In this issue of Pumping Prescriptions, I will answer a common question I receive from readers related to system curves for boiler feed systems. Hi, Dr. Nelik, I’ve enjoyed many of your articles in Pumps & Systems, including your November 2011 article “The Basics about Pump(s)-to-System(s).” Thanks for imparting knowledge! I’ve worked in the pump industry for 12 years, mostly doing field troubleshooting of pumps. I often need to understand the system and sometimes end up drawing system curves, so I appreciate that you write about [them]. I hope you don’t mind if I bother you with a question. When calculating the system curve for a boiler feed system, you start at the deaerator and end at the boiler. Though elevation change and friction losses matter, the dominant factor is the static pressure that must be overcome (boiler pressure is much higher than deaerator pressure). The tricky part of a boiler feed system is that the temperature can rise quite a bit, so the specific gravity (SG) is not constant. In this example, the deaerator is at 239 F / 0.946 SG / 26 pounds per square inch absolute (psia), while the boiler is at 535 F / 0.750 SG / 915 psia. How do you determine the static component of the system curve when SG is not constant throughout the system? Scott Shults, P.E. Solutions Engineer, ITT Goulds PRO Services
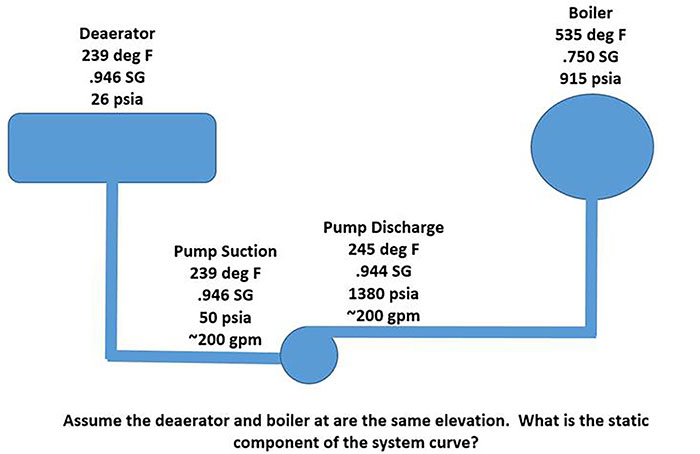