations, such as “Inverter Ready,” “Inverter Suitable,” “Inverter Duty” and “Inverter Capable.” While all of these annotations are descriptive to a point, none of them have a standard definition across the industry. Generally, these terms describe motors with winding insulation that may be suitable for use on VFDs, but they might also include other features related to operation on VFDs. The manufacturer should be consulted directly for determining the winding insulation of a specific motor. In addition, any motors manufactured prior to the NEMA MG 1 Motors and Generators motor standard should be carefully evaluated prior to the implementation of a VFD. When implementing a VFD, proper care needs to be taken to ensure the motor bearings are protected from common mode voltages (CMVs). VFDs can cause common mode voltages when supplying power to three-phase motors. Common mode voltage is a voltage potential between at least one phase and voltage source ground. CMV can cause a buildup of shaft voltage, which can potentially discharge through the motor bearings and cause serious damage to the bearings/motor. A shaft grounding system can be used in combination with electrically isolating the shaft and motor bearings to prevent these damaging discharges. However, CMVs are not always significant enough for bearing damages, so the degree to which motor bearings need to be protected will vary from system to system. The pump operating speed range needs to be taken into consideration. VFDs vary the speed of the pump to optimize system control, usually by lowering the speed below the baseline frequency. When the motor is operated at lower speeds, the capability of the motor cooling system is reduced because the motor cooling fans produce less airflow. In some cases the motor can be operated above baseline frequency. When a rotodynamic pump is operated at a speed above the baseline speed, the power draw increase is proportional to the cube of speed increase. As a result, define the pump operating speed range to ensure the motor is not overloaded at increased speed and the motor is able to withstand decreased cooling at lower speeds. For more information regarding variable frequency drives and motors, consult HI standard, “Variable Frequency Drives: Guidelines for Application, Installation, and Troubleshooting.”Q. What is the difference between NPSHa and NPSHr, and why is it important to know these terms?
A. Supplying a pump with insufficient net positive suction head available (NPSHa) compared to the NPSH required (NPSHr) will result in cavitation. Cavitation is the formation of vapor bubbles in the pumped liquid, when the pressure of the pumped liquid drops below its vapor pressure, and later the pressure is increased above its vapor pressure, resulting in the rapid collapse of the pockets of vapor. The vapor implosions can cause serious damage to the pumping system, and typically noise and vibrations are noticeable. NPSHa is the total suction head at the inlet of the pump and is a function of:elevation difference between the liquid level and impeller eyepressure on the surface of the liquid head loss in the suction pipelines flow velocity at the suction nozzle vapor pressure and density of the liquid being pumped barometric pressure at the pump site NPSHa for a system can be calculated as shown in Equation 1.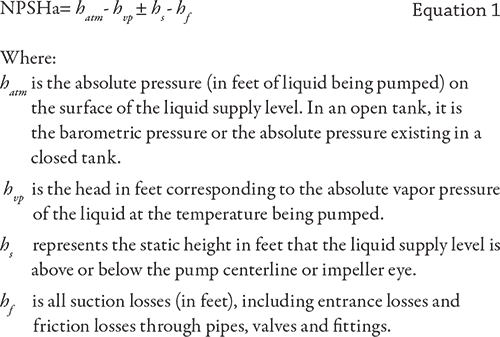
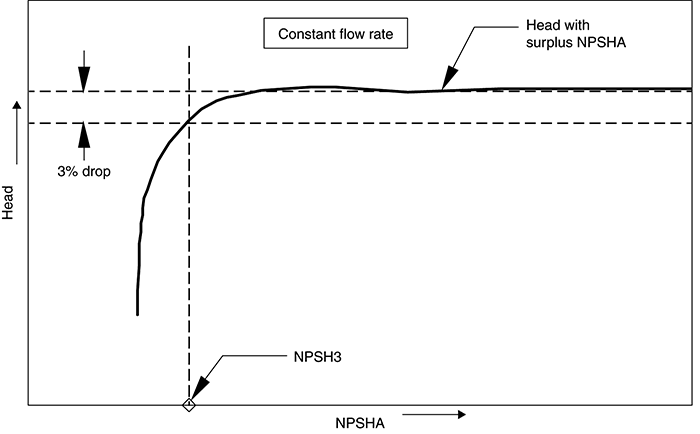
See other HI Pump FAQs articles here.