Who determines where pressure gauges are located in a pump system? How close to the pump should they be, and what happens if these rules are not followed? For a small pump system, the impact on the evaluated resultant energy consumption (real versus assumed) may not be significant. However, for a large unit, the penalty on evaluated efficiency and perceived or real wasted energy can be in millions of dollars. A good pump requires more flow and pressure while using less power. This type of operation indicates that the pump is running at or near its best efficiency point (BEP). BEP is the flow at which all the losses are the lowest. When a pump operates at or close to its BEP, it is more efficient, and its total cost of ownership decreases. The formulas in Equation 1 are commonly used to calculate efficiency from measured parameters such as pressure, flow and power.
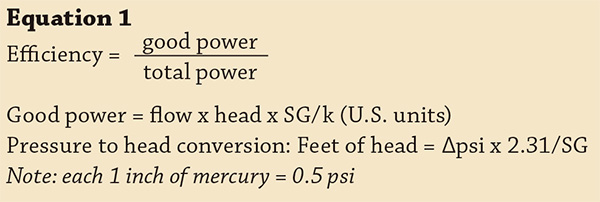
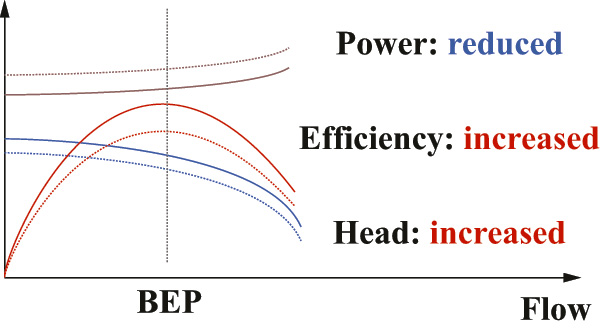
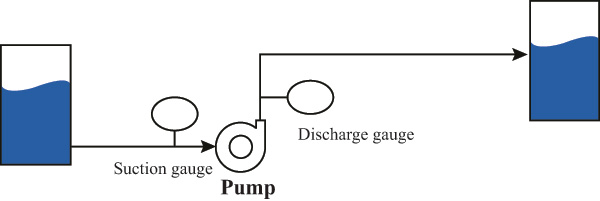
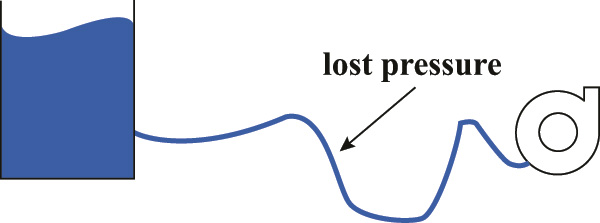
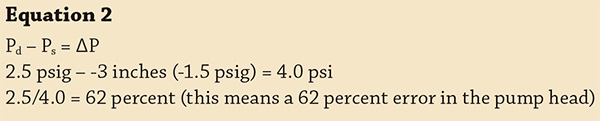