Due to widely diverse pump torque and speed requirements and new motor technologies entering the market, pump system engineers are increasingly tasked with matching the right motor technology with their particular pumps. Positive displacement (PD) pumps, for example, typically operate at speeds below the capability of conventional alternating current (AC) induction motors. The motors are unable to produce enough torque at low speeds in these applications, necessitating the addition of gears, belts or other speed reduction means. This solution provides the needed speed output, but also adds cost, size, weight and mechanical complexity. The gearbox is a crutch to make up for the motor’s inability to provide the required torque, which not only adds a component to the pump system, it also reduces system reliability. Despite these shortcomings, AC induction motors with gears remained the only realistic economic option for high torque, low speed pump types. Until recently a lack of alternative drive solutions has forced the PD pump industry to accept this added crutch as a necessary burden.
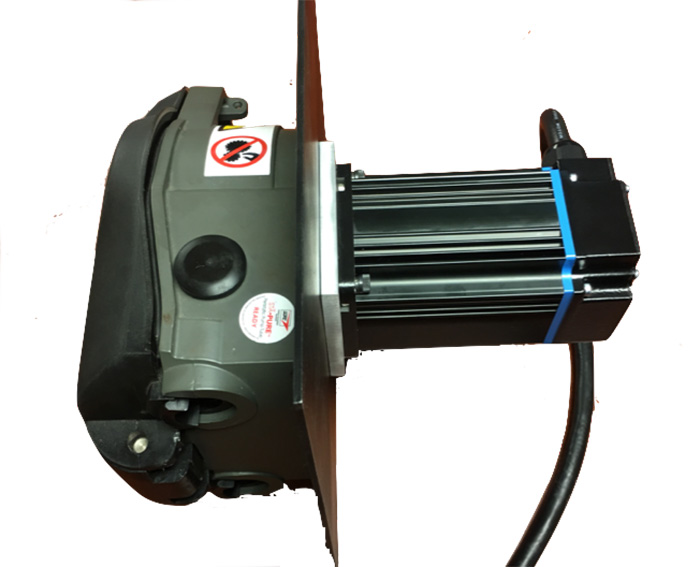
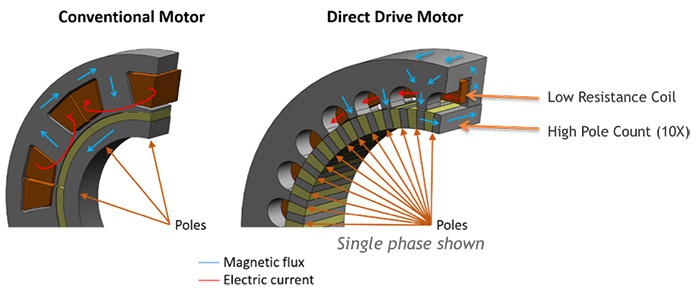
Case Study
Many PD pumps require high torque and efficiency at low rotational speeds. However, to achieve the torque needed, traditional motor technology requires high rpm, which is not conducive to the pump applications. In order to slow down the speed at the pump, a gearbox is often added to the pump motor. The addition of the gearbox usually provides higher turndown rations. However, the disadvantage of the gearbox is that it adds cost, weight, maintenance, complexity, added inventory, increased size and efficiency losses.The Solution
PD pump manufacturers are discovering that advances in direct drive motor technology can overcome these obstacles and outperform traditional motors. Although previously used in various high torque, low speed applications, these direct drive motor advances have recently entered the pump industry. Through wider ranges and lower speed capabilities, the direct drive motor technology is able to remove the speed reduction gearbox used in most positive displacement pumps, reducing the pump system size and maintenance costs while increasing efficiency, with much lower power consumption.The Results
A pump company and motor company collaborated to bring these motors into the pumping industry. The PD pumps with integrated direct drive motors have provided improvements in pump performance, while decreasing the pump manufacturer’s motor cost. In comparison to the incumbent AC-induction gearmotor system previously used, the direct drive system weighs roughly 35 percent less. Furthermore, by eliminating the gearbox, the efficiency of the pump system has increased by more than 30 percent. However, the most impactful advantage realized by switching to the direct drive system has been the increase in turndown ratio. The legacy gearmotor systems had a maximum turndown ratio of 20:1. This resulted in the pump manufacturer having to carry many different combinations of motors and gearboxes in order to meet the wide variety of their customers’ needs. The direct drive system (pictured in Image 1) has a turndown ratio of 2000:1, thereby covering an incrementally wider range of speeds and enabling a single direct drive to replace more than 45 different motor and gearbox combinations. Well suited for the requirements of PD pump applications, the direct drive motors are providing pump engineers a welcomed solution to legacy pump obstacles.