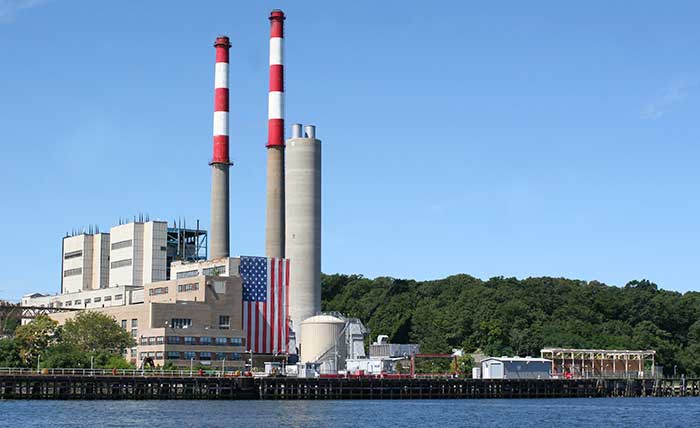
Power plant reduces energy costs by correcting valve positioning.
Siemens
11/15/2019
When thousands, if not millions, of people are relying on the reliability of a power plant to allow them to carry on their daily lives, plant efficiency and speed of response are crucial. A large power producer in the Northeast United States has a four-unit power generation plant that operates on-demand, based on bid price to the area independent system operators. Inside of Unit No. 3 at this plant, the operations department fills the drum with the controls in manual mode. Startup procedures call for the operator to provide an output to the feedwater valve at a prescribed level. Repeatability and accuracy of the valve position in response to the controller output in manual mode are critical for the drum-fill procedure.
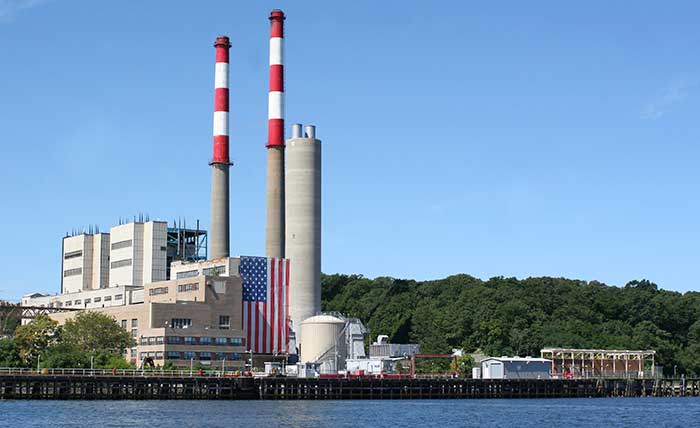
The Problem
A problem arose when the existing analog I/P (input) and pneumatic input analog positioners being used on the feedwater and startup valves did not provide repeatable valve positioning with the controller in manual. The operations fill procedures called for an output to the valve of 50 percent. The plant experienced a slow fill that delayed tie-in to the grid. Following evaluation of the issue, it was revealed that the valve was only at approximately 25 percent of travel. The analog devices were providing input that “drifted” with changes in temperature and vibration. While recalibration was attempted, it did not solve the control problem.The Chosen Solution
Eventually, the power producer made the decision to replace both the analog I/P and the pneumatic positioners with digital valve positioners. The digital valve positioners were selected because they could simplify the control circuit and eliminate the components that were drifting. The selected positioner was chosen because:- digital positioners have a history of sucessful implementation in other difficult plant applications, including burner-mounted air damper drives and attemperator valves
- on-site technical support is available for replacement mounting hardware design, installation and configuration
- of the availability of a position feedback transmitter integral to the positioner