Process industries rely on vast piping systems and connected equipment that must be sealed safely to protect their employees, profits and the environment. Safely sealing these systems can be challenging, but failure to do so can result in serious problems—including injury and death. Leaking pipes, pumps and valves can cause accidents and release substances that are harmful to human and environmental health. Leaks can also disrupt processes, resulting in downtime, maintenance problems and lost production. Because they represent an insignificant portion of the total cost of the systems in which they are installed but play a critical role in their operation, sealing devices are characterized as low-cost, high-consequence components. For this reason, they warrant more attention than they often receive. Lower quality seals may be less expensive initially, but the savings can be diminished by:
- More frequent replacement
- Downtime
- Maintenance
- Regulatory penalties
- Workers’ compensation claims
Sealing Selection
Service conditions and performance expectations should be defined and compared to published product information to select the best sealing solution for a given application. This helps eliminate a low-performance seal from a critical service or, conversely, prevents unnecessarily selecting a more costly, high-performance seal. The total cost should be considered, which includes the product itself and the potential cost of failure in human, environmental and economic terms. A simple acronym, TAMPSS (temperature, application, media, pressure, speed and size), serves as a guide for selecting the proper seal for each application.Temperature
The continuous temperature to which the seal will be exposed—including high/low excursions and any regular thermal cycling inherent in the process—should be the first consideration. The frictional heat generated by the rotating equipment will increase the temperature of the fluid contacting the seal. Temperature parameters will immediately limit the number of viable seals for an application.Application
The seal’s use and function also influence the selection. This information indicates the anomalies of an application and the special requirements for optimal seal performance. Defining the parameters of an application requires information regarding the seal’s installation location. Selecting the proper gasket for a flanged piping connection requires the following:- Knowledge of the flange types involved
- The flange’s material of construction and physical condition
- The grade of bolts used to secure it
- Whether collectively these factors can provide sufficient compressive force to affect a leak-proof seal, which is extremely important because more than 70 percent of gasket failures are attributed to insufficient load
- The condition of the stem
- If the valve’s motion is reciprocating, helical or continuous
- If a specific level of leakage must be attained to meet environmental regulations
Media
Identifying the media that will contact with the seal is imperative. Some processes use secondary media, such as food processing lines that are flushed daily with a sodium hydroxide solution. These processes require a seal that is compatible with this corrosive medium and the food being processed.Pressure
This refers to the internal pressure that a seal must contain. Most systems operate at fairly constant pressures, but as with temperature, end users must know if the seal will be subjected to pulses and other variations as a normal part of operation.Speed
The speed of a rotating shaft or reciprocating rod must be considered when selecting oil seals, bearing isolators, mechanical seals or compression packing for dynamic applications. High speeds require seals made of materials that can withstand and effectively dissipate frictional heat.Size
Standard sizes for American Society of Mechanical Engineers (ASME) flanges, American Petroleum Institute (API) valve stems, pump shafts and bore are available. Non-standard sizes are best conveyed to the sealing manufacturer in the form of dimensional drawings. Some applications may require field measurements.Deciphering Published Information
End users should consider the published specifications in Table 1 for a braided carbon fiber compression packing.They should note that the highest and lowest temperature ratings to ensure that the product is suitable for use under the service conditions. The pH range is a general guide—not a shortcut to identifying the actual chemicals that will contact the seal. Maximum shaft speeds and pressure ratings differ for rotary equipment—including pumps and quasi-static equipment, such as valves.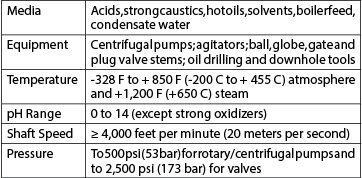
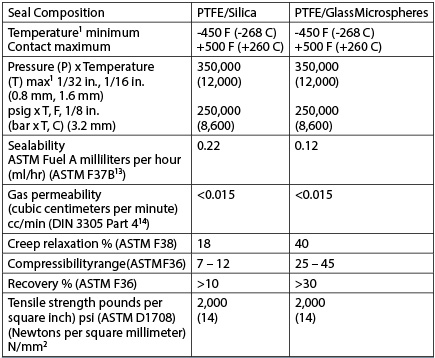
Proper Installation
Installing a seal correctly is as important as selecting the correct seal for the application. The key to effectively sealing gaskets is compression. Packing rings for pumps and valve stems must be properly seated and compressed. Pump packing should be lubricated and run in carefully to avoid burning. Many sealing suppliers provide training to ensure the proper installation of their products. If the incorrect seal is selected or the correct seal is installed improperly, the result is premature failure and leakage. Several conditions contribute to such failures—including the following:- Packing that has been burned from excessive shaft speed
- Extrusion caused by excessive equipment clearances
- Wear from abrasive media
- Deterioration from chemical contact
- Blowout as a result of inadequate or uneven loading
- Crushing from overloading and the application of grease