The U.S. Environmental Protection Agency (EPA) has adopted a comprehensive national program to reduce emissions from diesel engines. Implemented in a series of progressively more stringent tiers, the new standards require reductions in carbon (soot), hydrocarbons from fuel and lubricating oil, metallic particles, and watery sulphuric acid. Until this year, diesel engines have had to comply with the Tier 4 Interim standard, which specified lower emissions but did not reach the full goal. Beginning Jan. 1, 2015, the new Tier 4 Final standard requires all new diesel engines used in off-road equipment to meet substantial reductions in emissions. To meet the full Tier 4 standards, diesel pump package manufacturers are required to use engines with advanced emission controls. Tier 4 requires all diesel engines to have reductions in particulate and nitrogen oxide emissions. While previous generations of diesel engines could achieve the lower Tier 3 and Tier 4 Interim standards by managing emissions within the combustion chamber, Tier 4 Final’s more stringent standards require an after-treatment device.
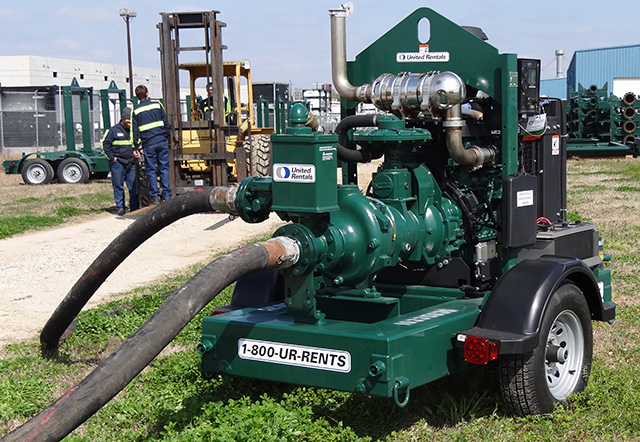