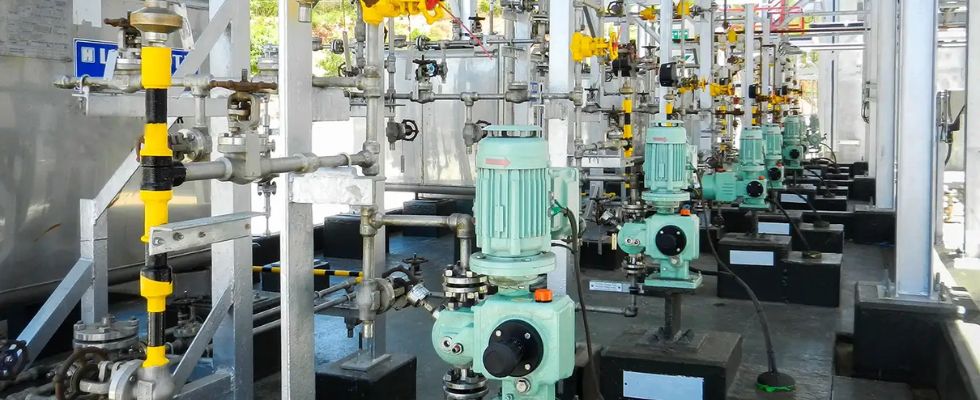
With the increasing awareness and adoption of industrial Internet of Things (IIoT) technologies, there is a growing understanding of the impactful benefits of implementing digital health monitoring solutions for industrial assets. However, one challenge many businesses face is knowing which solution to deploy, when to deploy it and for what specific application. Solutions for health monitoring can have different outputs and requirements. As such, they should be selected based on the desired outcome, as well as the criticality, complexity and value of the target asset. It is also crucial to align the needs of the maintenance team with the solution determined to be the best fit, while considering such factors as cost, ease of installation, scalability and ease of use. This decision requires thorough knowledge of the use case, including a review of maintenance records, reliability information and existing IoT infrastructure.
Below are three key steps to streamline this process:
1. Define the use case
Prior to selecting and implementing a digital health monitoring solution, it is important to define the use case and needs for the target application. When choosing the most impactful use case, businesses must review maintenance records and reliability information to find which asset(s) to focus on for health monitoring. They should also assess failure history to gauge the amount of unplanned downtime associated with those assets. By estimating unplanned downtime, companies can determine the magnitude of potential cost savings realized by an accurate health monitoring solution. This is an important element when determining the return on investment (ROI) and available budget.
2. Review existing IoT infrastructure
Another consideration includes a review of the IoT infrastructure already in place, such as any existing supervisory control and data acquisition (SCADA) system or data collection currently performed for the pumps. It is usually less common for facilities to collect vibration or other higher frequency measurements when monitoring pumps and other assets. However, SCADA systems collecting pressure, flow rate and temperature signals are common and could be helpful in assessing the asset health or providing important contextual information regarding asset operations. An additional factor regarding existing data is whether or not the historical data includes past failure events and trends, as the amount of failure data is an important part of training analysis models and establishing solution feasibility. When assessing feasibility, the number and distribution of assets also affects the potential sensor and hardware cost.
3. Consider service and maintenance expertise
One last key element is the expertise of the service and maintenance personnel who maintain and repair the pumps and other assets. In many instances, maintenance teams with a higher level of experience might not need or want diagnosis information in their digital health solution, as the early detection of trending failures would be sufficient. However, teams with less experience would likely need data to augment their knowledge and provide guidance regarding diagnosis and root cause. It is important to address the needs of the maintenance team before the project begins in order to deliver proper assistance and resources when they later tackle maintenance-related tasks.
Reviewing & Selecting a Solution
With use case requirements defined, the next step is to properly review solutions available on the market and select the right solution for the application.
Maintenance team expertise would dictate the solution type, as either early detection or one with further diagnosis capabilities and detailed information. Ideally, early detection should be automated, but some solutions provide more basic reports and visualization. These simple solutions are suitable if the maintenance team has the bandwidth or expertise to visually review the data themselves. Also, they are more cost-effective than highly automated and advanced analytics. Any available historical data with past failures plays a role in decision-making. Without past failures, it is challenging to have a solution that incorporates diagnostic insights, as the past failure historical data is typically used to train machine learning diagnosis models. Aligning the needs of the maintenance team with the type of solution required—as well as cost savings that work best for company ROI—allows businesses to rank and prioritize solutions.
Beyond the maintenance team skillset, software costs and data availability concerns, there is also the cost of infrastructure to consider, including costs related to sensors, data acquisition hardware and IT/servers, as well as installation and maintenance.
Ease of installation regarding the sensors and hardware is also essential. Businesses must weigh their options regarding wireless vibration sensors, if cabling or other constraints due to placement make wired sensors impractical. The end goal for any business going through a digital transformation journey is to have a scalable solution that monitors many assets, driving more significant improvements in uptime and productivity. Scalability and the overall time frame to deploy are both key when selecting the right solution.
Lastly, the solution should be easy to use, have an intuitive dashboard and provide key asset health information in order to best guide and support the maintenance team. Ease of use also pertains to maintaining and sustaining the solution. Benefits from improved uptime and productivity take time to realize, so ensuring the solution will be properly supported and updated for several years should be factored into the decision-making process. Ultimately, even if the solution is providing valuable insights, it will only be effective if the maintenance team continues to use—and is able to rely on—the solution.
The Right Solution for Pump Assets
Given the diversity of pumps, their systems and their applications, there is not a simple one-size-fits-all solution for monitoring them. For example, to generate actionable information when maintaining critical reciprocating pumps in oil and gas applications, several accelerometers, other additional data acquisition hardware and pressure and flow rate signals are necessary for a predictive health monitoring solution. Filtration and reverse osmosis pumps in wastewater applications, on the other hand, may only require early detection through low-cost sensors and hardware.
In general, however, early detection solutions are often more than sufficient for most pump applications and further diagnosis insights are typically not necessary. Not only this, but wireless vibration sensor offerings have come a long way in recent years and are usually low-cost and easy to install for pump applications. Larger assets whose failure would result in significant operational and financial impact might also need to be monitored as part of a larger digital transformation and uptime improvement initiative.
By following these implementation steps, selecting the right digital health monitoring solution and fulfilling needs at the onset of an initiative, businesses can ensure smooth deployment and valuable insights that will deliver impact and ROI.