I have been involved with horses for most of my life. There is a cliché that plays over in my head from the movie “The Horse Whisperer.” During one scene, Robert Redford says, “These people don’t have a horse problem… what we have is a horse with a people problem.” When I witness all the pump problems in the field that are directly caused by misalignment issues, I think about this cliché over and over and think to myself, it is not the pump’s fault. With an increasing and somewhat alarming frequency, I consult with end users who assume their new pump is perfectly aligned to the driver, so they do not align prior to startup. Just plug it in and run it, is the new modus operandi. Later when the real and expensive pump problems appear and I point out that the issues are caused by a bad alignment, the end user questions, “Why wasn’t this performed at the factory?” Spoiler alert, it was done at the factory, albeit not a precision alignment and the driver has since moved for a multitude of reasons. I strongly recommend that a pump be aligned at least seven to nine times, and four of those checks should be before it is even started up. Rotating equipment experts and engineers that work at “best in class facilities” with equipment records reflecting high reliability and long mean time between failures (MTBF) will agree. This article is not a step-by-step procedure on how to accomplish the actual alignment; there are plenty of resources that can help you with that. The purpose of the article is to advise (and hopefully convince you) that, first, the alignment needs to be conducted several times over the course of installation and, secondly, of its importance.
Why Spend the Time to Perform an Alignment?
When you look at all the reasons why you should perform an alignment, you will find lists that cite shortened mechanical seal, bearing and coupling life, premature wear on the pump, unacceptable vibration, shaft failures, noise, inefficiency and associated additional power costs as the top reasons. But I would state all of these issues and more, including expensive and unscheduled downtime, all translate to the bottom line, which equal total cost. If you fail to properly align the driver to the pump, you will pay more money over the life of owning and operating the pump during its now-shortened life span. (The market frequently refers to this matter as TCO, also known as the total cost of ownership.) There is also plenty of supporting documentation in the market that a misaligned pump will require as much as 7 to 10 percent more electrical power, and I have heard of several cases where it was higher than 15 percent. If the pump could talk, it would state, “Pay me a little bit now… or pay me a lot of money later.” Or perhaps the succinct: “Time is money.”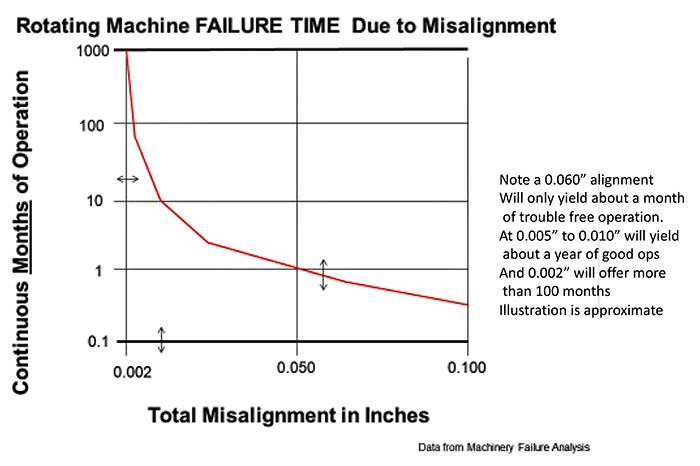
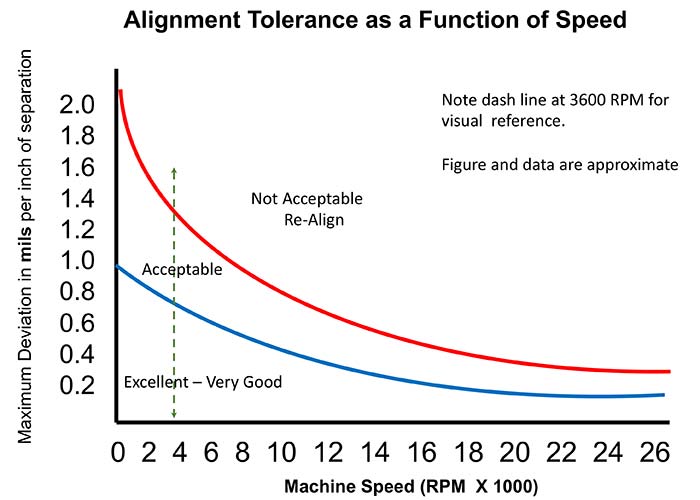