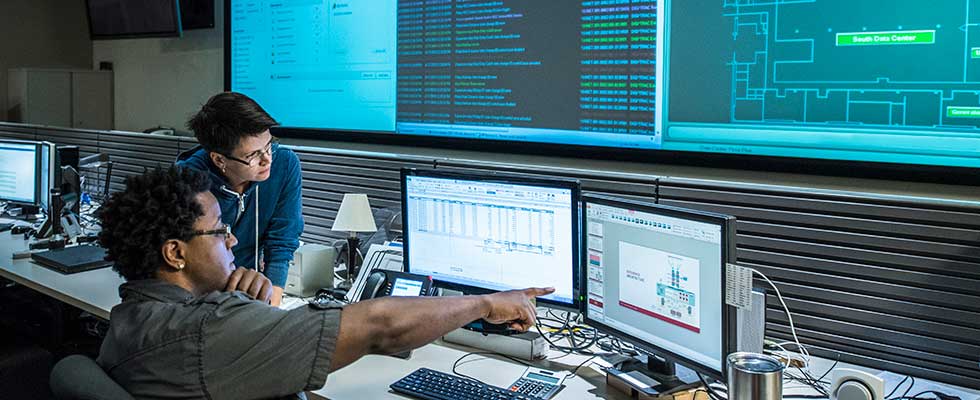
Digital controls technology and software ushered in a revolution in equipment operations. Using digital twin analytics and intelligence, organizations can avoid unplanned downtime and optimize overall operations and maintenance (O&M) costs by using accurate predictive maintenance procedures guided by a holistic view of each asset.
A digital twin is most commonly defined as a software representation of a physical asset, system or process. For assets, it may include physical characteristics, engineering specifications, failure modes and other basic information for an entire asset class. The digital twin also includes characteristics and historical data specific to an asset such as operational context, maintenance history and failure trends. Finally, digital twins include trained analytics to detect, diagnose and forecast emerging issues. In the power generation industry, these asset digital twin analytics are most used when trying to keep critical plant components in operation.
By using digital twin technology, organizations can accumulate information about the operation of physical assets. The result: Industrial organizations end up with a digital construct that knows everything about the design, the building or manufacturing, the past and current operations, and the servicing of the physical asset. This knowledge can help guide and prioritize maintenance procedures. If intelligence is added in the form of analytics, models or other algorithmic techniques, such as machine learning, organizations can fully move from preventative and reactive measures to a more optimal, fully predictive strategy.
Using digital twin software can provide multiple benefits including:
Increased reliability and availability—monitor, simulate and control an asset, process or network as an effective strategy to improve system performance
Lower maintenance costs—predict issues before breakdowns occur, order parts and schedule repairs at times that do not impact production goals
Improved workforce productivity—prioritize maintenance based on criticality and cost rather than schedule-based maintenance practices
Increased Reliability & Availability
One of the most important paybacks digital twins can provide is enabling a company to anticipate or identify failure of an asset with longer lead time to improve reliability and performance by modeling the expected versus observed states. With digital twin blueprints, analysts within the operations department can leverage both structured time-series data and unstructured data, including process parameters and condition alerts, in the context of the assigned maintenance strategy and actual maintenance performed. They can also compare operating conditions and performance with other assets.
Digital twin analytics can provide important diagnostic guidance as well, helping to rapidly assess current issues and provide an understanding of the underlying causes of failure that can help to prevent future occurrences. For example, an increase in the pump inboard bearing temperature for a condensate booster pump (CBP) indicated restricted cooling water at a power generation plant. The temperature rose as high as 126 F (52 C), with an expected value of approximately 110 F (43 C). No other bearing temperatures on either condensate booster pump showed increases.
Upon investigation, the plant’s operations team learned that the root cause was reduced cooling water flow to the bearing. After flushing out the cooling water line, the temperature returned to expected values. If the temperature continued to increase, the bearing could have been damaged, requiring premature replacement of the bearing and possibly causing a subsequent loss of production.
Lower Maintenance Costs & More
Money can be saved by power generators using digital twin technology. At one power plant, due to sea tidal conditions, the motor vibration in the cooling water pump bearings displayed an increase above the model predicted values but returned to normal during low-tide conditions. When the deviation was identified using digital twin technology, the site team performed local vibration checks, and it was determined that the pump had suffered a crack in the spider support bearing and was getting worse with continued operation.
After replacing the pump, the team was able to verify that the maintenance actions were successful by observing the actual values compared to those predicted by the model for all tidal conditions. Due to the early notification, the company was able to avoid a complete failure of the spider support bearing, which may have resulted in additional pump damage and potential pump trip. In addition, it was possible to replace the pump with the unit operating at low load to maintain condenser backpressure below unit trip levels. The advanced warning allowed the pump replacement to be scheduled and take place during a period of low power prices to minimize the financial impact of operating the unit at low load.
Another plant concern that can be avoided with early detection is equipment failure, including the cost of replacement and downtime to accomplish the fix. At one combined-cycle plant, early warning of a faulty auto-start mechanism on a condensate pump prevented early pump failure. Digital twin technology detected a spare condensate pump auto-starting multiple times per shift. After the alert, the company discovered that a discharge valve on the underperforming pump was stuck in a closed position. The site’s operations team performed maintenance on the valve. Before the notification, the site was not aware of the issue. Site operation returned to expected behavior after the maintenance was completed. Due to the early notification, the company was able to prevent premature failure of the spare pump and starter.
Improved Workforce Productivity
One of a company’s most valuable assets is its people. Making the most of their time is a critical strategic priority. Therefore, it makes sense to keep maintenance activities to the set schedule as opposed to pulling employees off other activities for an emergency. It is also a better business strategy that impacts production, quality and the bottom line.
At a combined-cycle power plant, digital twin technology detected a potential problem with the recirculation valve on a feed pump. Given the current operating conditions, the maintenance team was expecting the difference between the actual recirculation valve position and the demanded recirculation valve position to operate around 5%. However, actual values were seen to be operating as high as 8.5%. Over the next several weeks, the team monitored this issue. The valve’s performance began to rapidly deteriorate with differences between actual valve position and demanded valve position reaching values as high as 20%. The team then found a failed converter on the valve and replaced it.
Because of the early warning of this failure, the team had an opportunity to plan its maintenance action. If this issue was not corrected in time, it could have tripped the pump and caused an unexpected loss of production.
In another example, digital twin technology detected a deviation on a boiler feed pump at a combined-cycle facility. Specifically, the outboard bearing vibrations increased from 0.15 inches per second (in/sec) to 0.20 in/sec. After seeing the alert, the maintenance team discovered a damaged bearing during a routine outage and corrected the problem.
Due to the early notification from its digital twin, the team was able to correct the problem during a routine planned shutdown, preventing complete bearing failure. After maintenance was completed, the technology allowed the team to see that it was successful by observing the actual values return to the model-predicted estimate. This catch is estimated to have avoided approximately $93,000 in costs.
Harnessing Digital Twin Technology
Several software providers offer some form of digital twin intelligence and predictive analytics, though the completeness and sophistication of their technologies will vary. The most complete offerings are typically a component of a broader asset performance management (APM) solution that leverages digital twin predictive analytics but also intelligence to drive maintenance procedures and overall strategy. Alternatively, there are outsourced managed services offerings that use predictive analytics as the basis of a 24/7 monitoring and diagnostic turnkey solution.
Digital twin software is helping power generation companies to adapt to an increasingly challenging landscape, impacted by regulatory, market and technological trends. This digital transformation will help them to meet business goals.